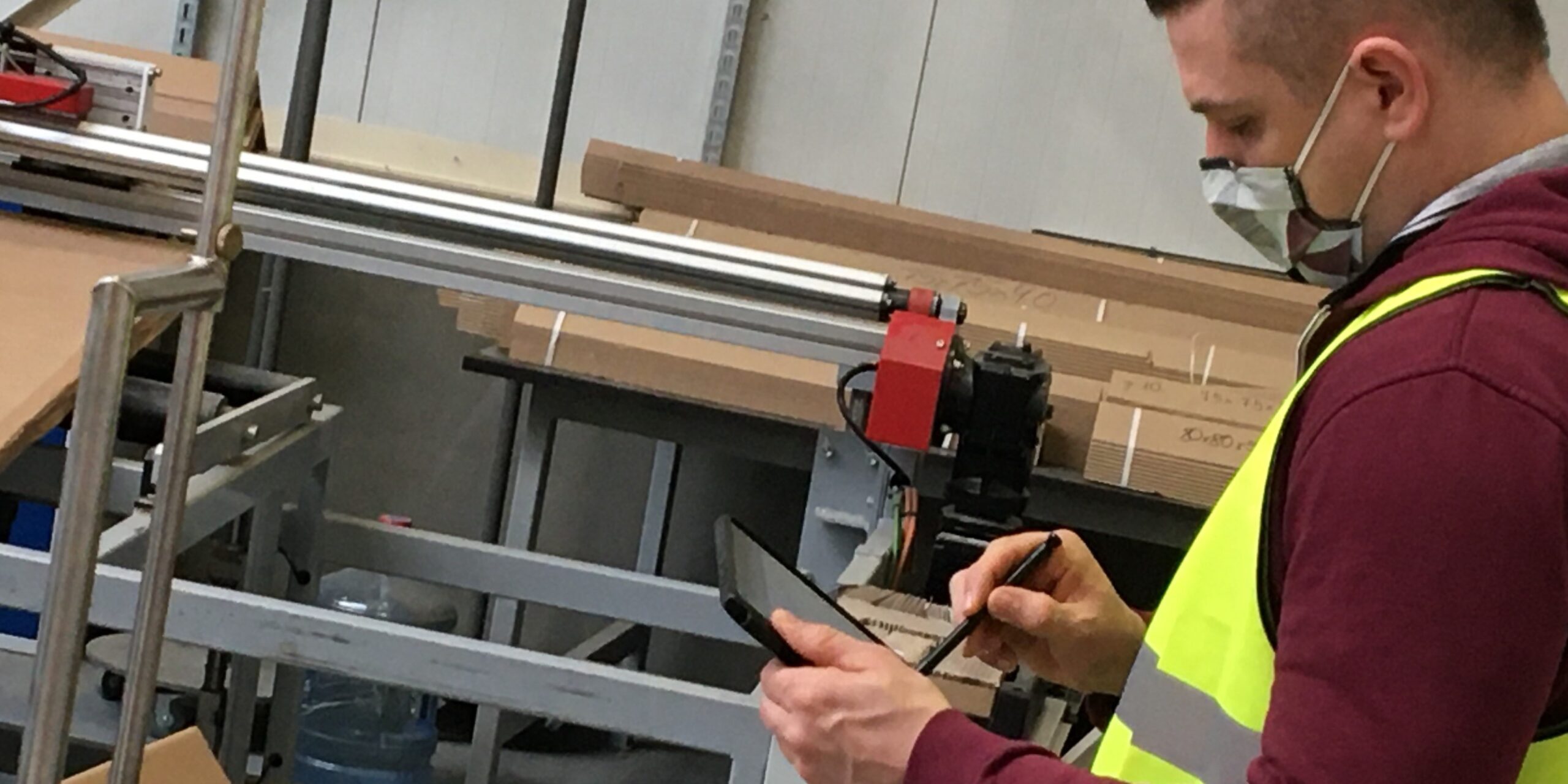
When digitalization reaches the gemba
FEATURE – During a recent Jishuken workshop, Poland-based Schumacher Packaging experimented with a newly-developed App to quickly create standardized work instructions at the gemba.
Words: Remik Horbal, Head of the R&D, Lean Enterprise Institute Poland
Many believe that digitalization and gemba do not go hand in hand. After all, going to gemba is all about getting up close and personal with the process and observe it. Surely, a piece of paper and a pencil are enough to identify waste and come up with improvement ideas. While that’s true, we unfortunately can’t deny that there is more to improving processes than unleashing our creativity. As anyone who has had to create Standardized Work Instructions (SWIs) will know, it also requires laborious paperwork.
Writing out steps and key points in the process on a notepad, after consulting with operators and adjusting them, is one thing, but the tedious creation and edition of instructions using Excel or Word is something else entirely. This paperwork can take many hours to complete. That's why the R&D department of Lean Enterprise Institute Poland, in cooperation with its industrial partners, decided to develop an App to create SWIs on a smartphone or tablet directly on the shop floor. The App allows you to take photos that illustrate the work and automatically generates instructions within a given template, thus saving team leaders hours in front of a computer screen.
In March this year, Schumacher Packaging used this App – called Soft4Lean SWI – during a Jishuken workshop. This type of activity can be quite challenging: leaders learn to improve processes directly at the gemba with the help a coach and, after three days of workshops, the production cell is already working in a new, more efficient way. Everything happens very quickly during a Jishuken activity, which is Schumacher Packaging used the App we developed to quickly generate the first versions of the new standard work. When the mock-up of the new cell was being built, participants were already able to create the first draft of the new Standardized Work Instructions and share them with operators. When the new, improved version of the cell was launched, they used the observations and feedback they got from the operators to further improve the standard right there on the spot, by modifying SWIs on their tablets using the Soft4Lean SWI App.
According to Maurycy Szkolnicki, the LEI Polska coach who led the workshop, using the App helped the team to “spin the PDCA wheels faster” because changes can be made in real time after testing each iteration of an improvement.
Tomasz Zamczała, Lean Manager at Schumacher Packaging, added: “What's important to us is that we can create the standard right away in an electronic format and add photos as we go. This way, we don't have to transcribe this information into a computer afterwards. Also, standards can be corrected very quickly, and this is important in the process of continuous improvement. Critically, we can add our own instruction templates to the App, to suit our specific needs.”
At the end of the first day of the workshop, the participants decided to change the standardized work instruction template. Our support team had to create a new template overnight so that the participants would have it available on the following morning to begin their work on the first version of the new standardized work. Fortunately, creating new templates on the App is quite simple: all it requires is to upload the appropriate file in the commonly used XML format.
According to Tomasz Zamczała, another important advantage of using Soft4Lean SWI is that the complete standards are stored in a centralized database that is easily accessible electronically by anyone across the company. At the same time, we have made sure the App would work offline as well, because we know that the Internet connection on shop floors is often not that great.
Although many users of the App prefer to create instructions directly on the shop floor on their mobile devices, Soft4Lean SWI is also available in a PC version that is particularly useful when it comes to fine-tuning instructions (for instance, to fill in instruction headers, to manage the instructions database or to export the instructions as Excel or PDF files).
Our team is constantly focused on enhancing and developing the App together with users. We want it to be as convenient to use as paper and pencil, but also to provide the full range of possibility afforded by mobile devices. After all, on such devices we can dictate the content of the instructions, take photos, record videos, track times. We believe that digitalization provides great opportunities, so long as it is easily accessible at the gemba.
More about Soft4Lean SWI applications can be found at www.soft4lean.com. All comments and feedback are welcome. Contact: remigiusz.horbal@lean.org.pl
THE AUTHOR
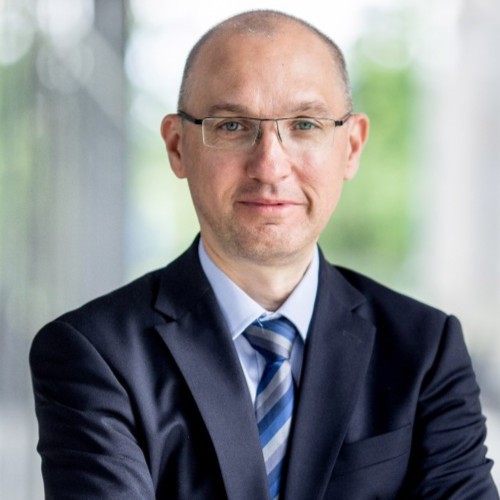
Read more

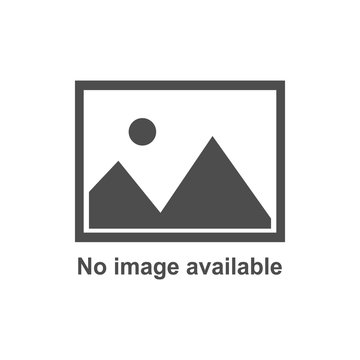
FEATURE – In business, the word “turnaround” refers to radical changes in the direction a company is moving toward. Here’s why Lean Thinking can increase the chances of success of such endeavors.
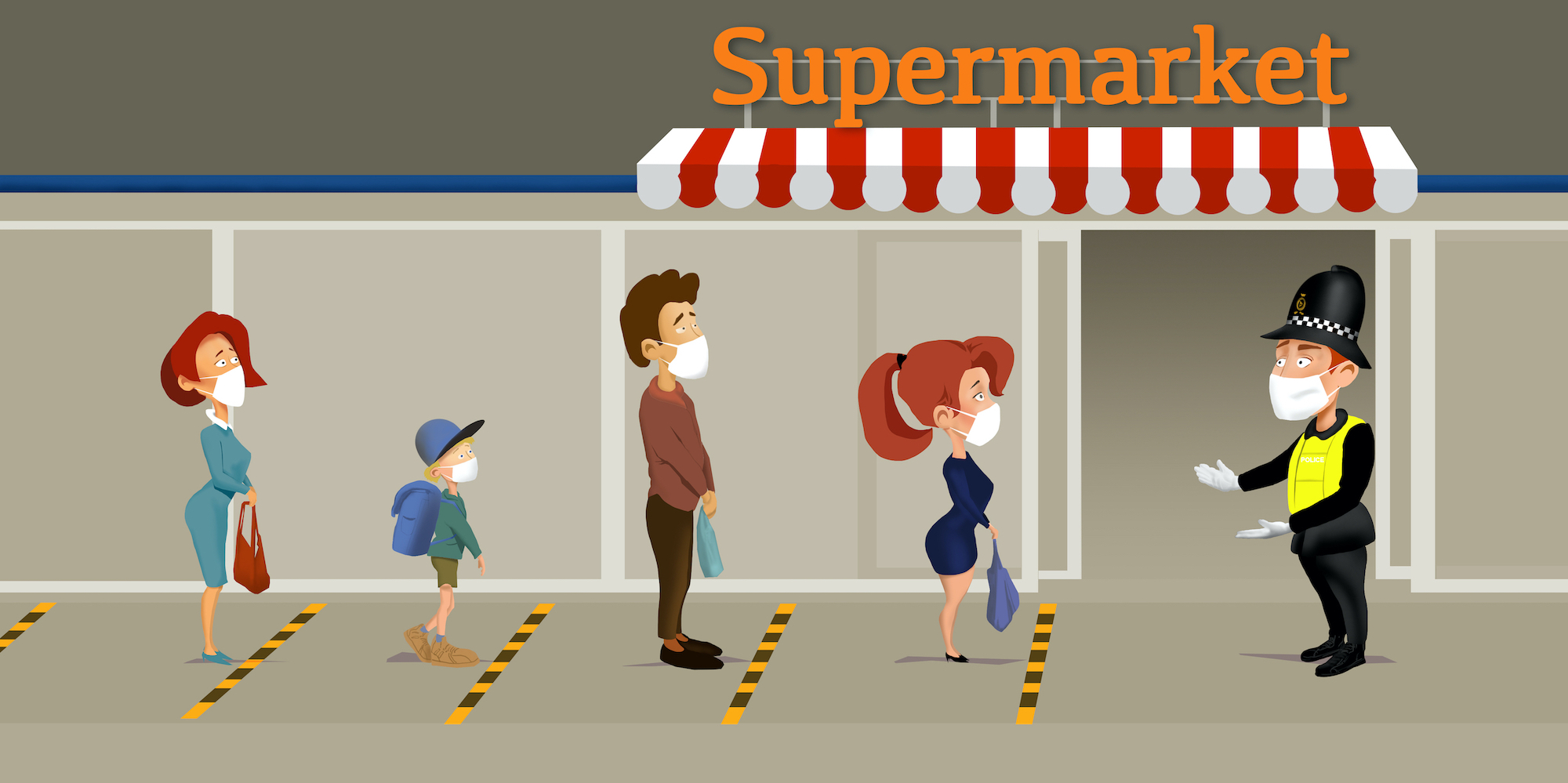
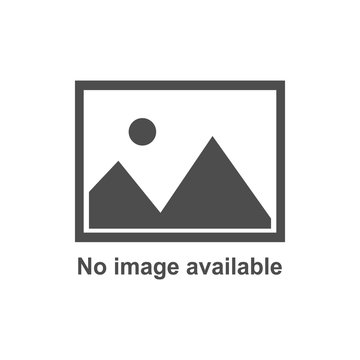
FEATURE – A simple lean tool can help us create safer flows in our businesses, a critical challenge as we plan our return to work with new physical distancing measures in place.
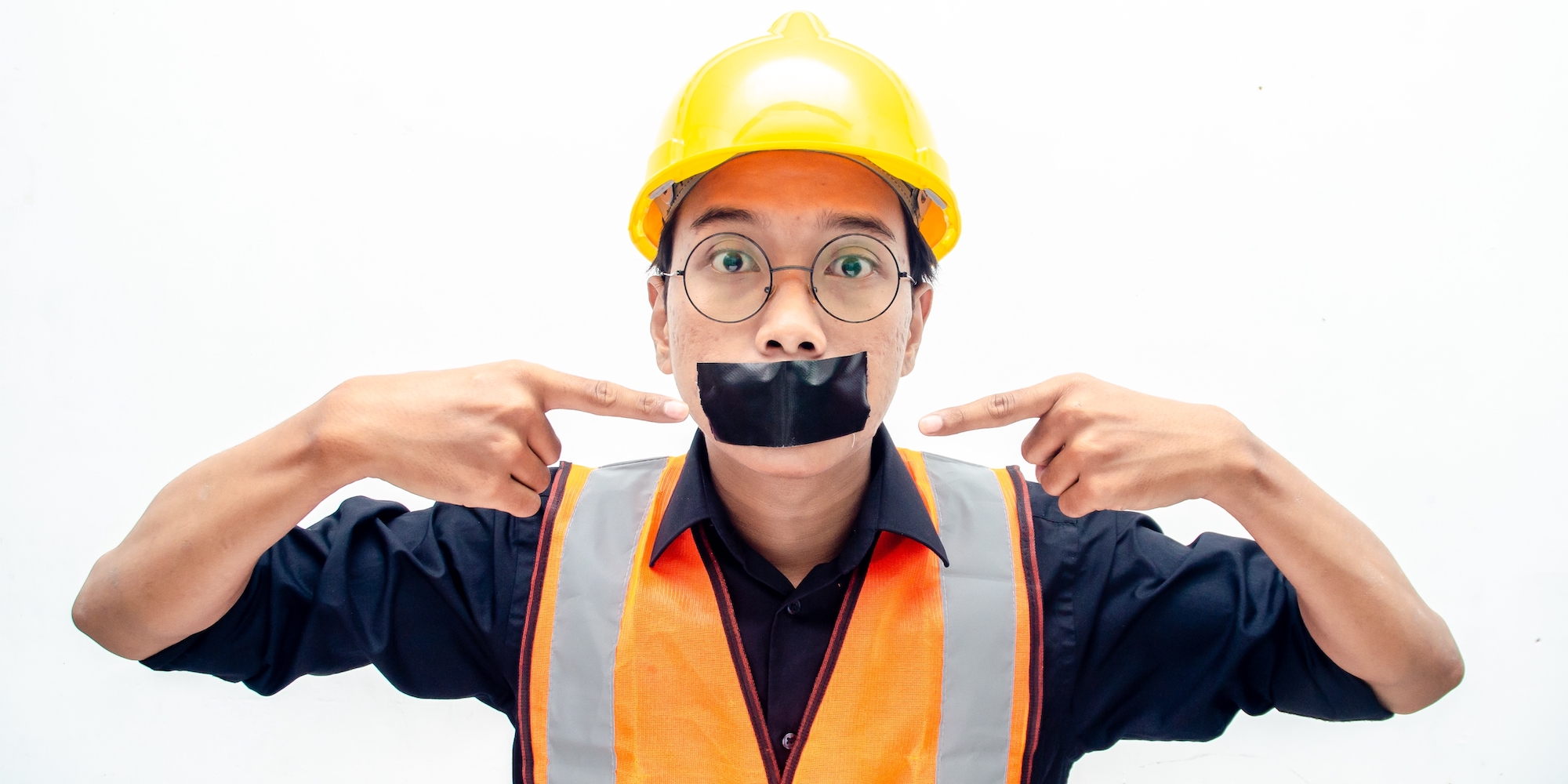
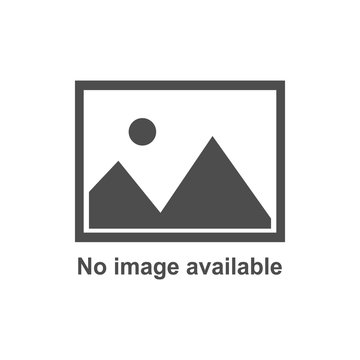
FEATURE – By changing its attitude towards problems and welcoming them as opportunities to learn, this Colombian construction company has turned around its culture.
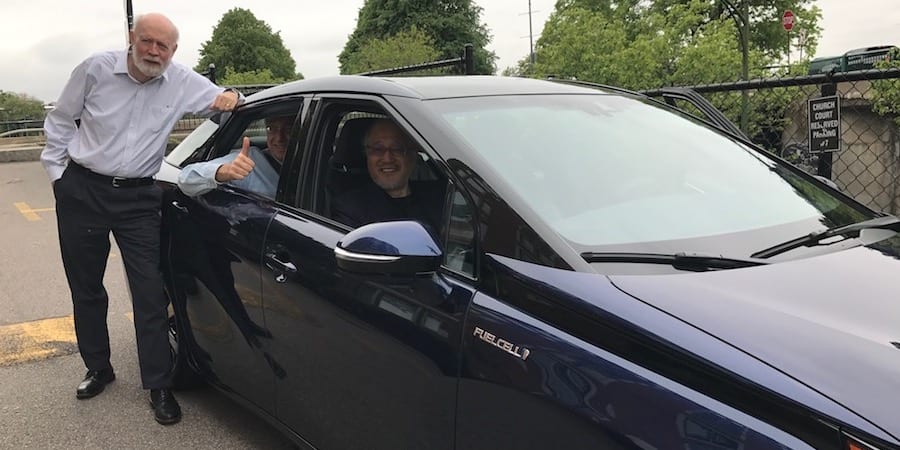
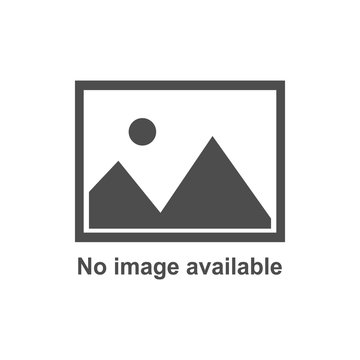
WOMACK’S YOKOTEN – After a road trip from Boston to Philadelphia driving Toyota’s hydrogen fuel-cell Mirai, Jim reflects on lean and green and why the two are not necessarily the same.