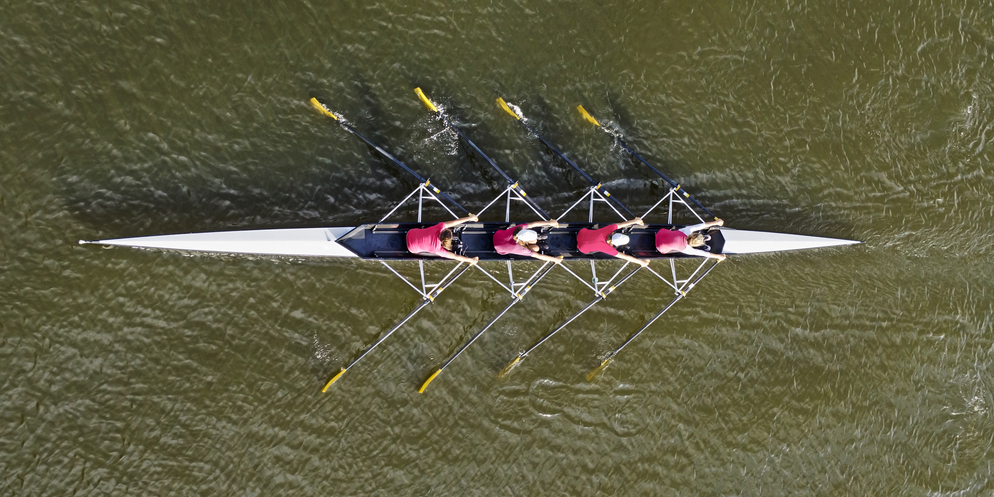
What is standardized work?
ROUND-UP – Standardized work, which lies at the foundation of the TPS house, is a necessary component of a lean transformation. This article looks at the best content on this topic from our archives.
Words: Roberto Priolo
If stability is a precondition for the improvement and success of a business, standardized work is a precondition for stability. To have one agreed-upon way to perform the work consistently means to develop the ability to easily identify problems (as in, deviations from the standard) and ensure quality in the process.
From agrobusinesses to medical practices, from hardware stores to restaurants chains, the benefits of standardization are well documented. Yet, some misconceptions still exist, and many businesses struggle to stick to the standards they create. So, let’s tap into the Planet Lean archive to see if we can provide some clarity on the subject.
First, a definition. According to the Lean Lexicon, standardized work consists of “establishing precise procedures for each operator’s work in a production process”. Its benefits include a reduction in variability and injuries, an easy way to document the process and train new people, and the provision of a starting point for further improvement.
Even though some assume that once a standard is established the work is done, standards aren’t set in stone. As more and more people embrace continuous improvement as a way of thinking and acting, better ways of doing the work are identified and the standard is updated through kaizen to reflect changes in the circumstances of and around the work.
In this article, Keith Edwards of Toyota, Section Manager at Toyota Motor Manufacturing in the UK, said: “The standard is very much the beginning of the journey. If you try something new and it doesn’t work, the worst thing that can happen is that you go back to the original standard. This limits the risk because all you are doing is improving an already-existing standard.”
Of course, as with many things in lean, the hardest part about standards is to maintain them and ensure people follow them. This is a responsibility of leaders, who play a pivotal role in creating a culture in which standardization can thrive. According to Malgorzata Jakubik and Robert Kagan of Lean Enterprise Institute Polska, to ensure adherence to standards without alienating people, a leader should: gather data to avoid “attacking” someone when they might not even know the standard exists; reaffirm the importance the person goes back to the standard by explaining why the standard exists; and commit to following up with the person later. More on this here.
In this intimate story, Tracey Richardson shares her own experience with standards at Toyota and explains the role of her trainer at the time. “I truly believed the leaders felt setting a standard without the proper discipline behind it was like having no standard at all, and that this would have a harmful effect on culture and morale. This was central to the thinking of Taiichi Ohno when he placed standardization at the foundation of the TPS House. If everybody follows the same process in the same sequence, discrepancies (when they arise) are much easier to identify and correct,” she wrote.
For a guide on how to apply standardized work, check out this article by René Aernoudts.
WHAT ABOUT CREATIVITY?
There is a common misconception that standards stifle creativity, imposing on people one way of doing things that might not allow them to express their talent. This is far from the truth. In fact, it is quite the opposite: standards focus on the mundane, repeatable parts of the work, releasing extra time (and energy) that the worker can then use to set its creativity free.
According to Ian Hurst, a Senior Specialist at Toyota UK, “standardized work is not a straitjacket, but a framework. Within it, there is always room to move, to find that better way I mentioned above. Before you can do that, however, you need to build a certain level of trust on the shop floor. Our people know that if their job is improved and time is freed up, we will always find more value-creating activities for them to do.”
In this interesting article, Alessandro Piccolo explains how even undoubtedly creative professions like DJs and chefs can benefit from the use of standardized work.
STANDARDS FOR LEADERS
While it was not originally intended for leaders, standardized work can be used as a blueprint to organize a leader’s agenda and to promote the right behaviors (for instance, participation in a weekly meeting or in a gemba walk). In this insightful piece on standard work for senior leaders, Michael Ballé, Denise Bennett and Peter Handlinger say: “We believe there are some specific skills that leaders can learn to deepen their understanding of lean management, to change others by changing themselves through daily practices, and to transform their organizations.”
Examples of lean leaders who “walk the walk” and leverage leader standard work (LSW) to ensure the “leanness” of their own behaviors about. One such example is Dr Frederico Pinto of Instituto de Oncologia do Vale in Brazil, who “goes to the gemba daily and participates in at least one rapid improvement event each week (as per his standard work). The hospital has also implemented a system – called kaizen shifts – under which there are special times of the week during which people work on their A3s, and Pinto makes sure he coaches at least one person on an A3 every week.”
Another great example is Sharon Visser. When Sharon ran a Toyota dealership in Botswana, she was meticulous in organizing her day according to what she considered to be her role as the leader of the organization. Standard work was her go-to tool for that. “Many people going into management feel that the work content is too varied to fit into a standardized work document. My gemba walk was something I managed to fit in every day – often twice a day. Whenever I came back from a trip, the gemba was the easiest way for me to catch up with the current situation, greet my team and let them know I was around.
You might be thinking that you do not have time for standard work. My answer is that if you don’t have standard work, you will never have time,” she says here.
THE AUTHOR
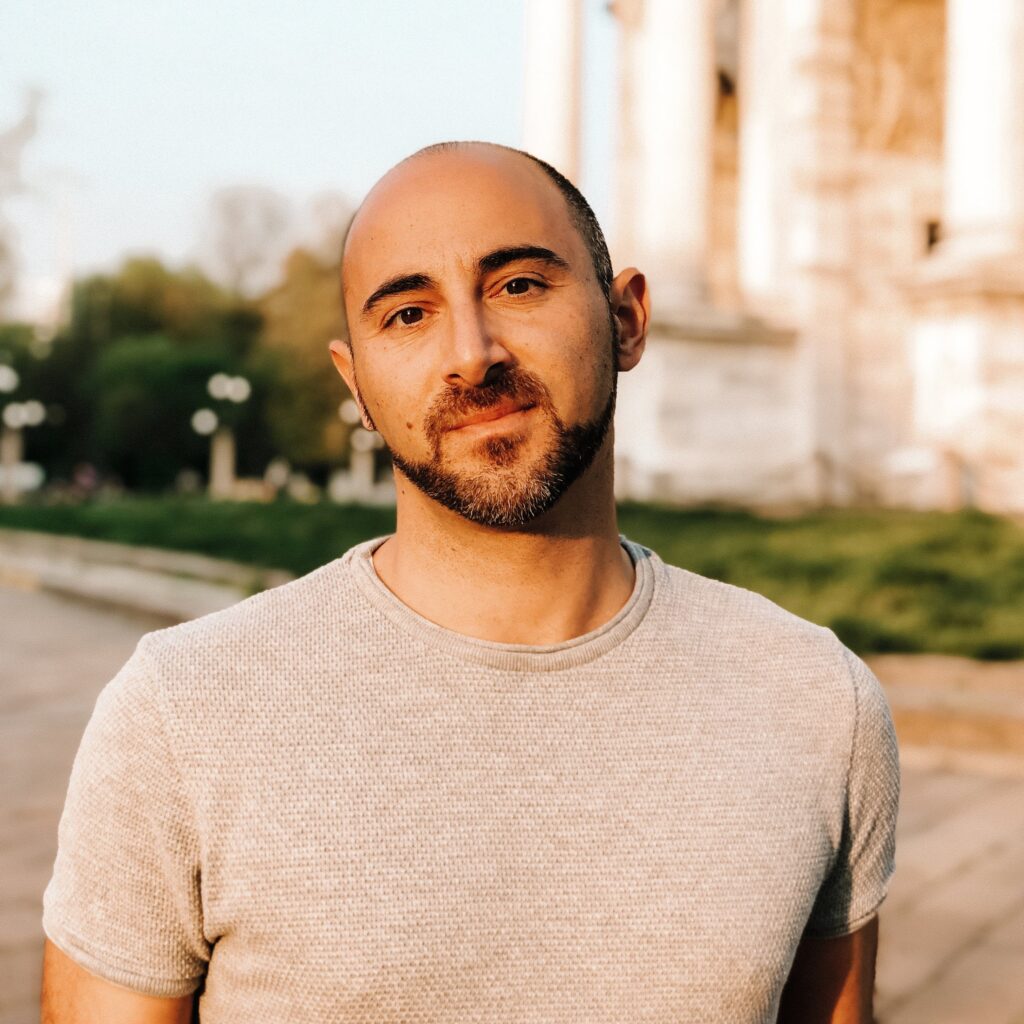
Read more
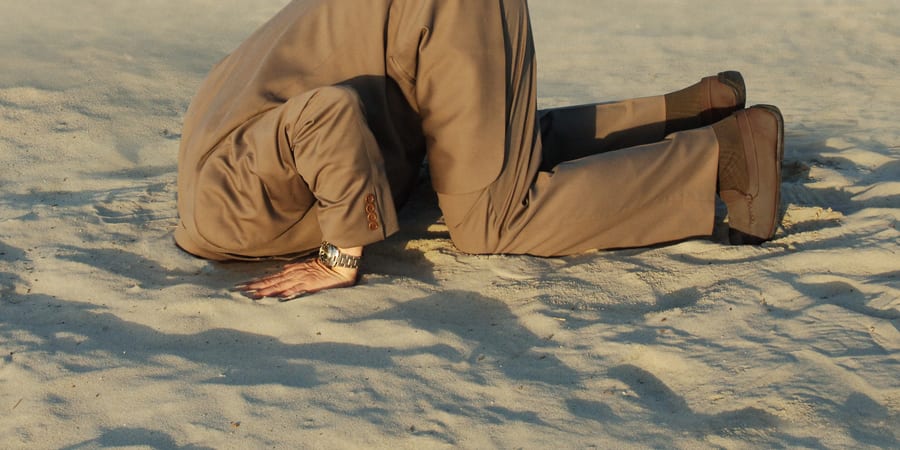
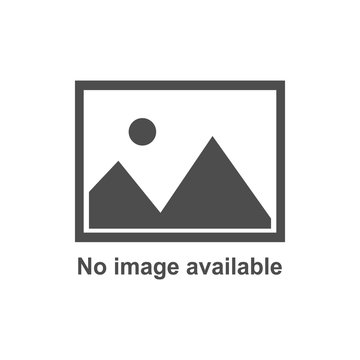
FEATURE – CEOs need to see people as assets and transform their companies’ product development systems if they are to tap into the full potential of a lean strategy.
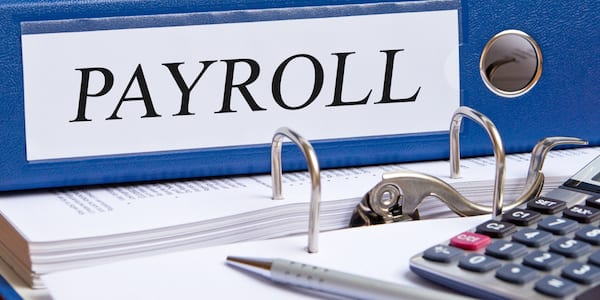
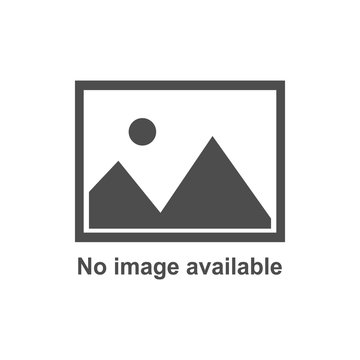
COLUMN – Finance is a critical function within a firm. Yet, lean thinking seems to struggle to make progress in this field. Following a workshop with Nick Katko, the author of this article sees an opportunity.
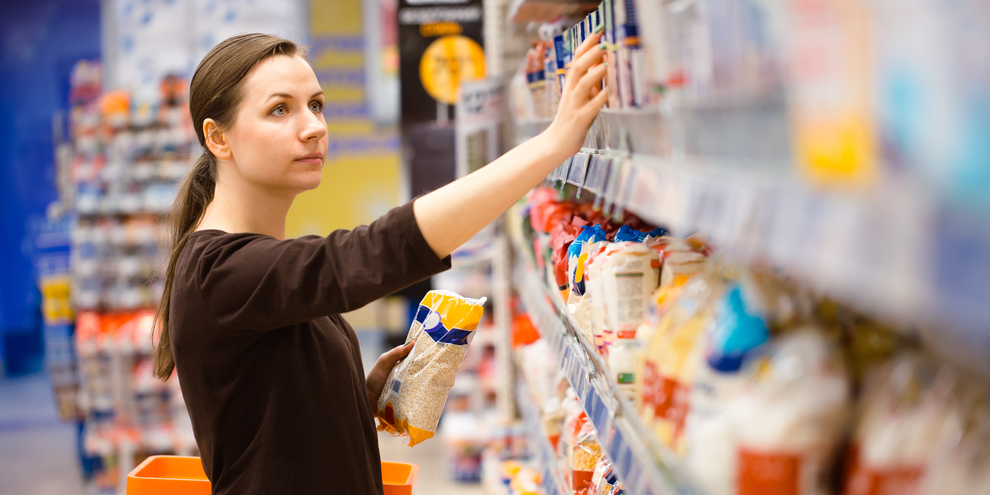
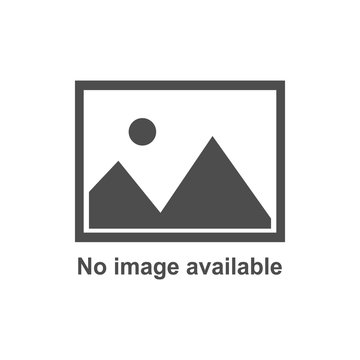
FEATURE – A lean retail experiment: Carrefour Group in Brazil has started a lean journey to rapidly adapt to market changes and reach excellence in the delivery of value to customers.
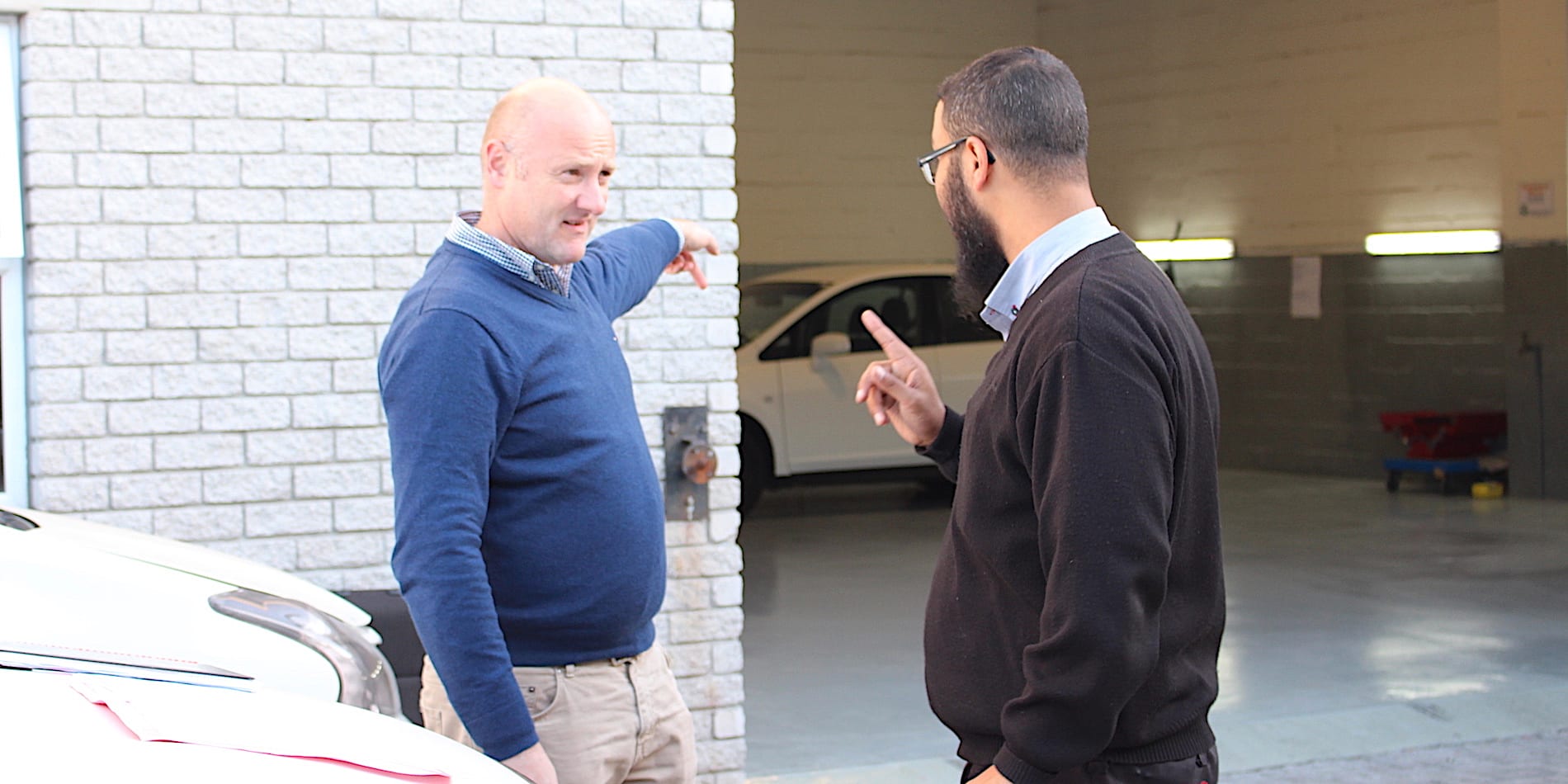
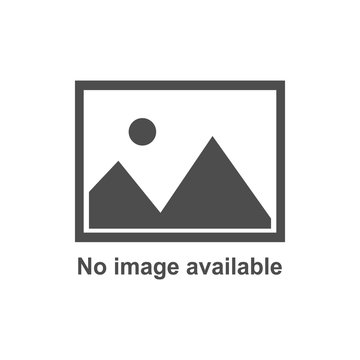
FEATURE – The role of the coach in a lean transformation is an often-debated topic. The author discusses his experience building the architecture of the Halfway turnaround.