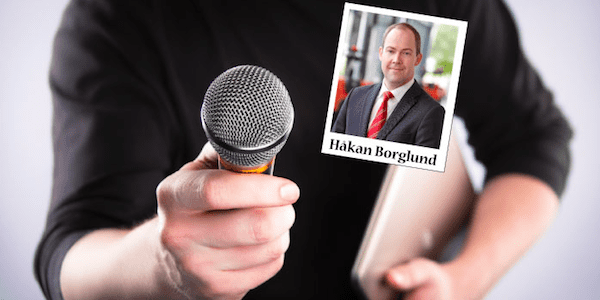
How Toyota Material Handling applies principles of lean IT
INTERVIEW - Håkan Borglund, CIO of Toyota Material Handling Europe, speaks with Planet Lean about Toyota principles and the role of lean IT at Toyota Material Handling.
Interviewee: Håkan Borglund, CIO, Toyota Material Handling Europe
Planet Lean: How does IT support operations at Toyota Material Handling Europe?
Håkan Borglund: First of all, it’s important to say that TMHE is formed by two organizations. The supply organization, which has three factories of material handling vehicles (in Italy, France and Sweden), needs production and quality systems that run seamlessly, and that’s a big part of my job.
But there is also the need for central support for our marketing, sales and services functions, which cover 30 local country offices.
This IT infrastructure is standardized and common across Europe. There is a lot of collaboration between teams in different countries: IT supports this in a number of ways, for example when we hold online meetings.
PL: How do Toyota principles apply to IT functions, from product development to supporting operations?
HB: We have lots of internal resources to rely on. Because of our company philosophy everybody working with us has to take the basic training in TIBP, Toyota Industries Business Practices, which means that we can enjoy the benefit of having people already familiar with continuous improvement, A3 thinking, etc.
Thanks to this, we don’t struggle to get people to understand the principles. They are already part of our culture. But when it comes to the implementation, we follow a PDCA approach and, depending on the circumstances, we use agile, scrum, the waterfall model, and so on.
PL:In your opinion, how is the relationship between lean IT and agile evolving?
HB: I consider them as two different approaches. I don’t see a clear way forward for lean I.T. yet. We need to create a framework, a methodology if you will, for it to be used in a development environment.
Lean I.T. needs to be developed further. Of course, one could say that agile is lean because it’s all about efficiency, but this only means using lean as a label. If we are talking about having a software development process that is mapped out from A to Z and that works, then I don’t think we are there yet.
PL: Can you tell us a bit about Toyota I_Site, TMH’s fleet management software?
HB: It originated from working with preventive maintenance. A truck needs to be maintained at regular intervals, and we found it would be good for our planning process to know in advance exactly when a truck would need servicing.
We thought, what if it was the truck that gives us that information? We developed a black box that picks up data on the status of the battery or of the truck and sends it back to a central database.
After we learned that the customer thought this system would work well for them too, we developed the reporting function. Our clients can now go online and print out a report that gives them visibility of data and tells them if, for example, anyone needs to renew their license or if a truck needs maintenance.
This year we have come to the third version, which has alerts. The truck itself will tell you if it bumps into something: we can arrange for the customer to receive the message in whatever formats they want.
I_Site is a strategic product for us and we will continue to develop it to include more functions.
PL: Is visibility one of the main advantages of a working IT infrastructure, then?
HB: Absolutely. The point is that we are already sitting on most of the data, it’s just a matter of pulling them when needed. I recently saw a great example at TMH France, where the team uses a huge screen that shows the current KPIs, pulling the data from the service management system.
THE INTERVIEWEE
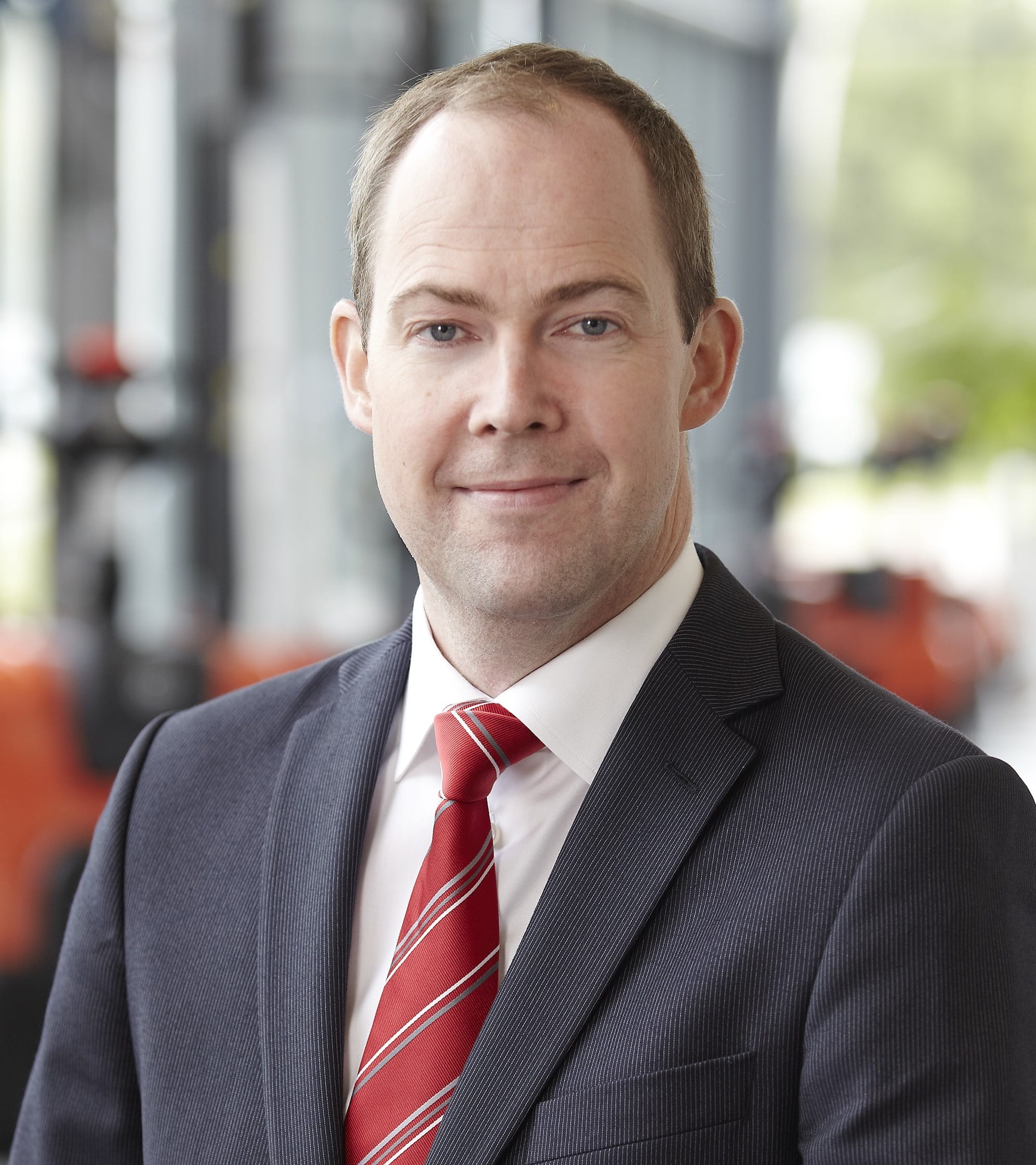
Read more
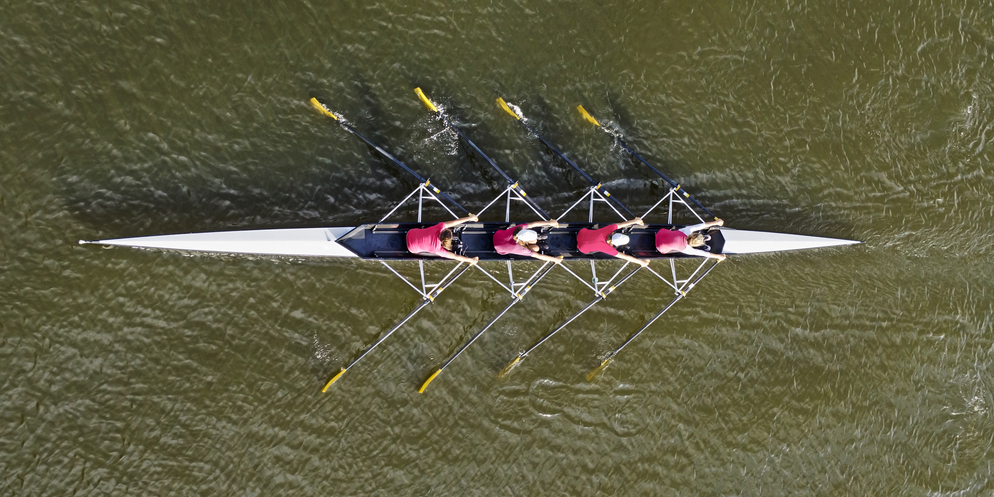
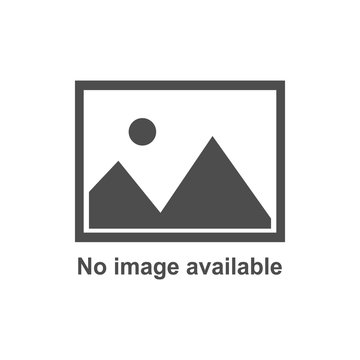
ROUND-UP – Standardized work, which lies at the foundation of the TPS house, is a necessary component of a lean transformation. This article looks at the best content on this topic from our archives.
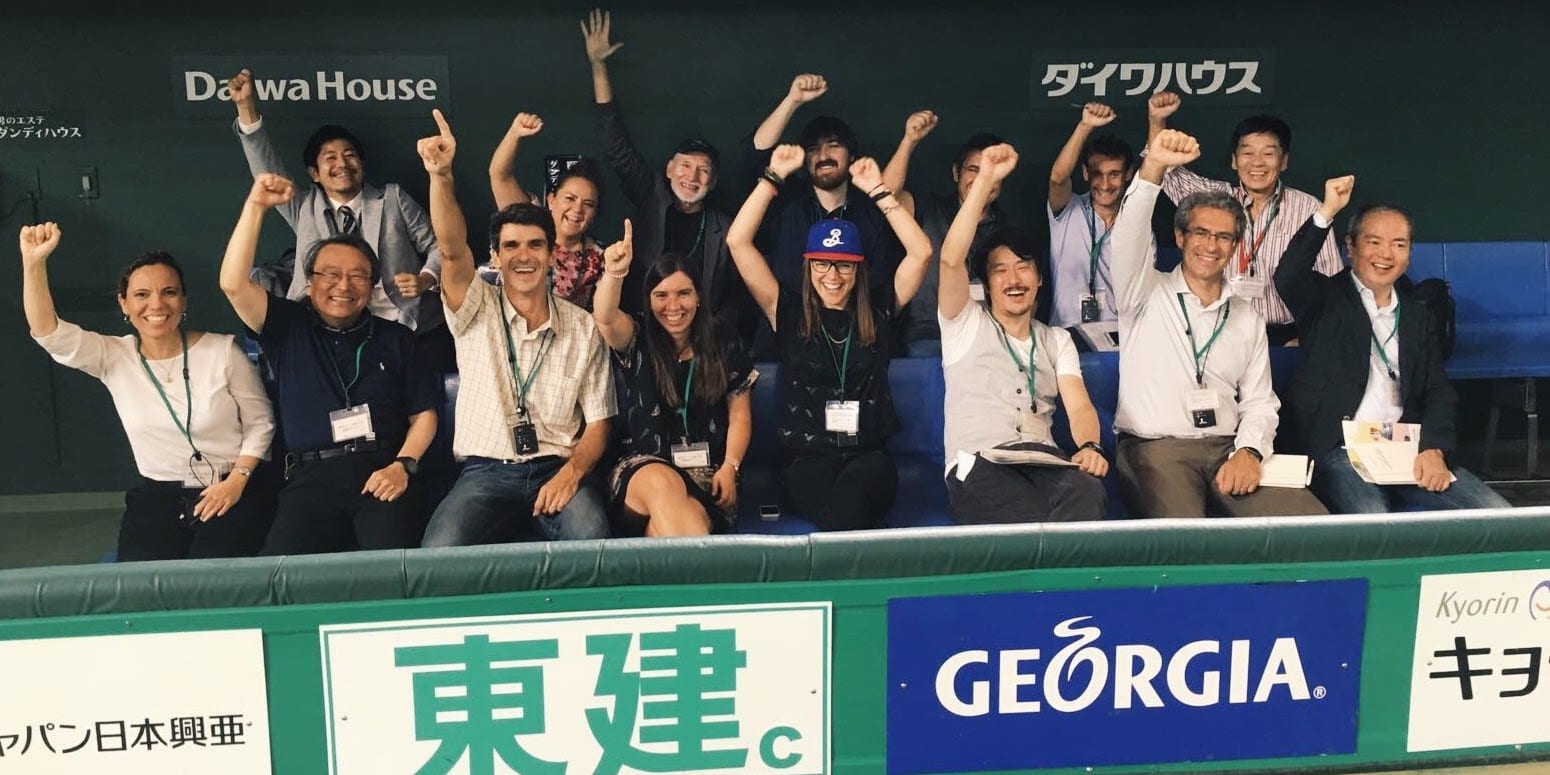
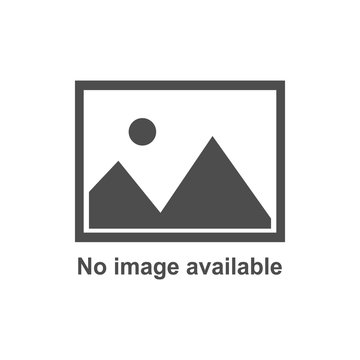
FEATURE – Study tours in Japan are an increasingly popular learning tool for lean practitioners. The author reflects on the first ever tour she ran and on what it left people with.
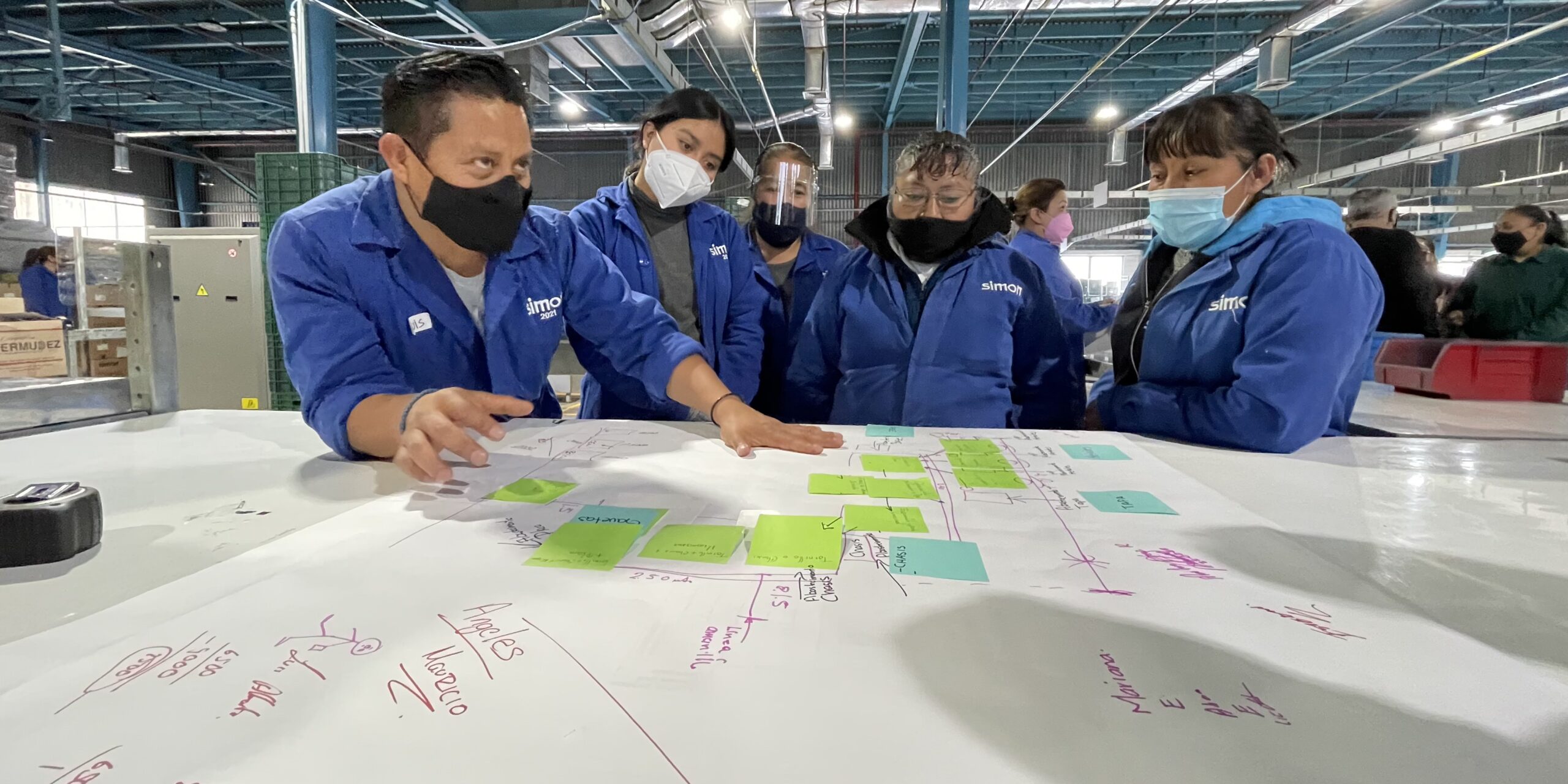
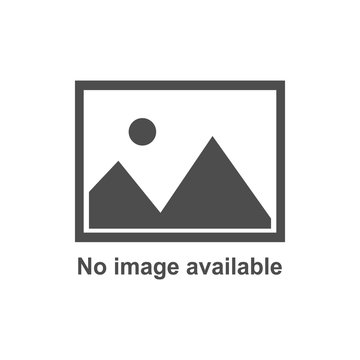
CASE STUDY – Starting in January this year, the Mexican plant of this manufacturer of lighting and electrical solutions has initiated a lean transformation that has already led to impressive results in terms of productivity.
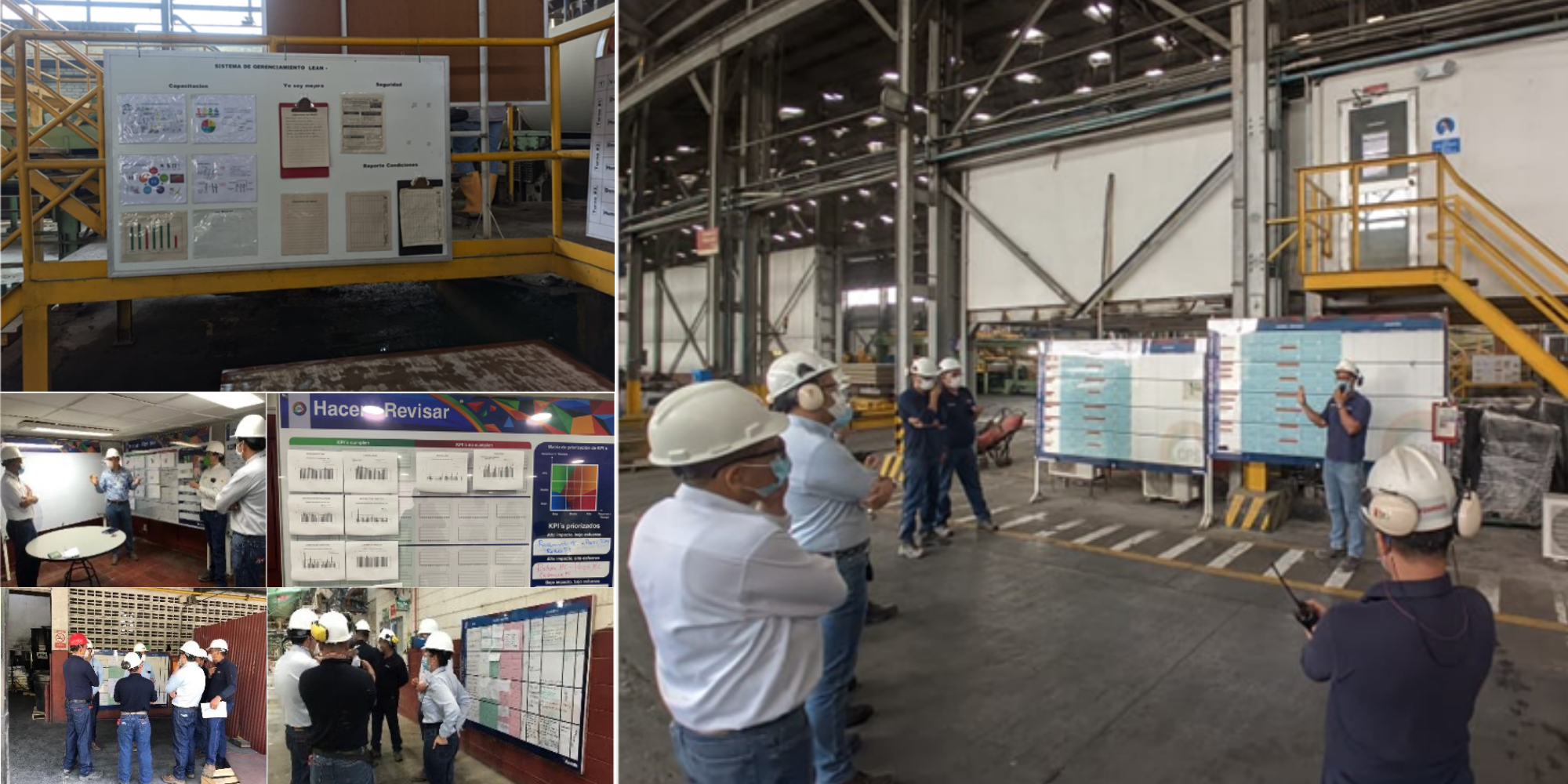
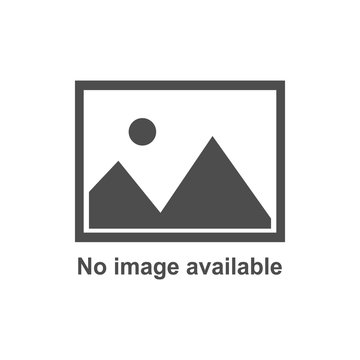
CASE STUDY – For the past year, Elementia Materiales, a producer of materials for the construction industry, has begun a lean journey that’s already brought impressive quality results.