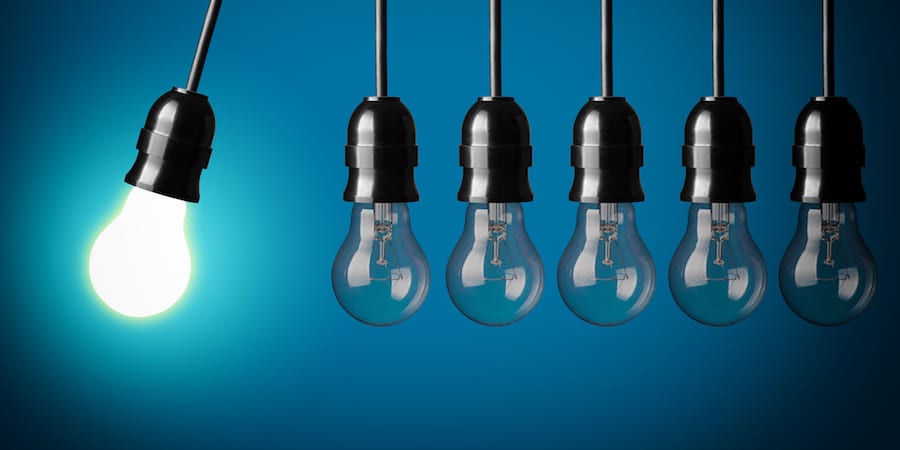
Five lean practitioners answer the same question #4
1 QUESTION, 5 ANSWERS – Without the active participation of people in improvement activities, lean is nothing but theory. Sadly, engaging folks is easier said than done. We asked five lean practitioners to share their approach to people engagement.
"What is your strategy for engaging people in lean activities?"
KRISTIAN LINDWALL, Agile Coach, Spotify – Stockholm, Sweden
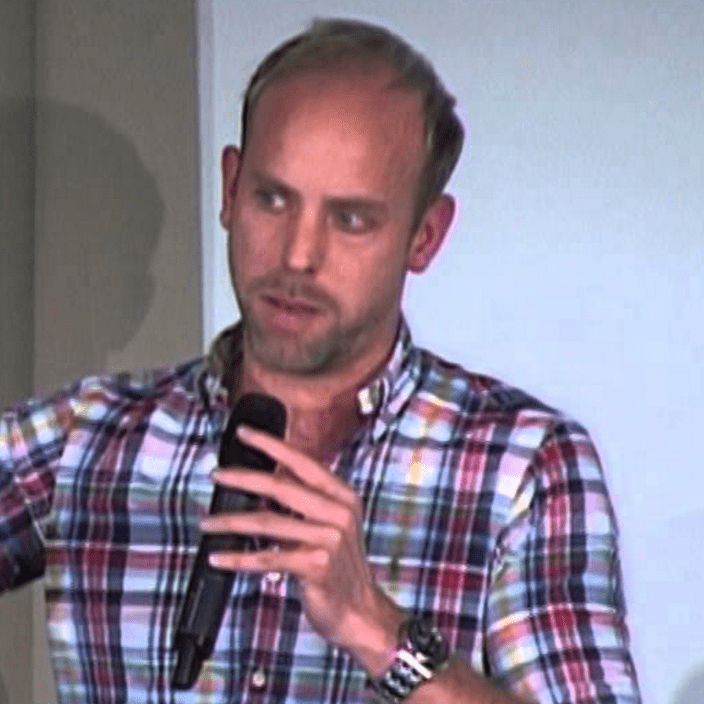
"Lean activities" can mean a lot of things. One key aspect of lean is continuous improvement, and that's what I would like to focus my answer on. I like to think about continuous improvement at different levels: individual, team and organizational. In Spotify’s engineering department, we have a number of roles and activities that are there largely to foster a culture of continuous improvement.
As an individual member of the team, you are part of a chapter, which is headed up by a chapter lead (who is also your manager). The chapter acts as a vessel for individual growth, both through a close relationship with your manager and via activities, such as Lunch and Learns and internal presentations. We also have numerous guilds at Spotify, open for anyone to join. They focus on specific areas of interest (like iOS or leadership) and are there to support the growth of their members.
An important role for us, focused on team improvement, is the agile coach. We currently employ around 30 agile coaches across the organization. They are experts in how to foster good team dynamics, practices, processes and how to create an environment that promotes continuous improvement. They facilitate retrospectives, post mortems and many other tailored exercises to keep pushing our teams to constantly improve and deliver the best music experience.
We also have teams whose sole purpose is to oversee the entire organizational model of Spotify’s operations. They have a holistic perspective of the company and have taken on challenges like our operational rhythm and onboarding. Company-wide activities such as our hack weeks are also their prerogative.
CATERINA BIANCIARDI, Lean Manager, Siena University Hospital (Azienda Ospedaliera Universaria Senese) – Siena, Italy
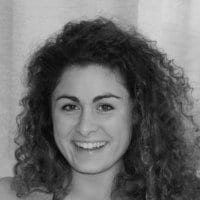
Lean can be defined as an improvement culture that makes use of many technical tools. The term “culture” has different meanings, but it is generally used to refer to the set of values, standards, beliefs and practices shared by a particular group. In this sense, for a culture to take roots we need to commit to people engagement by helping our people to grow and blossom – it’s no coincidence the word “culture” comes from the Latin colere (to cultivate).
Indeed, the essence of the lean thinking system is the involvement of our employees. Listening to them, appreciating their ideas, helping them solve their problems is a great way to make them feel part of the new culture we are promoting. As a lean office we give support to all our professionals who want to develop their own improvement project, so that they can appreciate the method and the results that the application of lean tools brings.
BORIS EVESQUE, Director of a train maintenance center – France
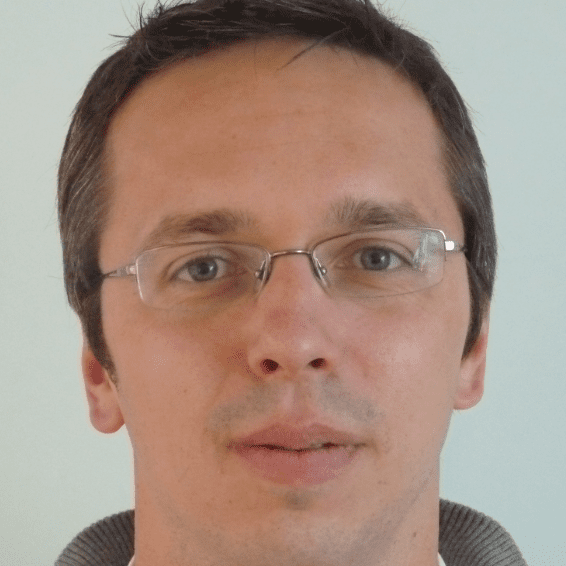
As the director of the plant, my approach to engaging people is: to commit to learning lean myself, to try to teach it to the managers of the plant, and to show a continuous interest in improvement activities at the gemba. In concrete terms, we have rigorously scheduled short reviews: daily lead-time reviews, daily discussion in front of a team’s problem solving and kaizen boards, weekly 5S visits, weekly A3 reviews, and so on.
At first glance, one could think we are looking to build of a blindly obedient structure in our organization, when really what we are interested in developing is both teamwork and a deep interest for the product. After all, our organizational strategy is to cultivate a strong desire to increase our technical mastery in order to improve customer service.
DEANNA HALL, Continuous Improvement Facilitator, Kinross – Round Mountain gold mine, Nevada, USA
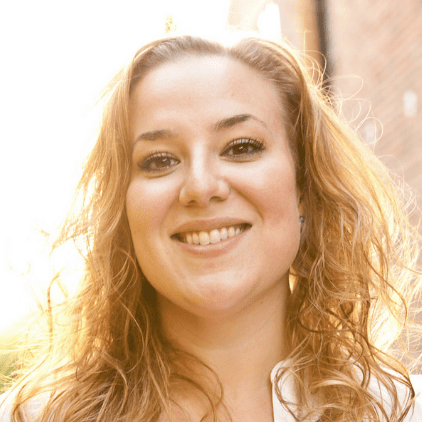
Our strategy for engaging our people is to ensure that they know we are all part of a continuous improvement team. We emphasize that our role is to support, not direct, and that only by working together will we be successful.
We engage our new hires within the first week. We have a motto that even with little experience, a fresh set of eyes can identify opportunities from new perspectives. We emphasize the importance of a closed feedback loop of communication between the employees, support groups, and section managers/team leads with the use of CI Boards (visual suggestion boxes). In addition, 40 high potential employees from all areas of the operation are invited to participate in a Key Concepts of Lean training session every six months.
We believe that feedback and recognition are vital to the success of our improvement culture. We hold monthly update meetings for site leadership, presenting current, future, and cash-flowing initiatives to generate continued engagement and support for continuous improvement. By sharing successes from other areas of the site, our goal is to encourage employees to become enthused to identify opportunities for improvement in their own areas. We feel that by receiving recognition for improvements achieved, they develop a stronger sense of pride in the workplace.
AYBERK KURT, former Lean Transformation Coordinator, Uludag University Hospital – Bursa, Turkey
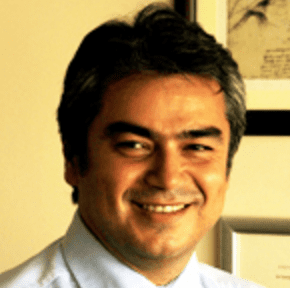
Our strategy to engage people in lean efforts focuses on trying to change our leadership team’s overall mindset and management style, and transforming them into lean leaders through our leadership development program. We know that people tend to be more engaged when taking part in activities to which they can contribute with their personal strengths, and that they feel fulfilled when they invest effort in projects that are larger than them. But before all of that, they need to become committed, they need to see – physically – that management itself is committed to the mission. They need to see that their organization has set clear goals and expectations for them, as well as setting up the right training programs for their development. They need to see that their managers respect their views and expertise, that they are there when they need them and that they can coach them, as well as empower them in their efforts by making their working environments better, for them and for their customers.
Sustainable employee engagement can only be established if leaders are willing to address the barriers to participation that stem from their own behaviors and replace the traditional command-and-control mindset with the lean leadership approach.
Read more
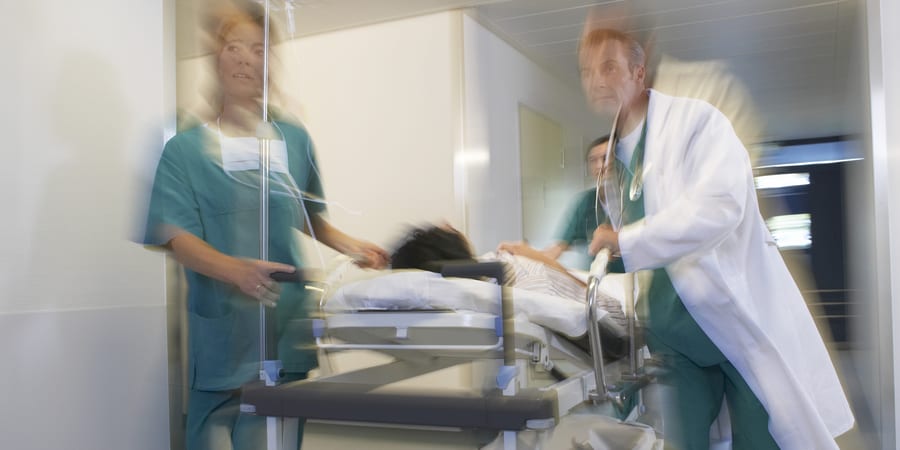
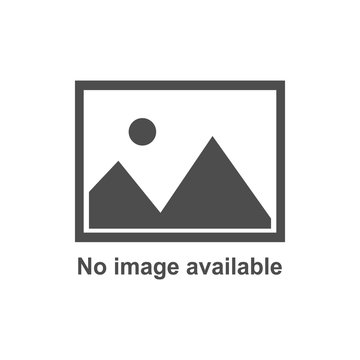
FEATURE – You don’t always need a lot of external help to initiate a lean transformation: the experience of the Emergency Department of the Hospital Clínic of Barcelona shows it can be done with very little support from the outside.
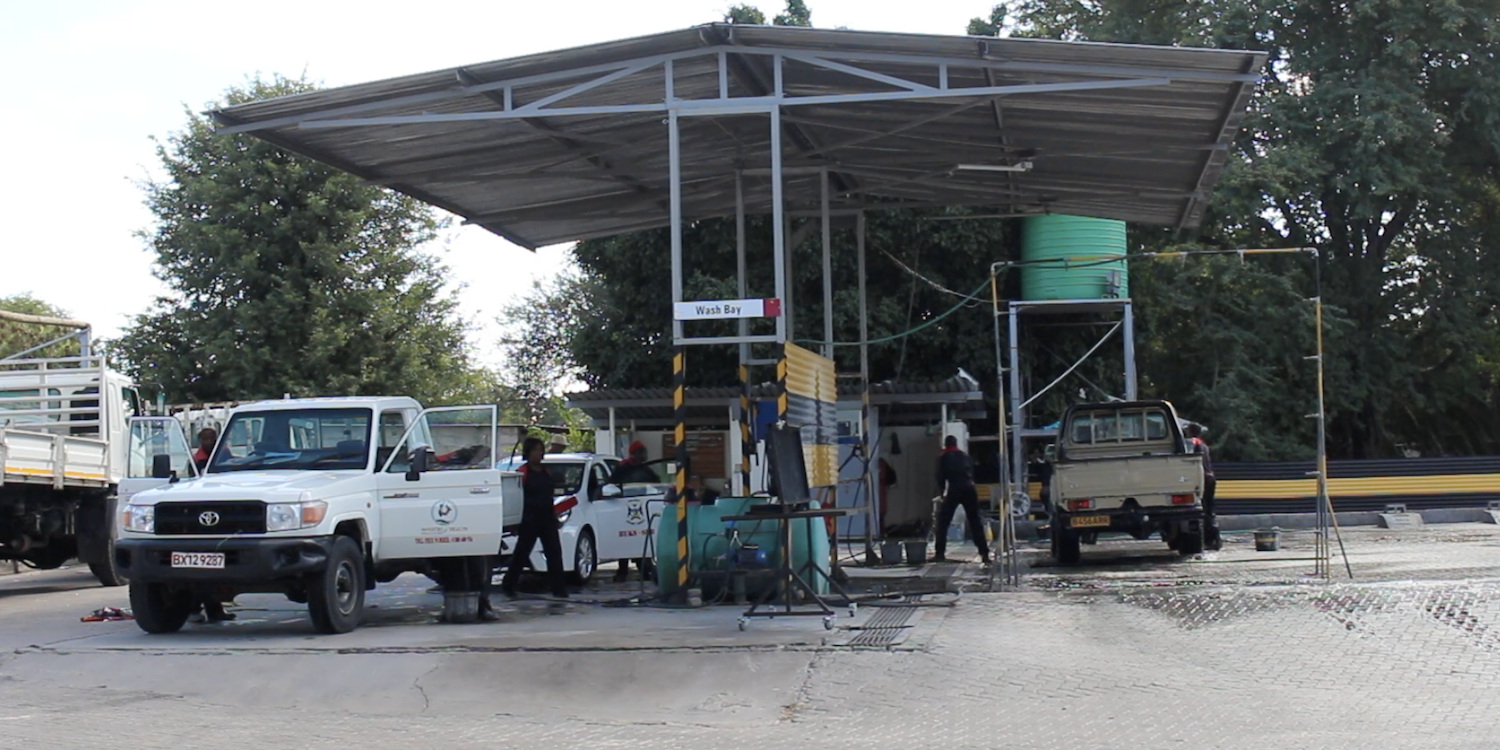
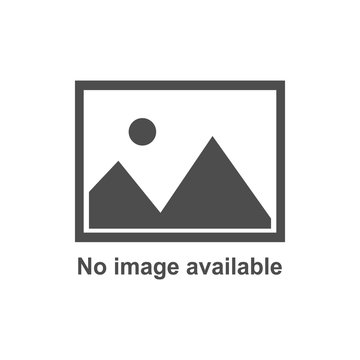
FEATURE – A leader’s creativity and care for her people can lead to extraordinary results even in the most challenging of environments. As the latest LGN book comes out, the author reflects on one of the most impressive lean transformations you will come across.
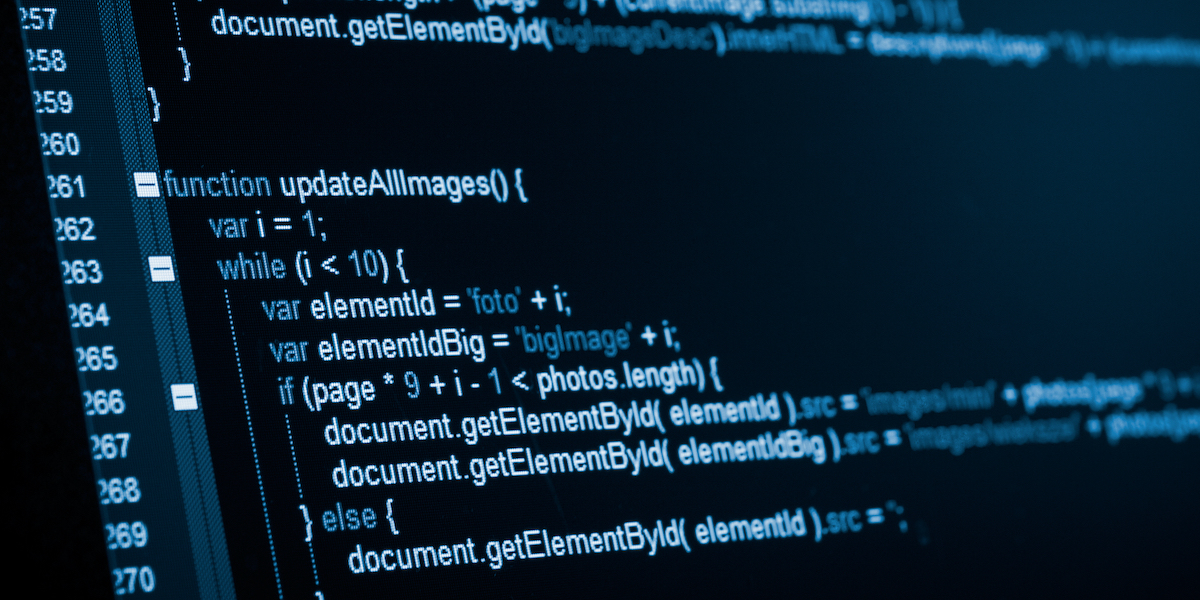
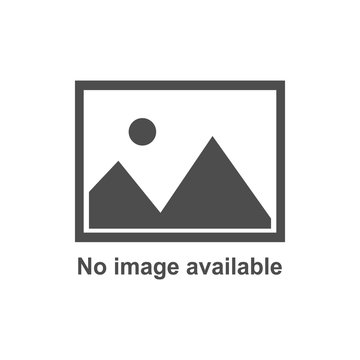
FEATURE - The author explains how a recent book on radical quality improvement in manufacturing inspired him to initiate similar experiments in his software development firm.
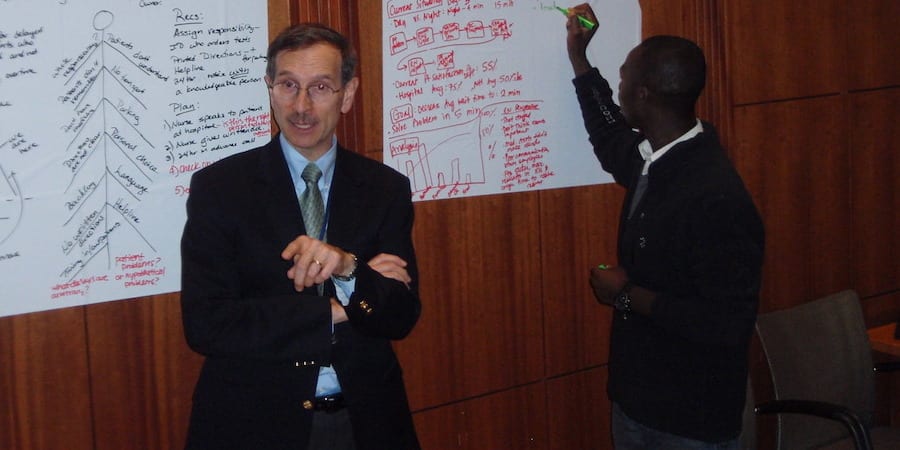
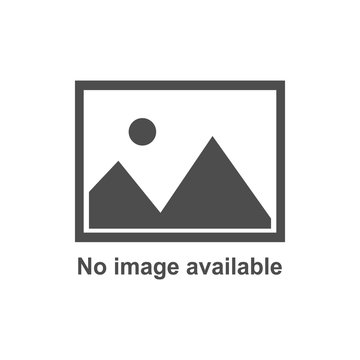
PROFILE – Another month, another inspiring profile of a lean practitioner. We were impressed by Dr Billi’s deep conviction in the idea that, first of all, leaders must be learners. You will be too.