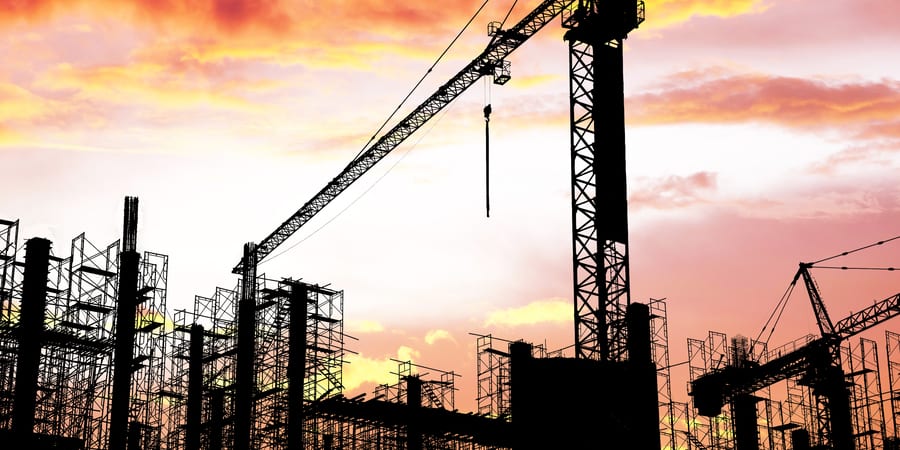
A gemba story to study lean thinking in construction
FEATURE – Drawing from his direct experience at the gemba, the author shares what he learned about applying lean thinking to his family’s construction company, and a few useful tips.
Words: John Bouthillon, CEO, PO Construction
To many, the construction industry is the go-to example of a traditional, “brick-and-mortar” environment ridden with bad working habits. Safety is often abysmal, they say, quality is considered optional and delays are the norm – not to mention the constant increase in costs. While a lot of this is true, as a lean thinker I can’t help but see a great opportunity here: what better environment to start applying lean principles than one with such a bad reputation for waste?
I have been running PO Construction, the family business my grandfather started after World War 2, for the past seven years and I have come to believe there is no roadmap in a lean journey, just a clear goal and some basic prerequisites. Or at least that’s the approach we have been using.
The goal we have set for ourselves could not be clearer: to always satisfy the customer fully, increasing value and reducing lead-time by removing waste. In doing so, we vow to learn from our mistakes, develop our people’s skills, and improve our products or create new ones. All of this should be done through continuous improvement and respecting all stakeholders. In terms of prerequisites, we have learned these are safety, tidiness and basic stability.
SAFETY FIRST
If your factory or office is being renovated and you think that this justifies your poor safety or 5S records, you will feel right at home in construction. Imagine the average construction site, and tidiness and cleanliness are hardly the first two things that come to your mind. Yet, they are the prerequisites for lean success.
It is essential to start off your lean journey by tidying up and making the gemba safe – being able to see the work and to concentrate on problems when and where they occur without being afraid for our lives and safety is critical.
At PO Construction, we found that the 5S approach had to be slightly revisited and expressed in our own words (only the first two “S’s”, while the last three are in line with the lean tradition):
- Sort and dump: we sort through our materials and equipment, and keep what we need on site, send back to depot what we don’t need now but can reuse, and throw out what is no longer usable or necessary.
- Tidy up – “One place for each thing and each thing in its place”.
- Clean up or shine.
- Standardize.
- Sustain.
Safety is a priority, and nobody can argue with that: by adopting our own version of 5S and applying it at the gemba, we have slowly started to reduce our accident ratio (by 20% year on year) – a well-known problem in the construction industry.
LEARNING TO SEE PROBLEMS; SEEING PROBLEMS TO LEARN
Our next step was listing the problems we encountered on site. In our business, it is difficult to see issues as they occur – often, a trade comes in but can’t perform their part of the job due to a problem left behind by the previous trade. As a result, it is always the painter’s fault if a project is late, simply because he is the one who has to deal with the client at the end of the process.
Faced with this problem, we realized we had to learn to see. We started to write down the problems we discovered and found a way to explain them clearly (drawing an illustration of the problem seems to work well for us). Once the problem is clear to everyone, the solution normally becomes obvious (that is the countermeasure, not the correction) – after all, construction is not rocket science.
As we see more problems, we become experts at digging up waste and come up with countermeasures. As a CEO, my contribution to this activity is critical: I regularly visit all sites and review with them how they solved their problems. I try to identify patterns and to determine in what instances they need headquarters to help. Whenever people find a smart, creative way to deal with a problem, I spread the word.
Truth is, from our problems come new ideas for improvement. They are our kaizens. Another important part of my job is to support the teams in testing new solutions, which is often difficult for us, because the task that created the problem is usually complete by the time we want to try out our new idea. So I normally try it out at another site. This can be frustrating for teams, but we have already been able to transfer our ideas from one site to another a few times.
SPEEDING UP PROJECTS
Another common problem (not only in construction) is the popular, “What can’t be done today can still be done tomorrow.” If part of a job is too difficult, the tendency is to leave it and return to it later. Hey, you never know… sometimes problems just disappear overnight, right?!
There are plenty of examples of this, but my favorite one is perhaps that a bricklayer who had completed all the walls on two floors on one of our projects, but only up to a height of five feet because he didn’t have the scaffolding to go any higher. This meant that sadly the painter couldn’t start painting anywhere, because no area was actually finished.
It is common for trades to take up much more space than they need, because they see it as a way to ensure they won’t be interrupted. If for whatever reason they can’t work in a room or on a floor, they still have plenty of other places to focus on. Unfortunately, expanding like that normally means longer lead-times.
BACK TO BASICS
When you ask how long a task will take, you usually get a quick answer: eight weeks, for example. This is how long it will take a tradesman to complete a certain job (the time usually includes a bit of a buffer, to allow for uncertainty). Ask for the pace, and you will be told eight weeks divided by the number of units (rooms, apartments, floor…), plus another little buffer that results from the math. But sometimes with lean it’s important to go back to the basic principles. The lean questions I learned to ask are: “What is your takt time?” or “If we complete this task room by room, how much time is needed between the same step of the task in two rooms?”
Imagine a project as workers walking one after the other through the rooms of a building. It is clear that reducing the time needed to complete their tasks can be achieved in two ways: getting each worker to walk faster or getting each worker to walk closer to the previous one.
Of these two approaches, the latter is the easiest. Before thinking about working faster, we should focus on wasting less time between the tasks of two trades.
ACCELERATING THE FLOW
To speed up the flow, we need to work just-in-time and produce only what is needed at every takt. The first consequence of this change is to stop working as soon as a task is completed (to eliminate over-production in the work of a trade and delays in the work of another) – needless to say, this feels extremely counterintuitive and seems to go against the balance sheet. Surely the more work I do in a day, the better! However, a project does not require more work done in a day, but finished tasks so that the next trade can step in.
Because the value stream doesn’t start and end with us, we want our subcontractors to make money on our sites too. To ensure this is the case, we completely finish tasks, apartment after apartment, and use the extra working time to prepare for the following day.
This is a huge cultural shift: these days, we know there is more value in a finished apartment than in working for the sake of working.
What I noticed is that, once this is understood, the flow automatically tends to accelerate, as each trade realizes that having more time to prepare for the next day creates better working conditions, which in turn reduces the hazards and limits the need for a buffer time. In the new system, trades can come in one after the other and work closer together than before, and problems are gradually removed.
When working apartment by apartment, the work content (the time needed by a trade to complete a task) varies with the size of each apartment. If we want a subcontractor to work on one apartment at a time, we need to come up with a way to effectively use the extra time we have when the work content is low and to avoid overtime when, conversely, the work content is high. The idea is to separate the value-adding work from the preparation work and from all the activities that come at the end (such as cleaning). Depending on the situation, we can use the extra time to prep for the following day or leave the cleaning for the following day to avoid extra costs. And here’s the trick… we don’t need heijunka, because of the natural mix of work on a construction site: the number of big and small apartments is the same on every floor and therefore the work balances automatically.
MORE LEARNING OPPORTUNITIES
To ensure that work scheduled for today is actually completed today, we have to reduce incidents and problems on the sites. It is up to management to step in and support the worker when a problem occurs. Each problem must be solved and we need to make sure they don’t re-occur.
Workers normally struggle to focus on a problem, because they have too much to do during their day, and over time they will find ways to simply work around it. They feel helpless in front of a problem, but the truth is that they know what should be done – they are the ones doing the work every day! On the other hand, management has the responsibility to encourage problem solving but doesn’t know the problem as well as the workers.
That’s why it is necessary for management and workers to join forces and work on solving problems together. In doing so, we also learn more about the way each task should be carried out and get better at scheduling the work. Sometimes, a pattern emerges from a series of problems we observe. Each worker will have seen a part of the larger situation, but can’t understand the whole picture. Management (even senior management), instead, has a big-picture view and is able to use problems to identify trends. Often “connecting the dots” shows us that what we have done so far is wrong, or counterproductive. Some of the greatest a-ha moments occur in such situations.
PRODUCT IMPROVEMENTS
Finally, in pursuing better products and processes that will reduce our carbon footprint, solving problems and performing kaizen, we generate knowledge that directly feeds into our next generation of products. If your industry is anything like construction (a project-based environment with short process life cycles), you might be able to incorporate your enhanced practices in your work within a few months.
Some changes are major; others are more incremental. At PO Construction, for example, after a difficult project using a specific type of thermal breaks for the first time, we imagined and developed our own ideal thermal break. Since then and over the years we have gradually improved both our break and the way we use it. Today, the new product is commonly used in most of the concrete buildings we build. In fact, we have even started to design our buildings based on our use of this technology, which has dramatic effects on their energy performance.
My plan is to continue to improve the work of our sites based on our strategy and to successfully spread the “new way of doing things” across PO Construction so that it becomes the cornerstone of how we design and sell new projects.
To summarize, and to draw a few lessons that others in the construction industry might find useful, here is what our approach to each new project entails:
- Work safely - Clean up the site and make safety everyone’s priority, so that you can start looking at the work and to identify the waste.
- Right first time - Learn to see defects instead of passing them on to the next trade and stop at the earliest point of deviation. You should also work to transform your company’s mindset and start to welcome problems (ask “why a problem occurred” rather than “who is to blame for it”), developing your people’s problem solving skills.
- “Finished and gone” - Value finished work more than work in progress. Increase the stability of your processes and reduce “batch sizes”.
- Accelerate the flow of trades - Value is not added unless a worker “touches” the building (painting, drilling, fixing, and so on) and empty rooms are nothing but waste in the form of waiting. You should strive to accelerate the flow by having one person work in each room.
- Lower the carbon footprint - Unleash your people’s creativity through problem solving and always think of new ideas to improve a building’s environmental performance. The construction industry is a huge contributor to global warming due its huge amount of CO2 emissions.
THE AUTHOR
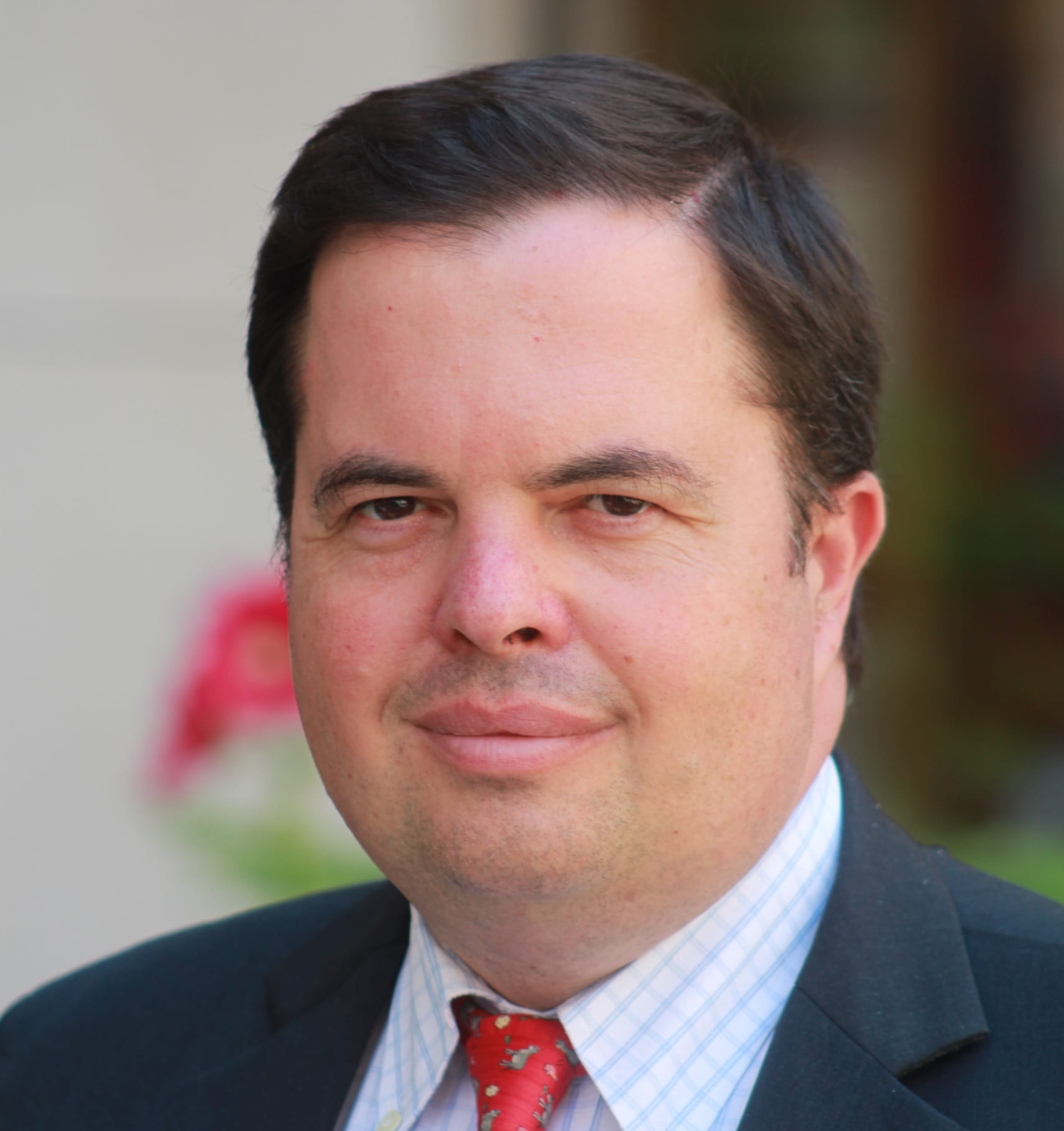
Read more
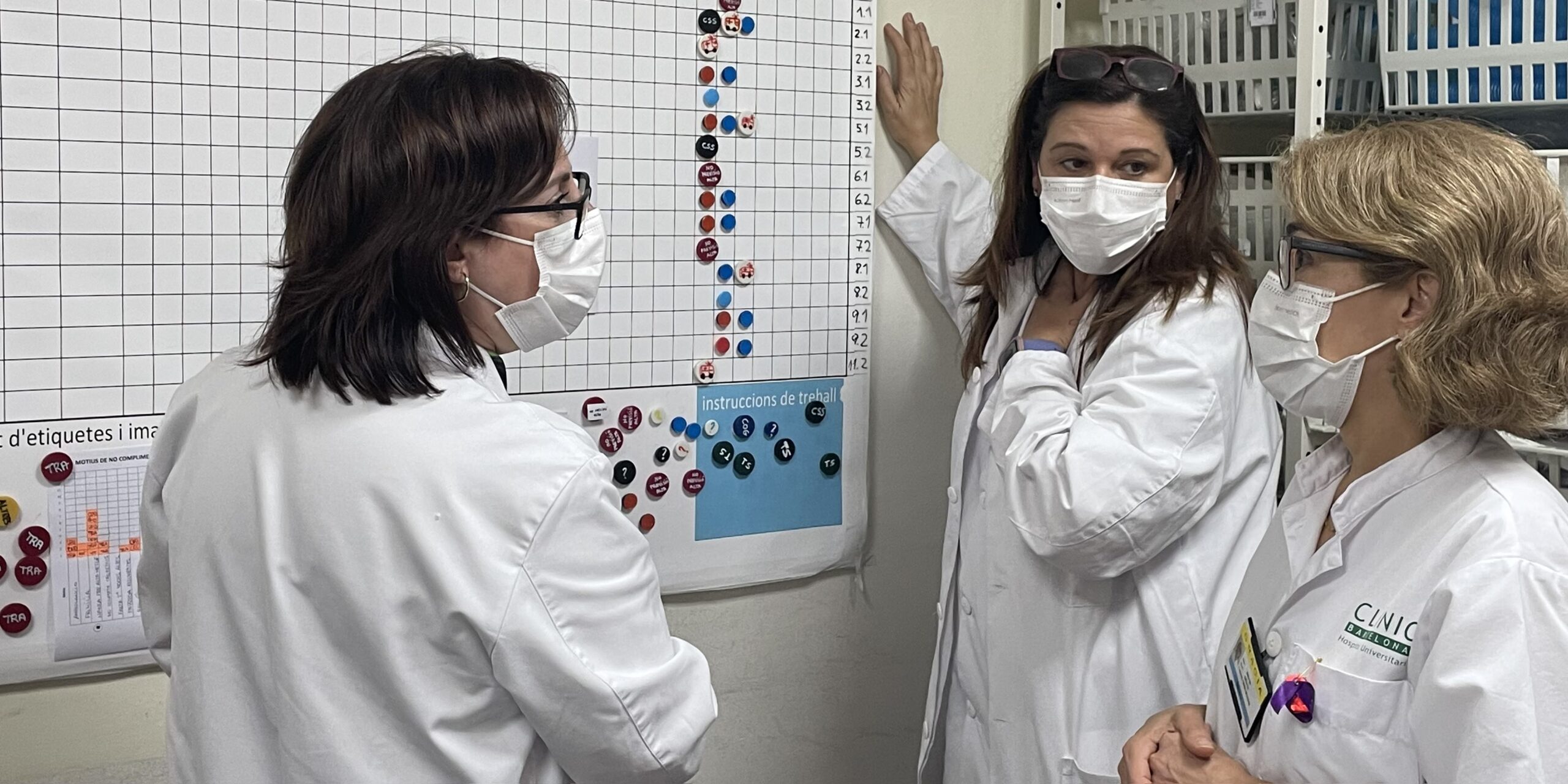
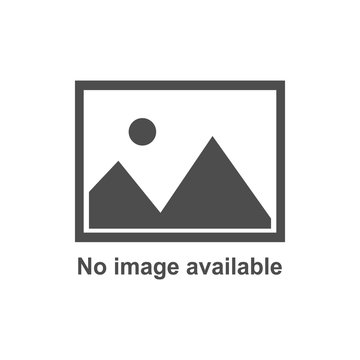
FEATURE – This nurses-led experiment in Barcelona’s Hospital Clinic is proving successful in getting more patients discharged on time and avoiding surgery cancellations.
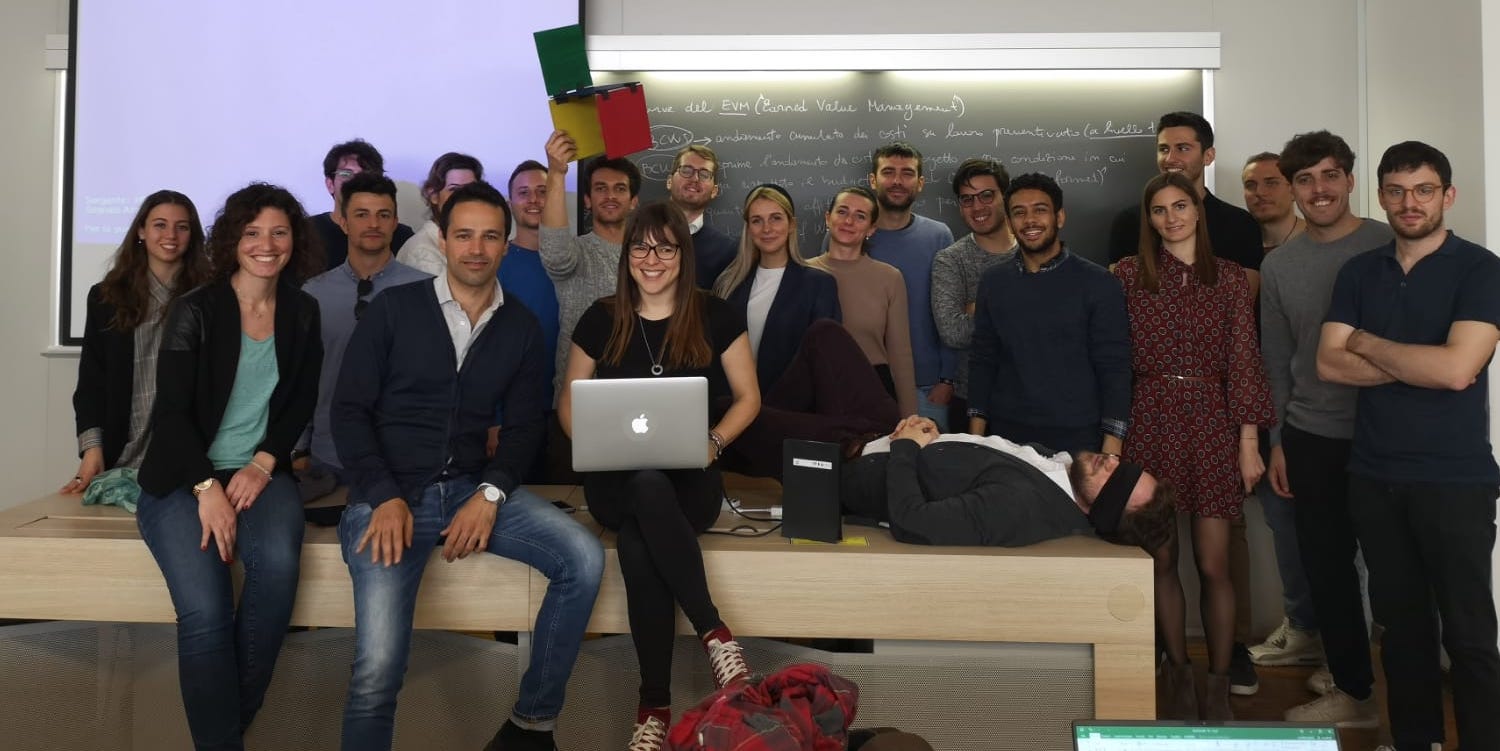
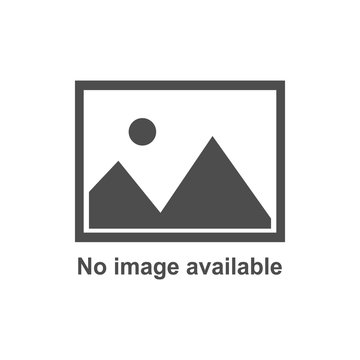
FEATURE – What does it really mean to teach lean? The author reflects on this question and shares a few tips on how to successfully engage learners in different environments.
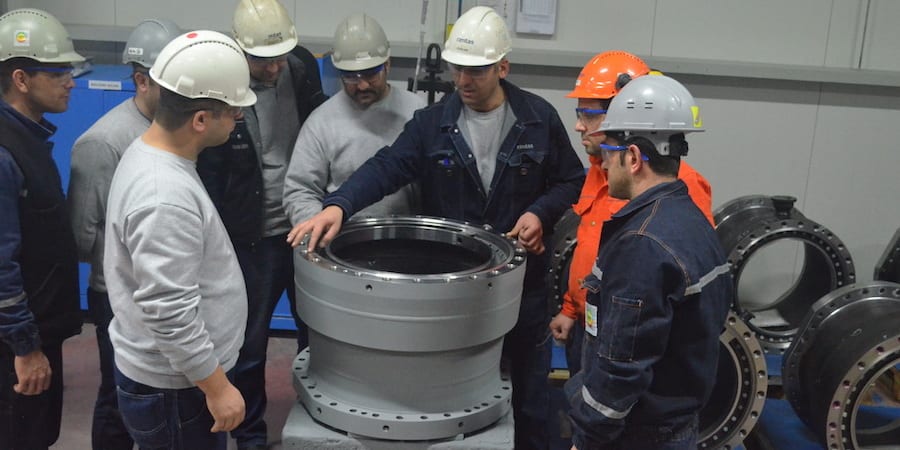
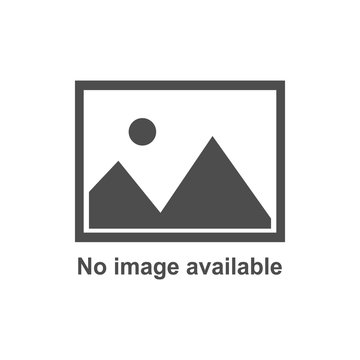
CASE STUDY – With plans to double capacity year on year in its new precision machining business, a Turkish company found in lean a way to control growth by stabilizing old processes while new ones are introduced.
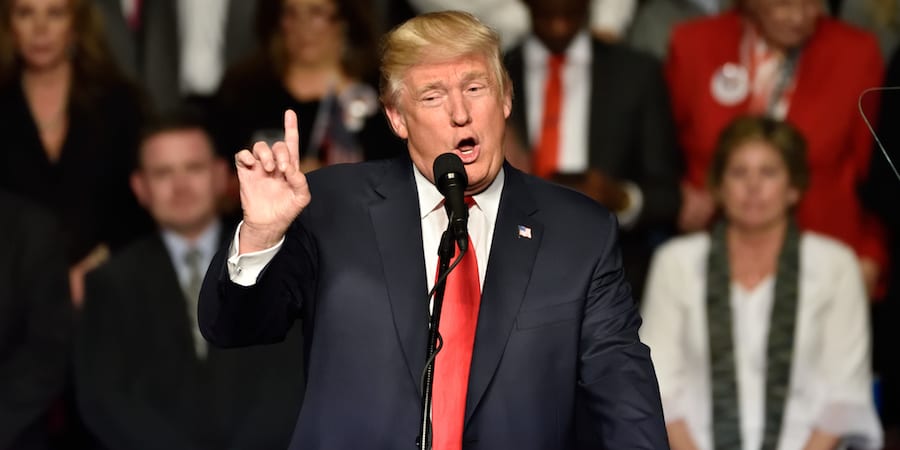
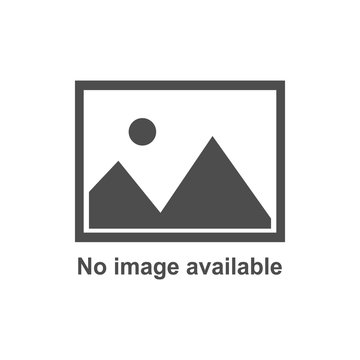
OPINION – Tomorrow, January 20, Donald J. Trump will be sworn in as 45th President of the United States. What can his campaign and dumbfounding victory teach us about leadership?