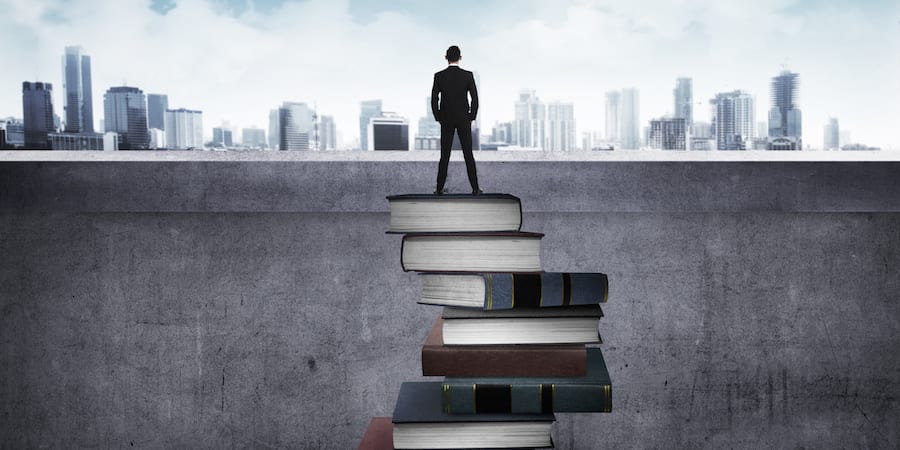
Takao Sakai on product and process development at Toyota
INTERVIEW – At the recent LPPDE event in England, Planet Lean editor Roberto Priolo sat with Takao Sakai to understand how Toyota approaches product and process development and how the Chief Engineer system works.
Interviewee: Takao Sakai, President and CEO of Global People Solutions Inc.
Roberto Priolo: Sakai-san, at the LPPDE event in England this part April you talked about an interesting concept – ningen-kei. What is it and how does it relate to LPPD?
Takao Sakai: Ningen-kei stands for “people system.” Research on it started with Frederick Winslow Taylor andHenry Ford, but over time there were many more thinkers – like Taichii Ohno – who gave their contribution to our understanding of it.
People are at the heart of any division and organization, and of any activity we carry out – among other things, they are responsible for making products (manufacturing) and for generating knowledge and information (engineering).
There is a difference, however. In manufacturing (a mass production process), ningen-kei is certainly well researched and documented, and fairly easy to manage, whereas in product development knowledge and information are intangible. We need to carry out more analysis if we want to learn to successfully manage knowledge work and understand the role of people in designing products and processes.
RP: Why do you think so many organizations find it hard to understand the importance of lean thinking applied to product development?
TS: Product development is often hard to explain and understand because it is intangible and it is all about knowledge – an abstract context. Additionally, while TPS looks interesting and fun (it involves big machines and production lines, after all), all you see in engineering is often charts and laptops.
RP: What is the right way to channel creativity for an organization that wants to innovate?
TS: Lean is the best-known way for an organization to provide value to its customers by means of a product or a process – and both require creativity in some shape or form. However, creativity has to be purposeful, which means that it must connect to the purpose coming from the company’s mission and vision.
Based on our financial targets, for example, what kind of value must we provide to our customers? What actions does each department have to carry out to contribute to the organizational goal? What price will make our product competitive? It is clear that the only thing that we can really manage and influence is cost, and there is no doubt that to make a good cost structure we need a lot of creativity in every field.
At Toyota, any technological development has to be purposeful: that is, it must either increase the value of the product or lower the cost of producing it – realizing an ideal cost structure (which Toyota calls genka-kikaku) means offering a competitive price to the target customers while ensuring enough revenue and profit for the company.
RP: Speaking of Toyota… you are an expert in Toyota Product Development. Can you explain the role of the Chief Engineer at Toyota and how creativity fit into the picture?
TS: The Chief Engineer is the “product president.” Supported by the company’s president, the CE defines the product value and price, in the face of the profit target set by the organization. The target cost set is normally hard to achieve to encourage every individual and division involved to draw from the past experience and to think creatively.
People’s knowledge and talent must be used purposefully to achieve kaizen (small and iterative process improvements) and kaikaku (revolutionary and purposeful innovation), and at Toyota both hoshin kanri and the Chief Engineer system are instrumental in channeling the necessary creativity.
THE INTERVIEWEE
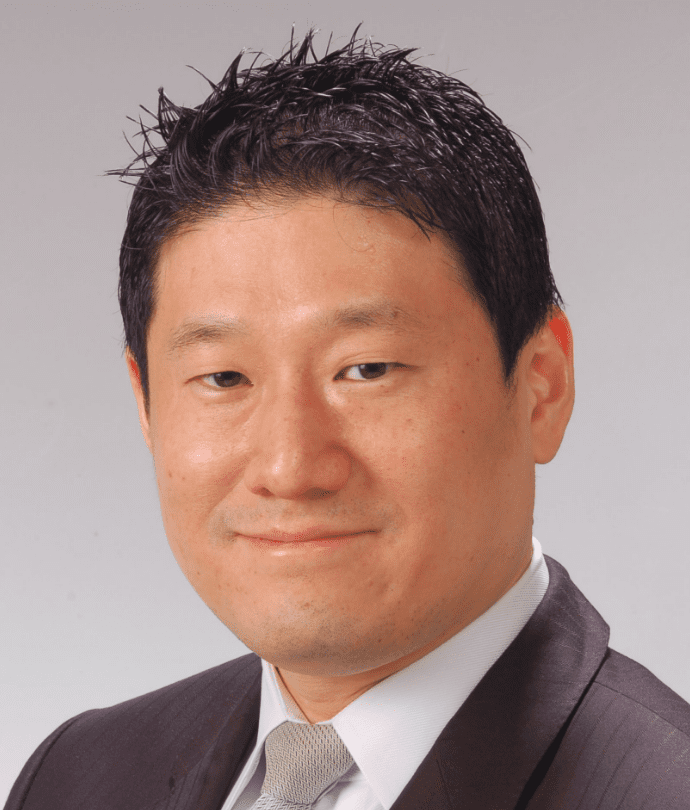
Read more
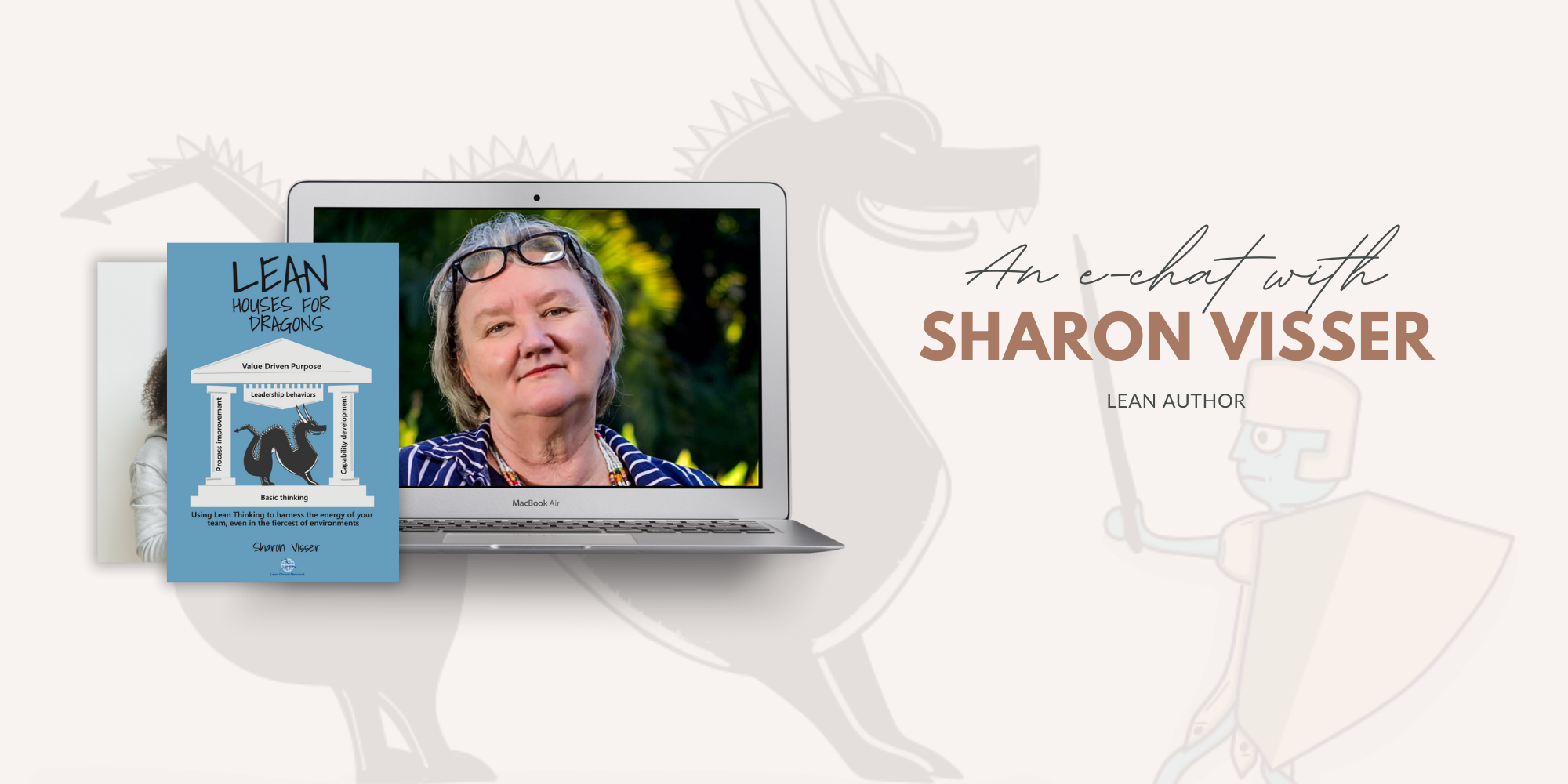
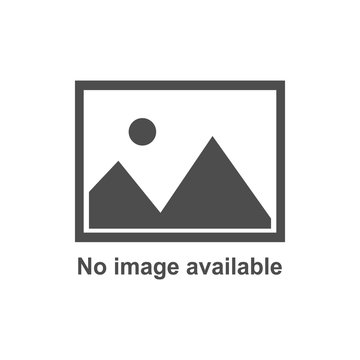
INTERVIEW – Our editor chats with Lean Houses for Dragons author Sharon Visser. They discuss her book, what fear can do to a transformation and the power of storytelling.
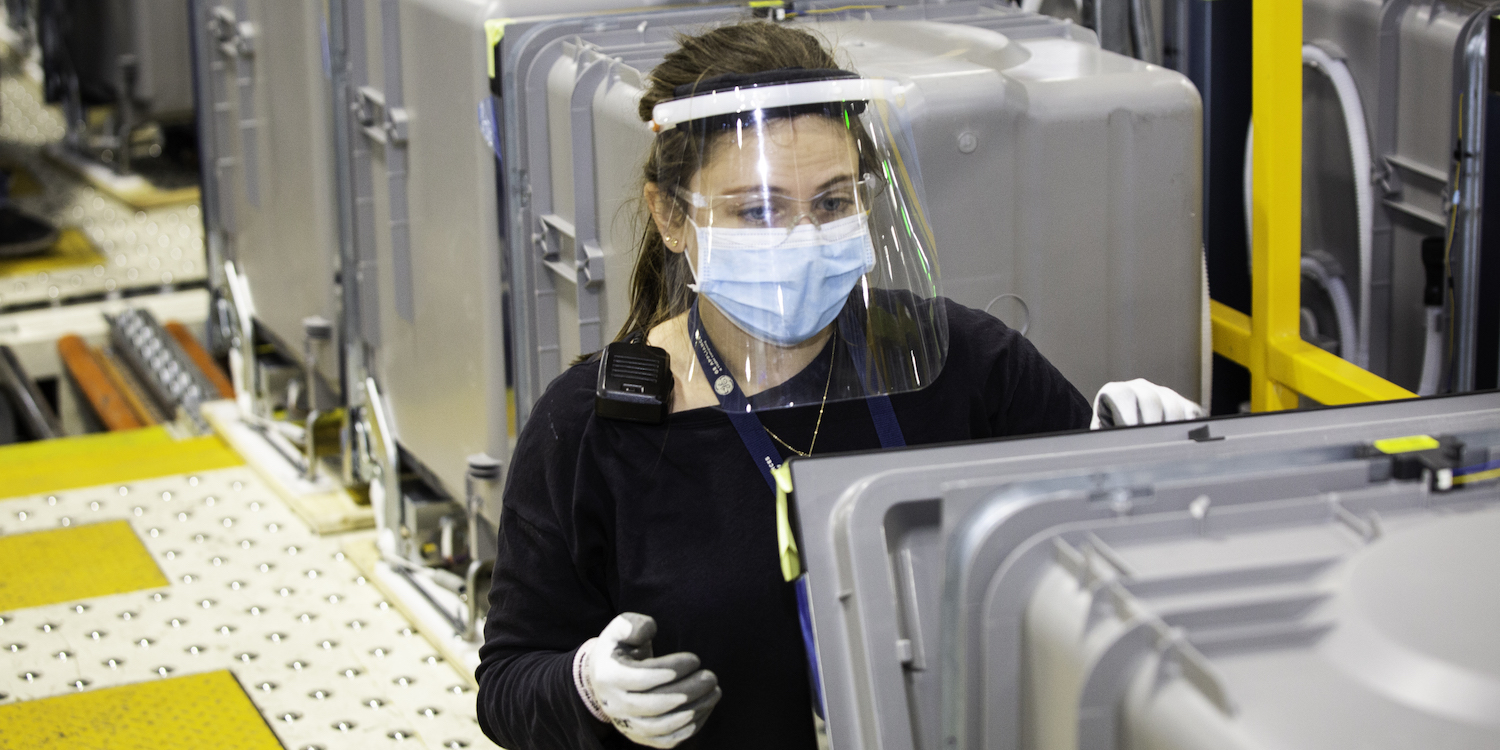
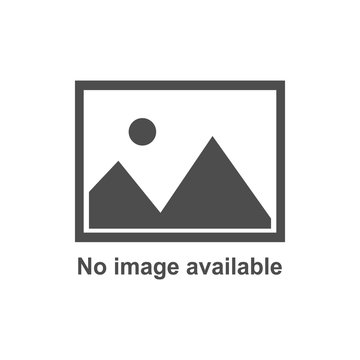
INTERVIEW – In 2020, GE Appliances had to stand up a brand-new assembly process for a new dishwasher. The leader responsible for the program explains how LPPD helped them to get it right.
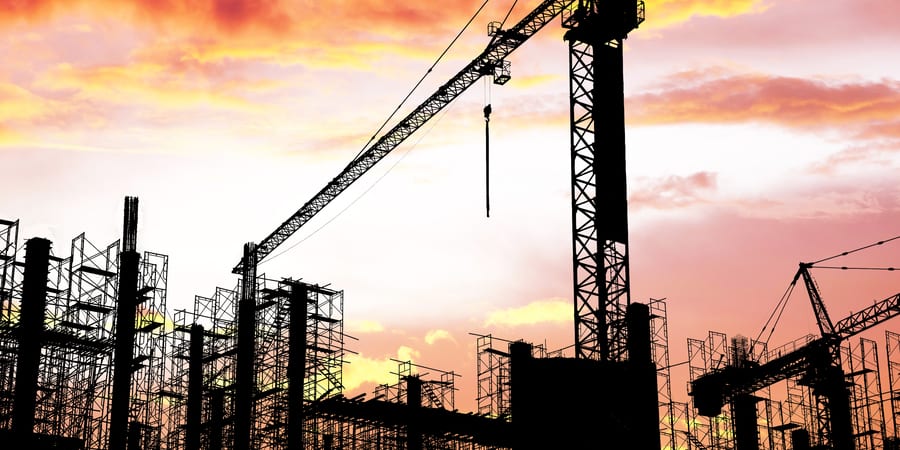
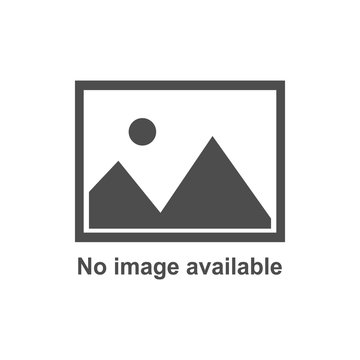
FEATURE – Drawing from his direct experience at the gemba, the author shares what he learned about applying lean thinking to his family’s construction company, and a few useful tips.
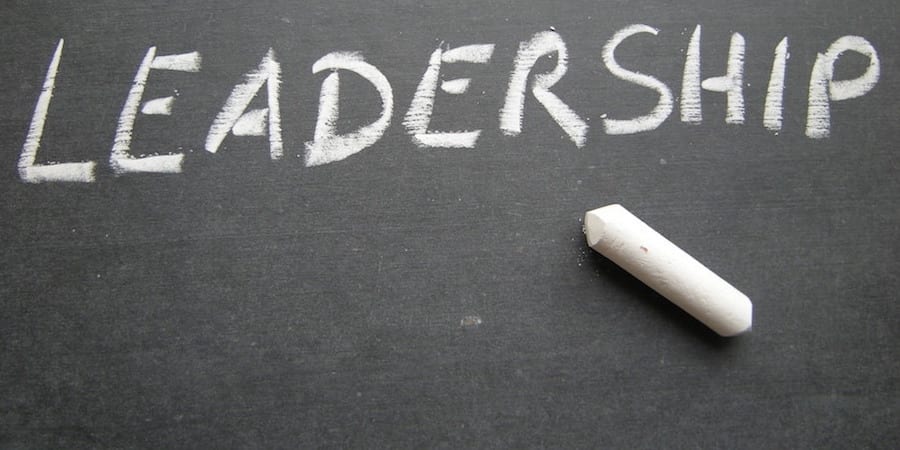
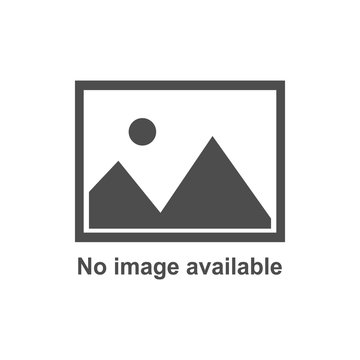
INTERVIEW – A program that aims to help disadvantaged school districts in Ohio used A3 thinking to teach principals how to scientifically solve problems together with their teachers. We met a principal and one of her teachers.