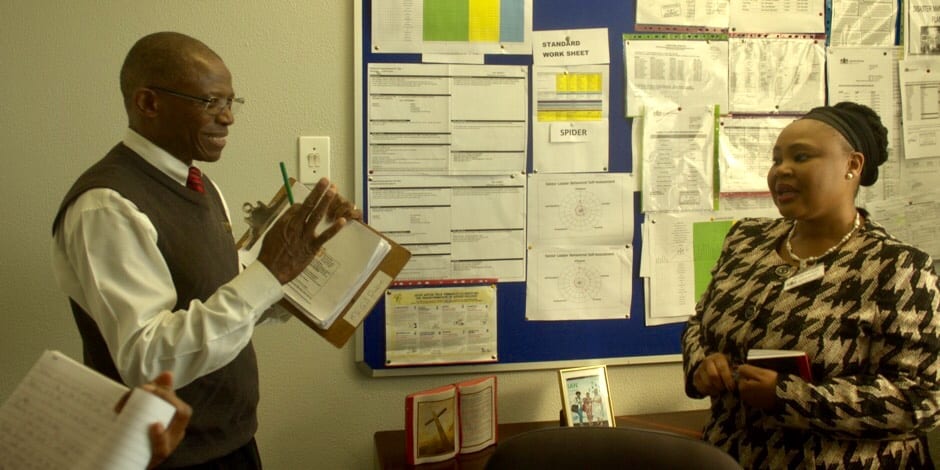
A CEO's journey of personal transformation
INTERVIEW - Grey Dube reflects on the approach, challenges and successes of becoming a lean CEO, and on how this helped turn Leratong Hospital into a lean organization.
Interviewee: Grey Dube, CEO, Leratong Hospital - South Africa
Interviewer: Rose Heathcote, CEO, Lean Institute Africa
Mr. Grey Dube is the CEO of Leratong Hospital, a Regional Hospital in Gauteng with a capacity of 855 beds and seeing on average 1.5 million patients of the Westrand and Johannesburg population (84% of them are uninsured and rely solely on public health services).
Mr. Dube began his lean learning journey in 2014. During that time, the hospital has made remarkable improvements in waiting times (up to 86% reduction, sustained at 75% in Patient Affairs), neo-natal mortality (reduced and sustained at 75%) and even finishing the work two hours earlier in one of the units, freeing up scarce capacity. They have spread their lean improvements and thinking to several areas including Surgical OPD, Medical OPD, Pharmacy, Accident and Emergency, X-Ray, with many departments now initiating changes on their own.
It is inspiring to witness the transformation of this hospital and their culture over the four years we at Lean Institute Africa have been supporting them. Leratong is now a model to other public (and private) facilities in Africa. It is clear to me that, if what they have achieved can be spread to more facilities, we will see lives change for the better.
I hope you enjoy my conversation with Mr Dube.
Rose Heathcote: How did your lean journey begin?
Grey Dube: As the appointed CEO of Leratong Hospital, I realized that I had achieved a lot as an individual but that those achievements were not sustainable. I felt something was missing, so I started searching for an answer.
In 2014, I attended my first lean training with Prof. Norman Faull from the Lean Institute Africa (LIA), and learned that lean could be what I had been seeking – that missing link that had eluded me over the years. So I got interested, and took a closer look at what lean had to offer. In 2015, LIA arrived at my institution to conduct lean experiments with my teams in Patient Affairs, MOPD and Pharmacy. This was the beginning of our lean journey, which brought many changes to the hospital, its patients and its staff.
I came to the conclusion that lean takes relentless effort, but works: my people were being developed to solve their own problems and this was transforming the way in which we served our patients.
In 2016, Prof. Faull recommended to the MEC Health that I visit Thedacare in Wisconsin to observe their improvement model. Together with other public hospital CEOs, we underwent intensive training and learned some of the secrets for creating value for the patient. This was the system that had been missing all this time and I began to develop a real love for lean.
If you had asked me a few years ago ‘What is your business improvement system?’, I wouldn’t have been able to give you a good answer. Certainly not without thinking long and hard. Now, without thinking, I can explain how we improve the work we do. We are no longer confused – we know what our mechanism for improvement is and how we use the tools and approaches to achieve our strategy.
RH: What does it mean to be a lean CEO?
GD: Before you can truly implement lean, you have to change yourself and your own behaviour. This realization really pushed me to change my own ways and employ the principles detailed in the figure below. These are the key behaviours of a lean CEO and include willingness, humility, curiosity, perseverance and self-discipline. As you can see, I rate myself in each of them as well as the re-enforcing behaviours of reflection, go see-listen-learn, asking questions, effective listening, A3 thinking, buddy system, and leader standard work. In February 2017, I rated myself low and it has taken me the whole year to improve to 4.5.
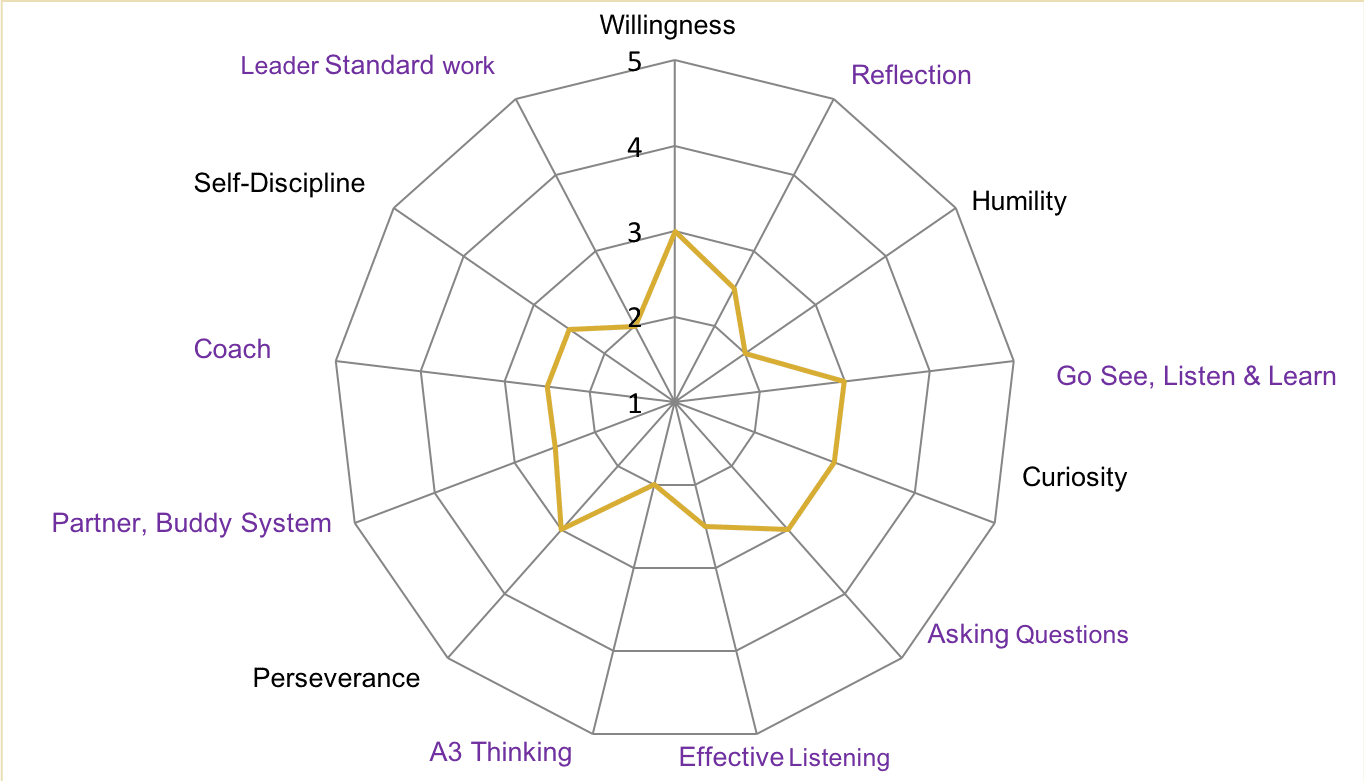
As a lean CEO, I know how important it is to offer my support, remove barriers, listen to front-line staff and hear what hardships they are experiencing in order to create value for patients. Once I initiated my own personal improvement I cascaded this to my leadership team – teaching them about the fundamental behaviors they had to develop. Now they all have their personal radar chart and focus. Critically, I became their coach and they have become the coaches for their teams. They know what is expected of them and they carry this message through to everyone else.
It is great to see leaders in our organization, like Clinical Manager Dr. Phanzu, drive change and support clinicians. He recently told me that in his mind, a lean leader is one who strives for continuous improvement, spends time on the floor, and understands the challenges for both the staff and the patients. He emphasized that if you are far from them, you lose touch. “It’s about keeping your finger on the pulse of the opportunities for improvement,” he said, adding how important it is to practice behaviors and routines that show staff we are serious about lean.
RH: What are some of the routine activities you do as CEO?
GD: Every Tuesday I visit the gemba with my executives and hear first-hand the issues being faced. I even track how much time I spend on the floor. If the challenges identified relate to finance, I refer to the Finance Manager. If the issues relate to human resources, I refer to the HR Manager. In this way, we collaborate across borders and solve problems together to support the front-line. This helps us improve the system.
We have developed our True North, which represents the strategic imperatives we commit to and the key things we focus on in the hospital. This is then translated into a balanced scorecard and status sheets at the gemba. A3 projects are also initiated to support these goals. In this way, we are connecting strategy with the activities on the ground.
A lean CEO has to be able to take a hard look at himself or herself, and strive for personal improvement. On a daily basis, I reflect on what I have done well, what didn’t go well and what I can do to improve the situation. Every day, I strive to move forward, one step at a time.
I’ve also developed my own personal leader standard work, and this guides me on the daily, weekly, monthly, quarterly and annual activities I need to accomplish. I support myself by sticking to this routine and my staff notice and appreciate the consistency. My managers do the same.
RH: What is the impact on your people?
GD: My people are happier. They are empowered and equipped to solve their own problems and they feel supported. They are the ones who understand the work, its challenges and are best placed to provide the solutions.
Managers no longer visit their areas to harass people and act as traditional, controlling leaders – they now show up with a better attitude based on respect and humility and they are consistent in this approach. We have to move away from a management style of control to one of support, which has a real impact on staff.
All the departments involved in the lean transformation have started their status sheets and gemba walks. The engagement and interest in lean has spread like wildfire to other areas where we’ve not even gotten to. They are spontaneously asking me when we are coming to help them. It's like a pull system for learning.
People now see problems, develop solutions and celebrate the results they achieve. They discuss on a daily basis what happened the day before, and what they can do to improve the situation. It’s a learning curve and it is clear that the more they learn, the more they become examples and teachers to others.
RH: Have the patients noticed an improvement?
GD: We used to get many patient complaints. In fact, at times it felt like that's all we got. Since we have taken on lean thinking, however, we have seen a measurable reduction in complaints and we have even started to receive compliments.
In MOPD alone we received 16 compliments after we slashed waiting times. We still receive complaints, but far less than we used to. We have come to welcome the feedback, as it helps us stay close to the issues that matter to our patients.
RH: What do you find most challenging about becoming a lean public hospital?
GD: It is difficult to change our old habits. As a lean CEO, you have to work very hard to help people see that lean is a strategy that can work. You have to be consistent in your message and your own behaviours before people can start to believe this is here to stay.
In the public health environment, you have limited resources and you have to think outside the box and make do with what you have. In this way, lean helps us develop our thinking to achieve better and more innovative ways of serving patients.
Clinicians are tough to convince. They began to support the lean transformation after seeing the first results, but in the beginning they were resistant. We only succeeded in getting them on board because we were consistent in addressing their concerns and stuck to our approach. To convince the leadership at Department level was also a challenge, and it is fantastic to see Gauteng Health now sees the value and bought into the concept. We hope to see lean spread to every facility and clinic, touching every person until we have a community of problem solvers who address problems scientifically day after day. As I see it, this is one of the best ways to transform healthcare and help society in Africa.
RH: What is the benefit to the CEO?
GD: lean allows you to move from crisis management to proactive management. I have less crises coming into my office these days, because problems are tackled at the right level of the organization. Foreseeing issues and addressing them in a timely manner prevents them from turning into large, severe and hard-to-manage problems.
RH: Will lean at Leratong survive beyond you? What happens when you retire?
GD: Lean is now built into our strategy, systems and culture, and our people have recognized its value. When I’m not here, the work continues. The fact that this system has now been adopted in other Guateng Health facilities means it will also be driven from provincial leadership. The next step it to expose the Ministry and Premier to lean and all it can offer, so that we can change more and more lives.
THE INTERVIEWEE
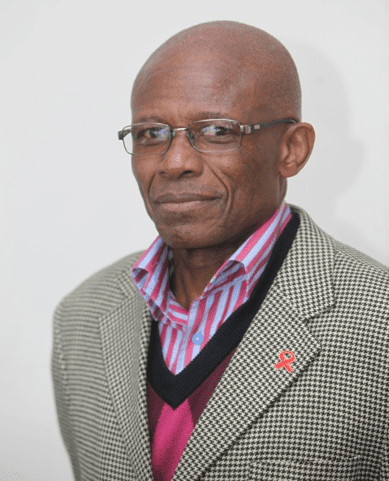
Read more
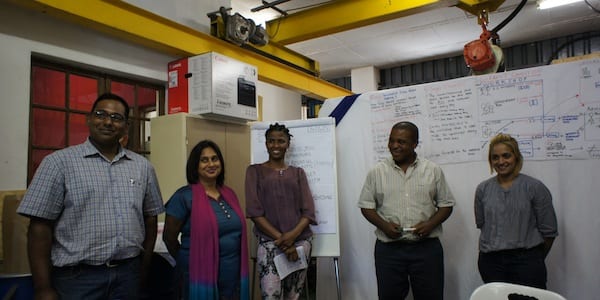
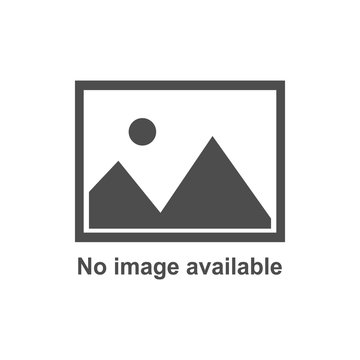
FEATURE - Norman Faull, Director of Lean Institute Africa, talks about a supplier development project the institute took part in, and shares a few of the results achieved.
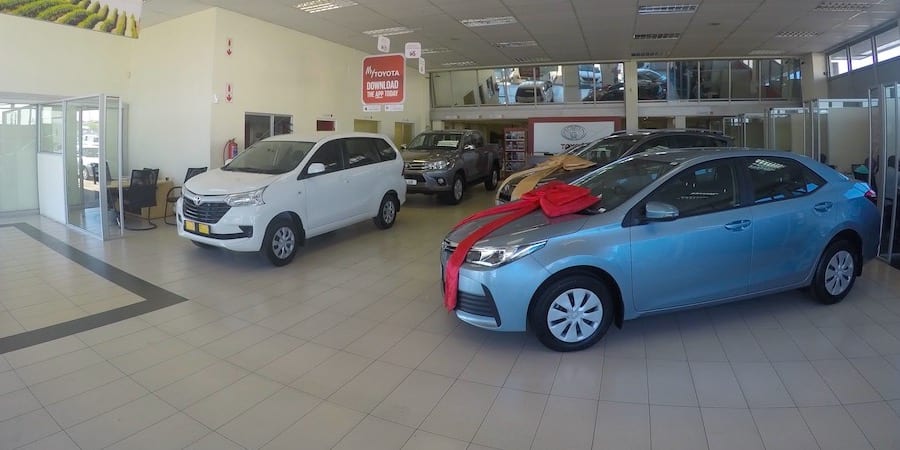
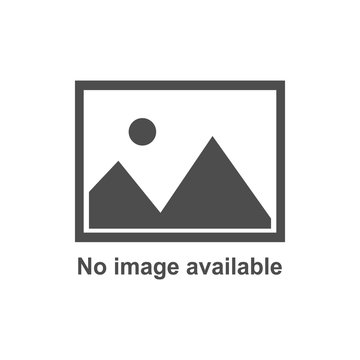
VIDEO - Visualization has an important role to play in creating awareness of the problems and highlighting gaps as a key starting point for improvement, and this Finance Manager does it with dedication.
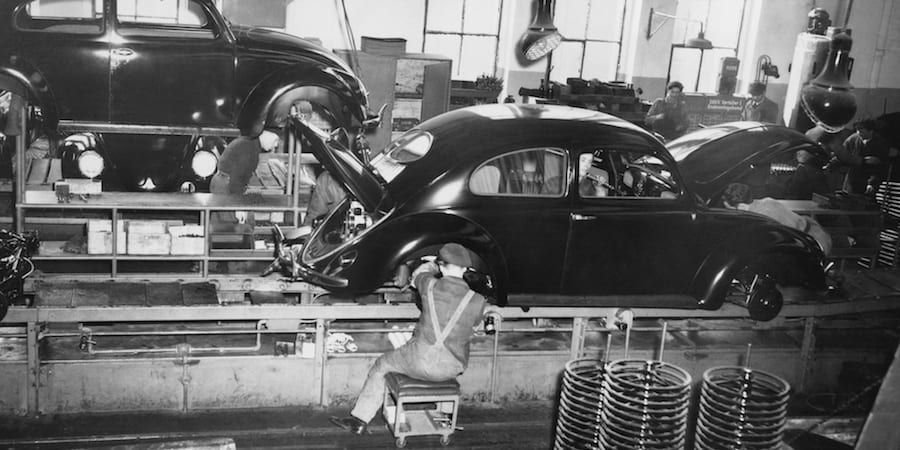
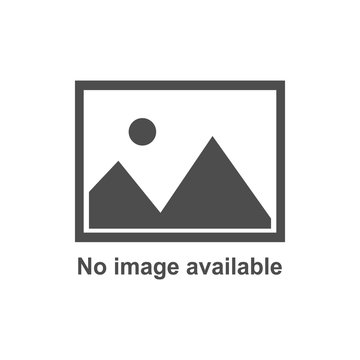
WOMACK'S YOKOTEN – The author reflects on how the legacy of Taylor and Ford still poses challenges to the lean movement, and why critics should move past a simplistic view of lean as mere standardization.
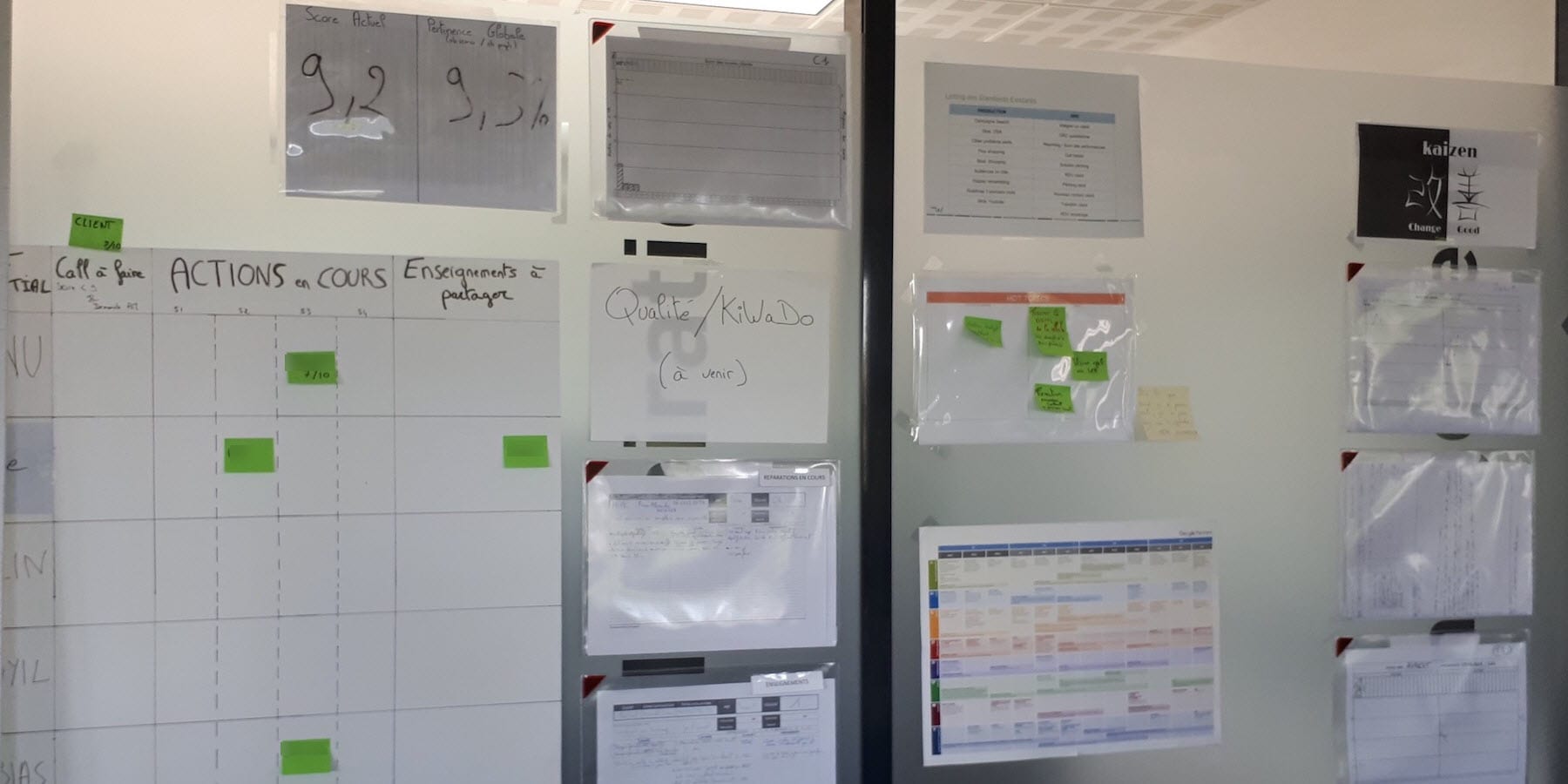
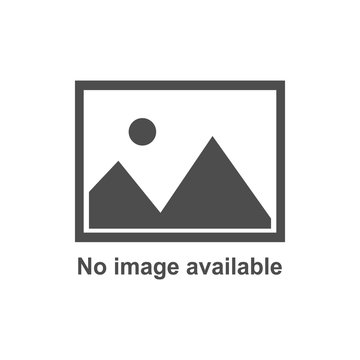
NOTES FROM THE GEMBA – In the web marketing world, a competitive advantage is a matter of life and death for businesses. The author meets a firm that has been leveraging lean to gain one.