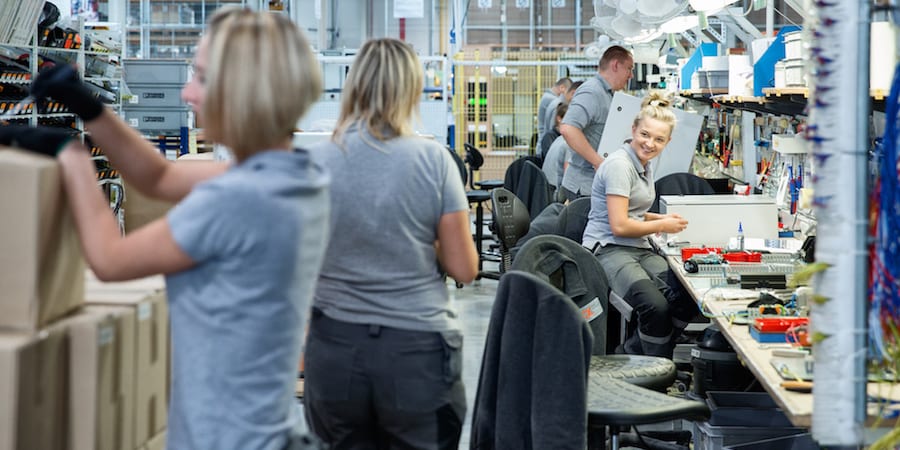
KK Wind Solutions in Poland uses TWI to improve onboarding
FEATURE – When you are hiring 20-30 people in a week, getting them up to speed with the company’s way of working becomes critical. But how to do it effectively? A Polish factory found the answer in TWI.
Words: Dagmara Chmielewska-Bien, HR Specialist, and Radoslaw Mackowiak, Line Manager, KK Wind Solutions Poland, with Michal Ziemann, Lean coach, LEI Polska
KK Wind Solutions’ factory in Szczecin, Poland, makes electrical systems for wind turbines and employs around 650 people. In recent years, demand for the company’s products has grown exponentially, leading the factory to continuously hire new people – at one point this year, we were welcoming 20-30 new employees in a week. You can imagine how badly we needed a system to quickly bring them up to speed!
Even though the company has been on a lean journey for quite some time, we didn’t have a standard for the onboarding of new employees, which meant that new hires joined the team directly on the lines and, not knowing exactly how the system worked, lagged behind everybody else’s takt time, causing delays for the entire production department. Team leaders on the line were responsible for training new people, but this was clearly not enough.
This is the main reason why in October last year we decided to start experimenting with Training Within Industry (TWI) with the help of Lean Enterprise Institute Polska.
EXPERIMENTING WITH TWI
The first thing we had to do was identifying the basic knowledge that newly hired people needed in order to start working on our lines. Because we manufacture electronics (large cabinets with electrical systems inside) for wind turbines, the essential operations that every KK Wind operator must be familiar with include wiring, insulating, and assembling copper components.
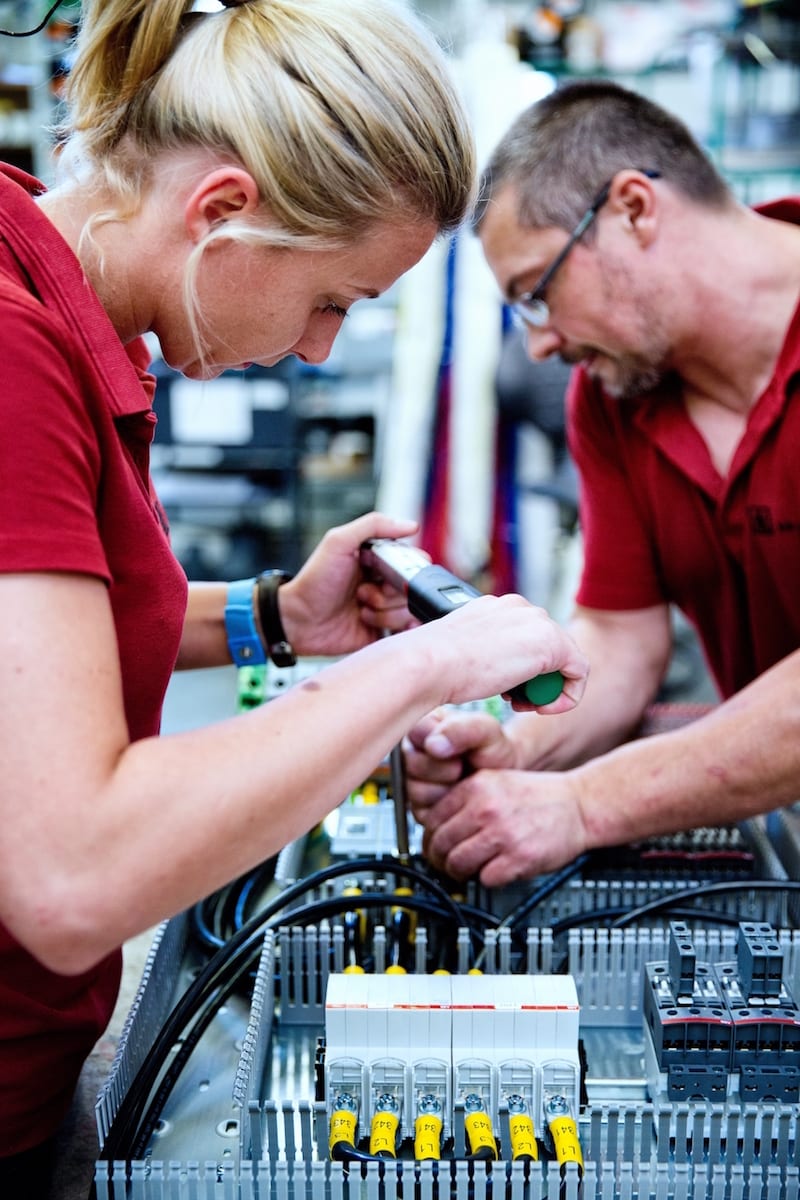
Every product we make has its own specifications, so it was essential to identify the basic tasks that we could teach (for everything else, there is documentation our people can refer to): to do that, we deconstructed the process of assembling our cabinets, isolating the four-five activities that are common to almost every production line, and came up with a standard for each of the tasks.
We created a special area at the gemba dedicated to TWI training, where new hires now spend their first week learning about basic tasks they will be expected to carry out, important documentation, and standards connected with the daily work (like 5S). After that first week, they have enough to get started on the line, where the rest of their learning will develop thereafter, on the job.
We have three different levels of operators on the production lines, to which correspond different levels of expertise:
- operators who finished the first week of training can go to the production line and take on basic tasks that don’t define the final quality of the cabinet (like pre-assembly);
- operators who, after a couple of weeks working, are ready to move on to more complicated activities (like installing wiring inside cabinets);
- and Captains, who are operators responsible for the output of a production line. These are normally more senior employees who have been with us for a while.
Through TWI, we have also made quality checks a part of the standard people follow at every step, which limits the amount of rework we have to do at the end of the process (not to mention, the risk of accidents).
Because of the nature of our production we have put a lot of emphasis on the creation of multifunctional teams: it is very important for us that people can work on different cabinets on other production lines. This is also why our deployment of TWI is based on processes, not production lines.
We have also found that the TWI training we offer in our purpose-built area on the shop floor (it is not sophisticated but it does the job) is a great way to get people familiar with lean tools, like 5S or kanban, which they will use every day.
HOW DID PEOPLE RESPOND TO TWI?
KK Wind Solutions is not new to lean. We have been experimenting with the use of the methodology for nearly a decade. Over the years, lean has given us a 50% improvement in efficiency, drastically improved space utilization and allowed us to gain new contracts (as our capacity improved, we started supplying more than one client at a time). Lean principles and tools – like flow, 5S, kaizen and value stream mapping – have had a huge impact on our business, and we are thrilled that TWI is too. Perhaps its great success is linked to the fact that this approach directly impacts the way our people work, making their life at work easier and more satisfying. Since March, we have trained 200 newly hired people (we currently have four dedicated trainers, each working with a maximum of four people at a time).
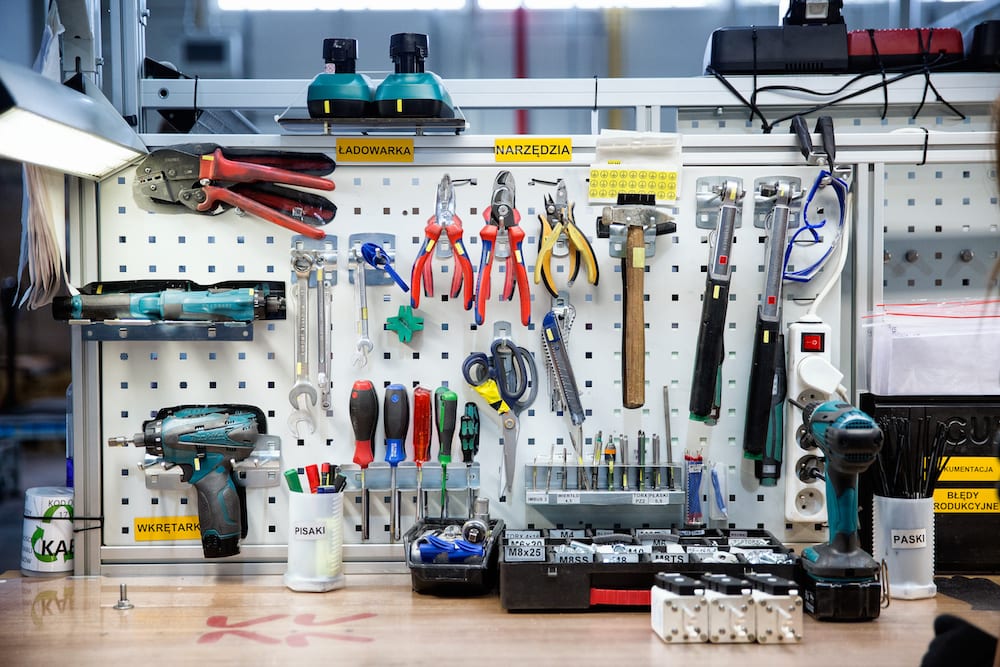
We absolutely see TWI as a way to give our people responsibility. And they responded well to it, once the initial doubts and resistance were overcome: they see they now have an opportunity to learn activities they were previously not involved in (which makes moving from one line to another easy and quick) and even the most experienced operators told us that TWI is a great approach to agree on one method.
While the main focus of TWI is on forming people who join KK Wind Solutions, we of course use it with existing employees, too, to ensure we can sustain standards.
We are noticing a shift in the way we work, and in the results we can achieve together. Before we introduced TWI, there was no standard in place to onboard a new employee, which resulted in the company spending longer than necessary to bring them up to speed and in them not always being able to work to their full potential. With the new training, people join the line with a more versatile mindset and a diverse and tested skills set that they can use on a number of production lines, according to what our demand dictates.
Importantly, we have also recorded a marked reduction in the number of errors made by our employees despite the increase in productivity we have experienced: DPMO (Defects Per Million Opportunities) went down by 30% on average.
This and other improvements are likely a result of a number of our continuous improvement initiatives, but we have no doubt that TWI has had the biggest impact.
For KK Wind Solutions Polska this is just the beginning of our journey with TWI. The second step will be to spread it to the whole factory to make sure that it becomes the way every employee thinks and behaves. We are currently running a pilot project on two of our production lines, before we start applying the new system to the entire production area.
TWI brings us awareness of our daily activities while giving us additional improvements in efficiency, which will help us to gain new clients in the future.We encourage every lean organization to give it a try!
THE AUTHORS
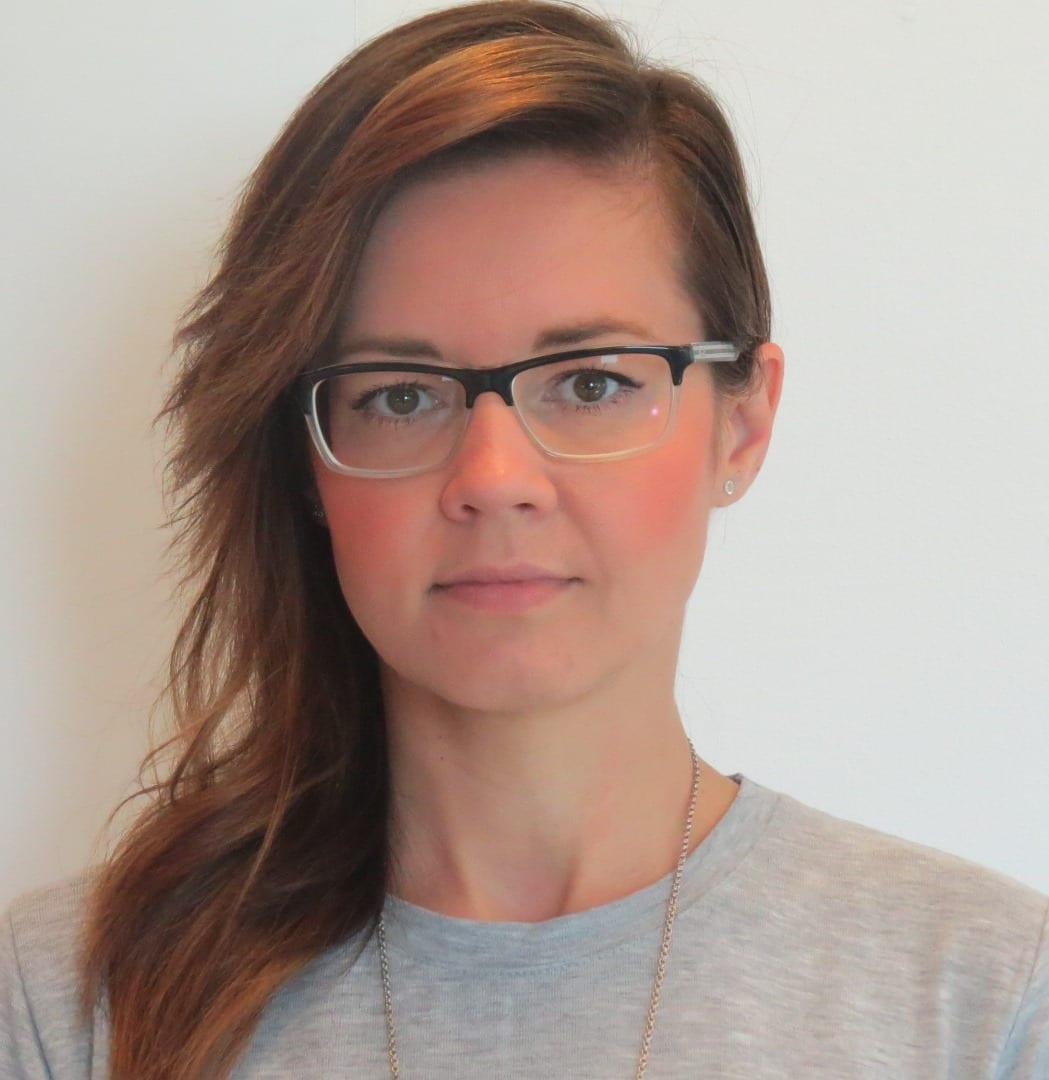
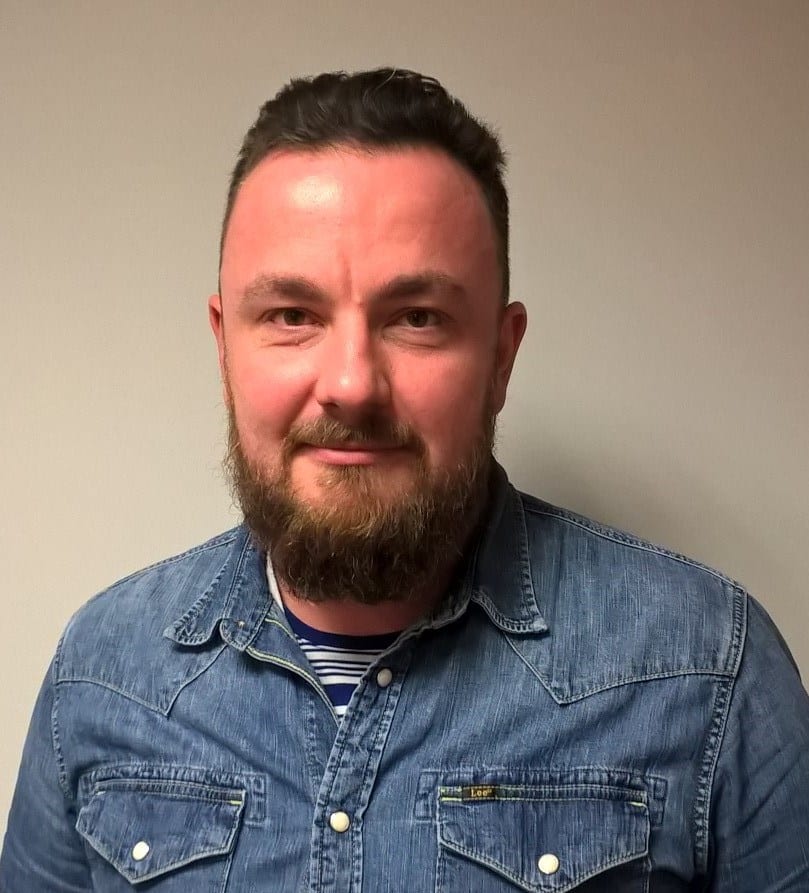
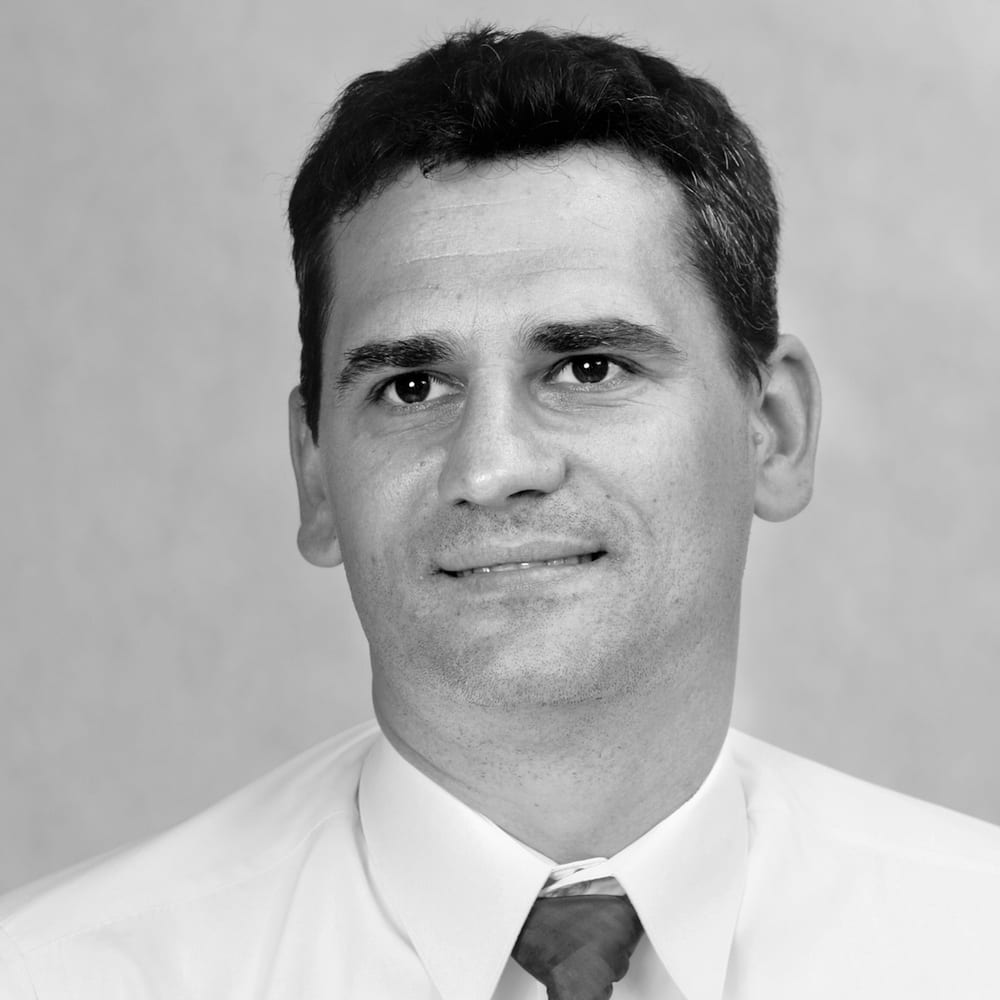
Read more
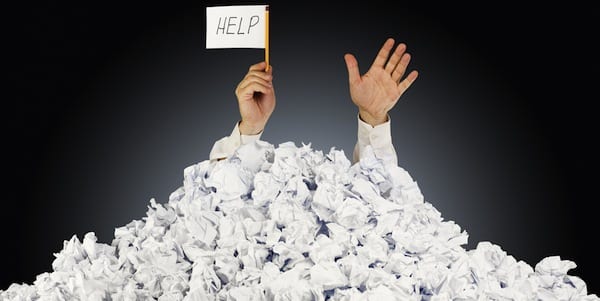
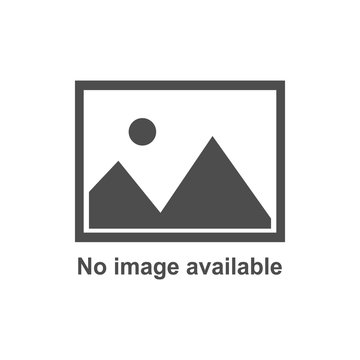
FEATURE - Develop your people if you want to develop a better (lean management) system in your business. This is the key message of this article, which looks at the role of management in an organization and in society.
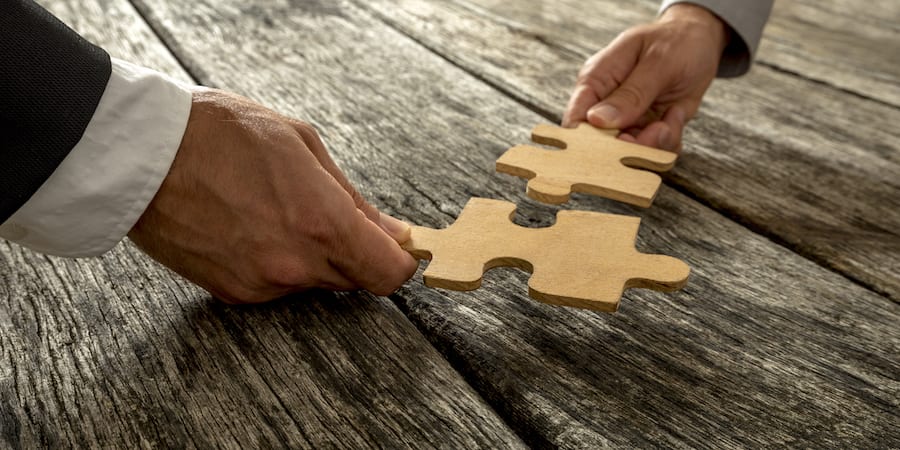
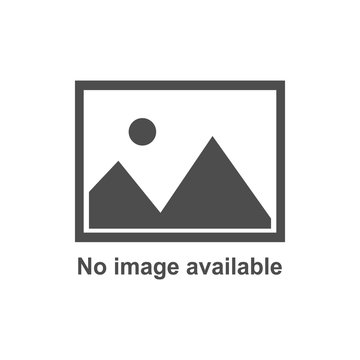
OPINION – After reading the latest book by Edgar H. Schein, the author reflects on the nature of consulting and management, and explains why humility must become a defining trait of both.
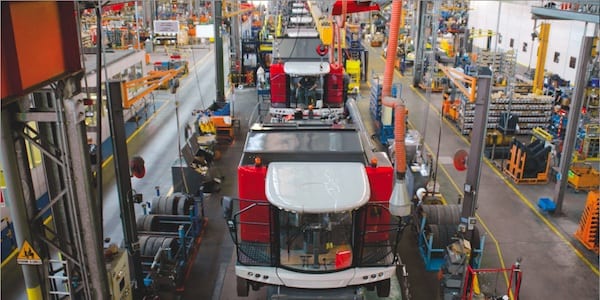
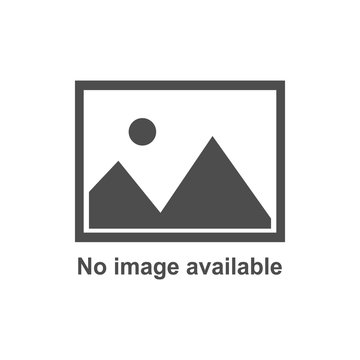
CASE STUDY - An approach based on Lean Daily Management System and experiments in a model area led an Italian manufacturer of combine-harvesters to become one of the leanest organizations in the Veneto region.
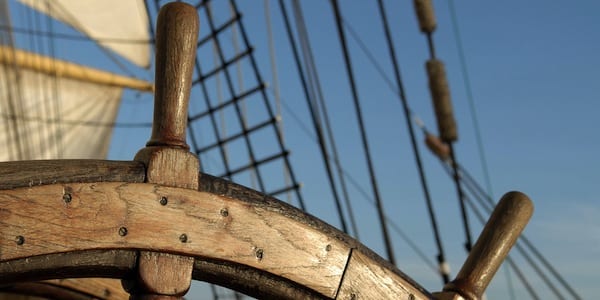
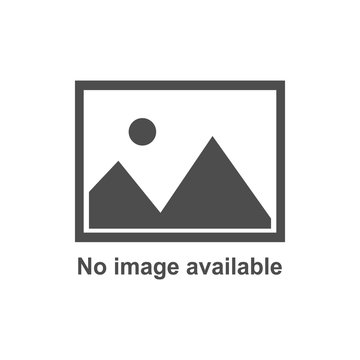
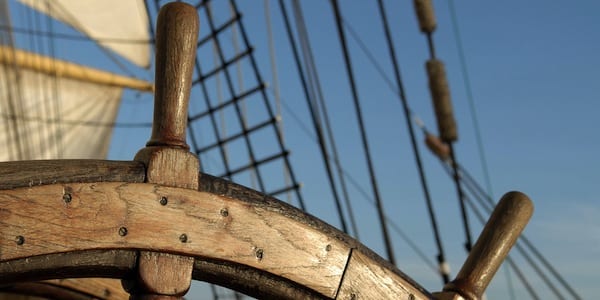
FEATURE - We are often told that employee resistance to change is natural, but it’s really just the result of a wrong approach to lean thinking. Learn to effectively engage people and change will follow.