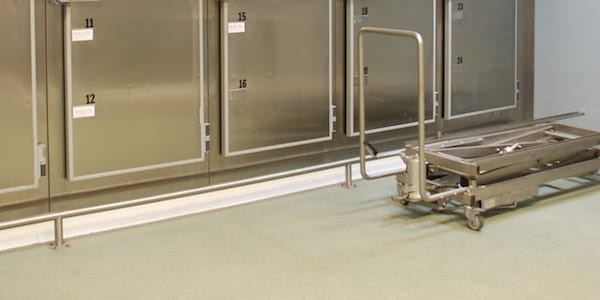
Lean principles in a forensic medicine institute
ARTICLE – The Institut de Medicina Legal de Catalunya has learned that employee engagement and lean thinking can shake up even the stiffest of the public sector's working environments.
Words: Ignasi Galtés, forensic doctor, Institut de Medicina Legal de Catalunya
Our ability to overcome resistance to change is what will determine whether an approach will work and an improvement will stick. Every time you successfully introduce a new standard, no matter how small, the work improves a little, and that is a crack in the system (remember the Trojan Horse?) through which every other improvement will seep in.
Achieving a lean turnaround seems to be particularly hard in the public sector, where the environment is often the most adverse to change that you can imagine. At the Institut de Medicina Legal de Catalunya, we have managed to make lean happen through the involvement of our people.
The public sector (not just in Spain) is known for its many problems, of which two seem to be particularly hard to solve: first of all, the way we do things often makes no sense and we typically don’t know why we act a certain way. Secondly, bureaucracy inevitably makes our processes cumbersome.
In this context, lean can help us by rationalizing and speeding up our processes and getting rid of red tape.
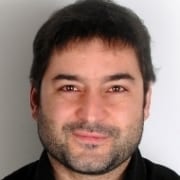
"We had been trying to introduce lean for years, but couldn't: first of all, many at the Institute believed that the methodology only applies to automotive and didn't understand that a process is a process, a product is a product, and a customer is a customer. Explaining all of this was very hard, and the only way to do it was through education.
There were other challenges. To begin with, roles and processes in the public sector tend to be very compartmentalized and people don't always have the will to take part in cross-functional initiatives, which is of course opposite to the flow-based horizontal view of a business that lean thinking advocates for.
Finally, as a leader you must strike the right balance between helping people to understand, providing them with instructions and direction, and not giving the impression that the entire lean experiment is nothing but a top-down initiative."
Carles Martin, subdirector, IMLC
In our job at the IMLC, the concept of “value chain” is particularly meaningful, because the documentation we deal with is not only important, but it is also confidential. We must be able to guarantee traceability at all times: we are talking about judiciary proceedings, and a little doubt at any moment can have a big impact on an investigation.
The facility I work in is rather small. We carry out about 600 autopsies per year. Lean has helped us hugely there, through the introduction of visual boards and tools and by planting the seeds of a new culture.
Take a look at the before/after pictures below. Shocking, right? Even what today might look chaotic was much worse before lean was introduced.
[widgetkit id=37]
The truth is, working in an untidy and messy place is not pleasant. And there is a lot of this in the public sector – granted, not all civil servants deal with dead bodies and organs, but you get the idea.
People’s willingness to participate in our initiative to improve things was the main problem at first.
As much as we tried to convince them that this was going to improve things, they had to see it for themselves. So we decided to introduce morning meetings that took place around three boards: one for problems, one for improvements, and one for failures. Every morning, during a ten-minute meeting, people could suddenly see the problems that were occurring and tackle them immediately.
It sounds promising, but the idea failed soon after it was introduced. Instead, Dr Carles Martin suggested we organized training to teach people to identify problems, and I can say that in that we have definitely succeeded.
"We tried several tools. Some worked for everybody, some didn't. The boards, for example, were perceived as part of clerical work rather than something that could help people in practice. Additionally, they were seen as a way for management to control workers.
While simple, all the tools we used were actually oriented towards people engagement."
Carles Martin, subdirector, IMLC
The examples of our improvements are extremely simple, but I think they were very clear actions for people to understand. As a matter of fact, by optimizing and improving our processes, we have been running the entire facility without an administrative office for a whole year (due to a maternity leave).
We started three years ago with lean and the vast majority of our improvements have had a positive impact on the daily practice.
Some of the main actions we have taken include: reorganizing autopsy reports, guaranteeing a better control of the fixation of body parts (histology), controlling the consumption of formaldehyde, and the use of mortuary refrigerators.
It’s great to see that all these improvements are being sustained, which means that we were able to motivate people.
THE IMPROVEMENTS
One of the biggest problems our facility was facing was unidentified bodies, which ended up staying in the morgue for a very long time because nobody claimed them (it’s often illegal immigrants without residence permits nor family in the country). Now, with the introduction of a simple system of color tags, technicians know right away what the situation of the refrigerators is.
A red tag indicates that a body is still awaiting autopsy, while a black tag flags up a problem. Unidentified bodies that have already been autopsied but are not claimed by anyone cost us a lot of money: the black tag reminds the administrative office that they have to pick up the phone (we even installed a special black phone they can use just for that) and start doing all they can to find somebody who will come to collect them.
In the morgue, life got easier for security guards, too, after we put a system in place to level the consumption of electricity for each of the refrigerators. Now they know what temperatures each machine should be at and which ones are on or off. Prior to this, refrigerators would be on all the time for no reason.
Another messy (or, rather, disastrous) situation was in the room where we keep the boots we use during the autopsies. You can see pictures of before and after in the gallery above.
The room was always very dirty: there were at least three times as many boots as we needed, placed randomly on a plastic shelving unit. The floor was sticky and finding everyone’s boots was basically a mission impossible because the boots' rubber shafts would flop to one side. We introduced a very simple system: strings hanging to the ceiling, which hold the boots up above the floor while of course holding their shafts up. This way we could get rid of a lot of boots we didn’t use, and the room was once again easy to clean. Today it’s perfectly tidy.
In the autopsy room, we placed a little desk by one of the walls so that medical examiners can avoid taking notes on the big counter next to the body they are examining. We designed a room that is optimal for work: staying by the new desk, by the feet of the body, you can see both cadavers at the same time (there are two tables in the room) and take all the time you need to reflect. You are also not working on a dirty counter, and - more importantly - you are not bothering the other doctor working in the room.
We also put up a board to help coroners make sure that weigh and other important information are recorded for all the organs. This way it’s impossible to forget.
We have also improved the changing room. The police often come here, so we have started to purchase scrubs of two colors, one for doctors, one for visitors. This was an improvement the technicians themselves suggested: they proposed it, created it, improved it and they are now sustaining it.
A system to check the consumption of formaldehyde is also in place now, which tells us when a drum is opened and is about to finish. It’s been very successful, and we are going to try and take this to our sister facility, the larger Ciudad de la Justicia.
A lot of these changes are just common sense, and they are very simple, but they have really made a huge difference in the daily working lives of people here.
On the investigations side of things, lean’s biggest contribution was in the changes in how we handle autopsy reports. We receive bodies from eight judicial districts. Up to three years ago, when a medical examiner completed an autopsy report they would put it on a tray placed on a desk, where they accumulated.
There were, therefore, constant delays in the delivery and receipt of the reports. Our colleague in the administrative office would only send them out when the pile was big enough to catch her eye. There was no flow of exit for these reports. It was a bottleneck, pure and simple.
We found a way to calculate the number of entries we have for each district and for each we identified an average, to then set the optimal frequency for sending out the reports. Today there is a very simple board, which notifies her when it is time to send certain reports. It’s a poka-yoke. We are running the entire administrative function of the facility using one wall!
Don’t forget, this is no private company… If lean works with people here, it will work anywhere. The public sector is possibly the most static of working environments, but here we have managed to change things.
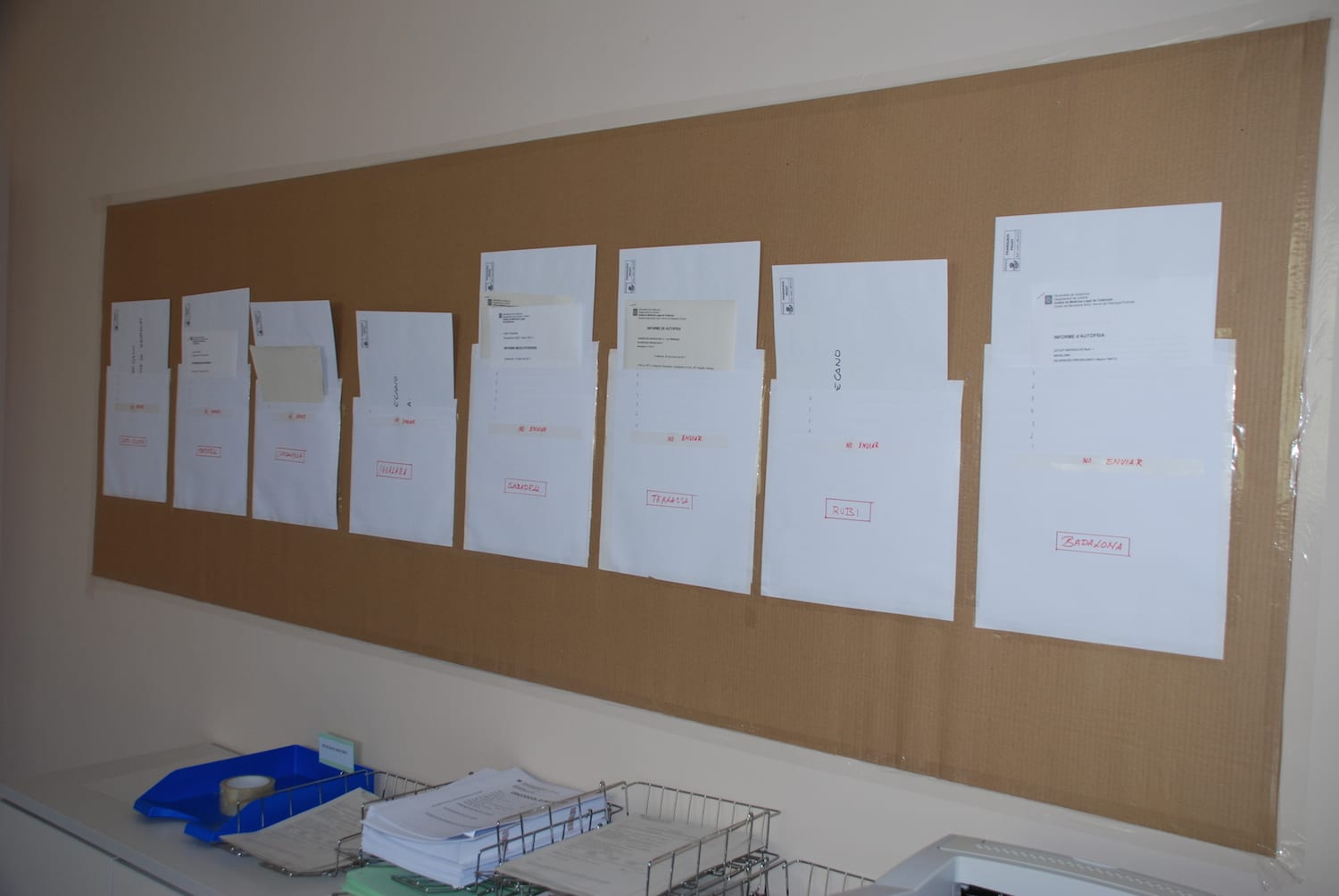
"In my mind, the most meaningful improvement we introduced was the wall that we use to run the process of managing the autopsy reports and sending them to the different courts. It brought takt time, and with it regularity, to the way we deliver them. As a doctor, I don't like administrative tasks. So, finding a new way to complete a report and ensure it is delivered with less administrative workload involved was fantastic. The process is so visual and simple now that tracking it comes natural to us: one glance is enough to understand the current situation."
Carles Martin, subdirector, IMLC
LEAN FIXATION
Whenever further testing on organs is required, medical examiners take a sample and send it to a laboratory for histological analysis. Of course the sample is sent together with an application to request specific tests.
What we had to improve was the fixation process (putting the organ in formaldehyde to preserve it), whose length depends on the body and the organ that needs to be analyzed. A brain, for example, takes three weeks to fix; a heart only one week. We struggled to get visibility over the process and to have a clear understanding of when a sample could be taken from an organ.
During the autopsy, we put each organ in a container full of formaldehyde and we fill a request form. The container travels to the laboratory with a tag identifying the autopsy and the date by which the organs will be fixed. At the laboratory, we have devised a system to effectively manage the process: it uses a table divided in two sections, one per doctor, and a calendar, indicating what samples will be fixed and by which date.
This way the technicians are forced to keep an eye on the fixation process, because there are only so many spots for containers on the table! Without this system, we’d have a cupboard full of containers, many of them carrying samples ready to be analyzed.
Another issue we had was that the organs reached the laboratory still covered in blood. We needed to find a way to clean them during the autopsy, like a strainer for example. I was using one from the beginning, out of my own initiative, and people often laughed at it. But when the budget was cut, we had to start reusing containers and people realized the only way to be able to do so would be to clean the organs during the autopsy. Suddenly, my strainer seemed like a great idea – they started to call it “the Galtes strainer,” after my name.
I’m sure that is one of those cracks I mentioned earlier, through which other lessons and improvements will come. It was something that helped people understand what lean is all about.
I think the best thing about working with lean is the incredible number of ideas we generate. Of those ideas, only a fraction is brought forward and, of those, only a couple are normally applied and then sustained. But those who are will certainly have a great impact on the organization because they came right from the people.
"Our small center is very much a laboratory that we use to try out different things, which we might then be able to apply elsewhere. While many of the problems we experience in our other locations are different, we found that we can use the same approach and tools to tackle and solve them.
In a way we need to start all over again in each facility, but at the same time it is clear that the virus in now spreading fast. It's like a colonization, which we started using the same tactic the Greeks used to infiltrate the famous city of Troy... the Trojan Horse."
Carles Martin, subdirector, IMLC
THE AUTHORS
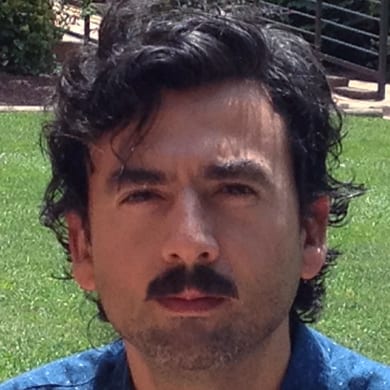
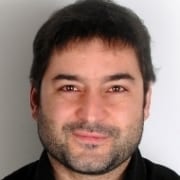
Read more
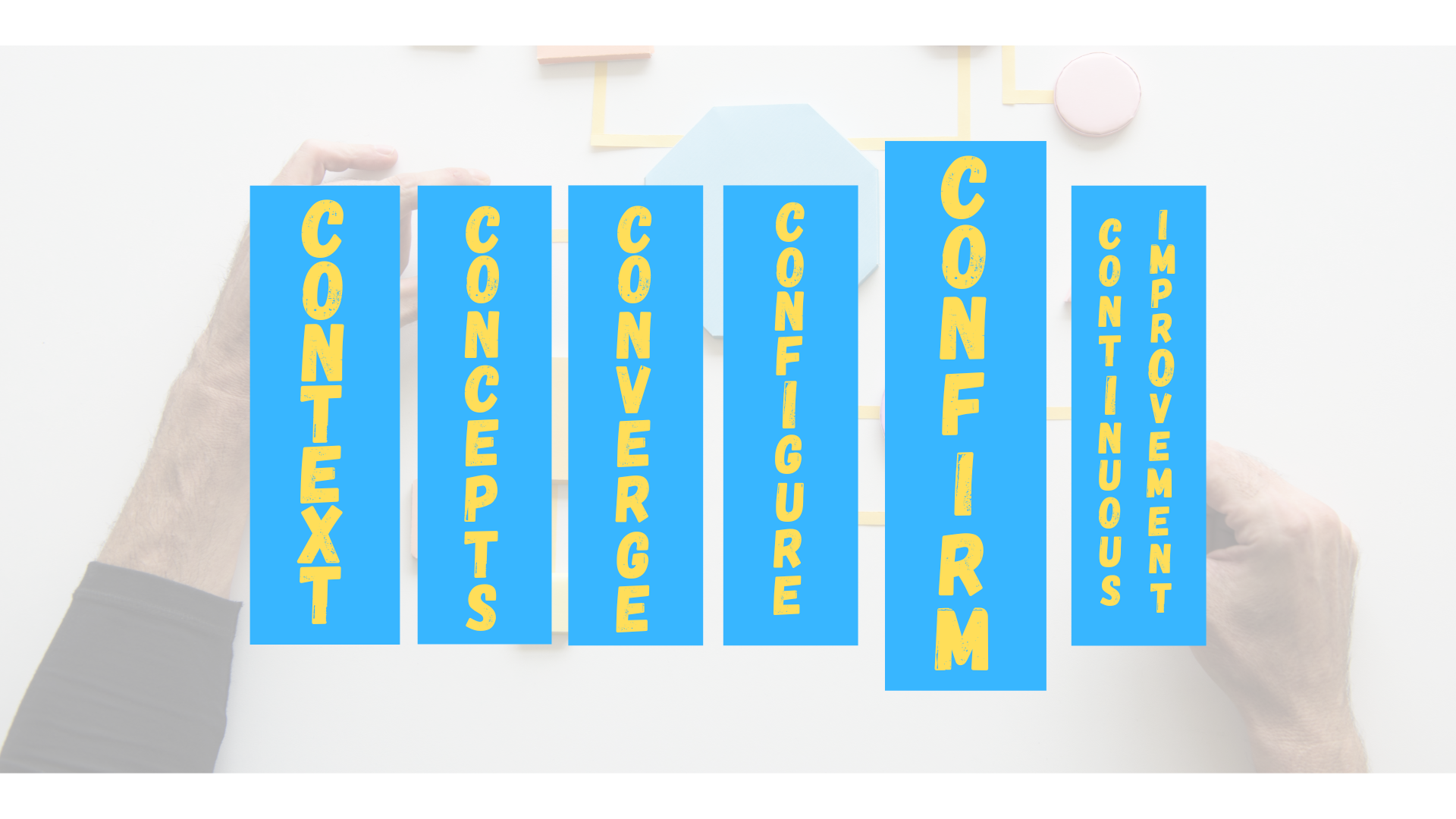
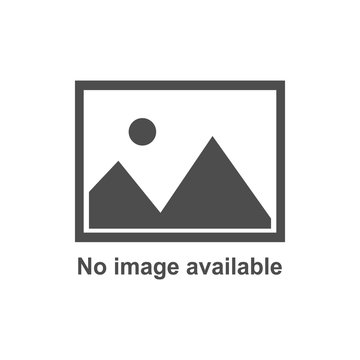
SERIES – The authors discuss the fifth of six elements in their 6CON process development model – CONfirm – leveraging a robust launch readiness approach to finalize the process while ensuring it meets the targets set in the business plan.
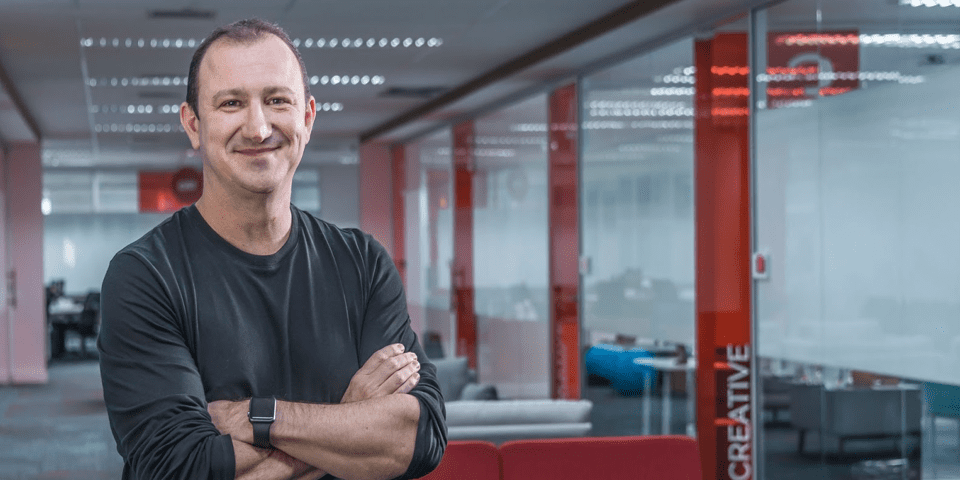
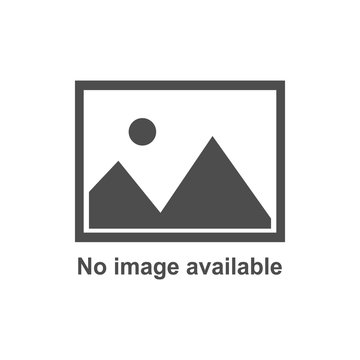
INTERVIEW – At last month’s Lean Digital Summit in Lisbon, César Gon told attendees how, with lean digital, we have an opportunity to finally get the attention of CEOs and business leaders.
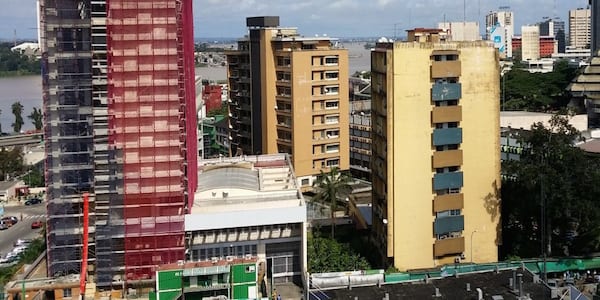
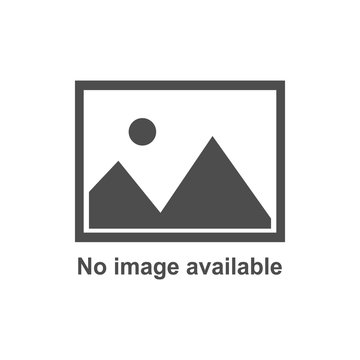
OPINION – A trip to West Africa to deliver a lean workshop prompts Anton Grütter, CEO of Lean Institute Africa, to reflect on the meaning of the Andon cord.
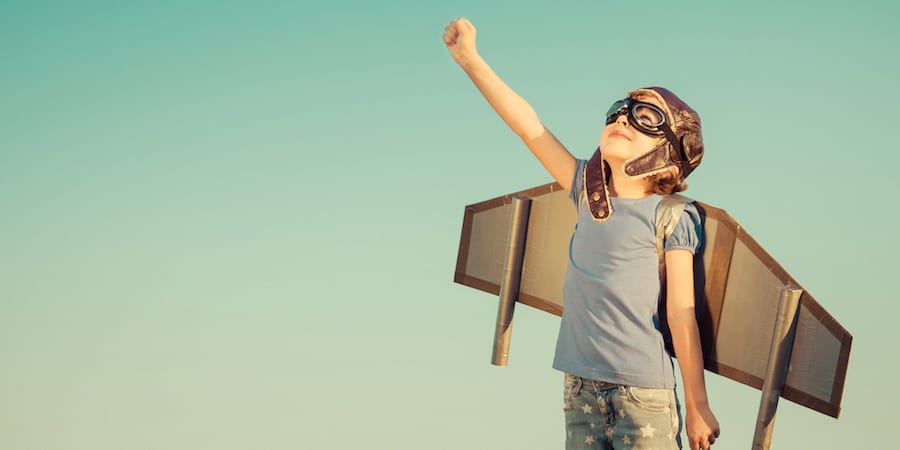
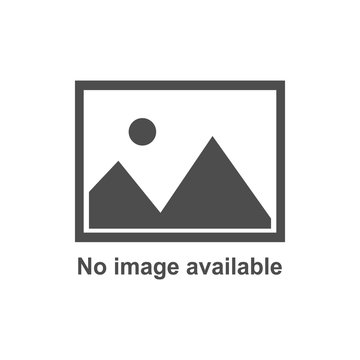
OPINION - Managers who want to hold on to their hierarchically controlled businesses and defend them against creativity and change are not protecting their organizations, but putting them at risk.