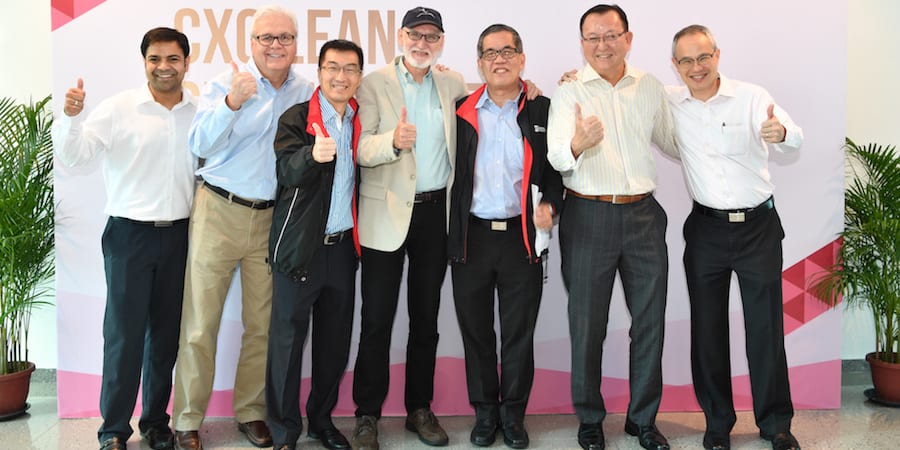
An alliance to bring lean capabilities to Singapore
FEATURE – Last year, the Lean Global Network entered a partnership with the Singapore Institute of Technology to bring lean capabilities to local SMEs. Along the way, we discovered an alternative approach to academic teaching.
Words: Jikku Mohan and René Aernoudts, with Arthur Poh
Back in 2013-2014, as part of our efforts to have a growing impact in the world, the Lean Global Network was looking at Southeast Asia with great interest. Singapore immediately appeared as a very attractive base from which we could spread our lean influence in the region: the city is strategically located, business-minded, and cosmopolitan.
As we looked for opportunities to establish a presence in the city-state, we found that the Singapore government was grappling with a major social and economic challenge that could hinder its future growth: a labor shortage due to a low birth rate and an ageing population.
To try and mitigate the negative effects of this manpower-related issue, in October 2015 the Ministry of Manpower introduced the Lean Enterprise Development (LED) Scheme, which hopes to boost the competitiveness of Singaporean small- and medium-sized enterprises (SMEs) –largely owned and run by locals, rather than expats.
Over the years, there had been many government-sponsored initiatives to bring innovation capabilities and productivity increases to Singaporean companies (some dating back to the 1970s), but they failed to yield sustainable results. We learnt that the government strategy had been performance-driven, with a stronger focus on KPIs than on developing capabilities at the front line (the only way to ensure the sustainability of results). Furthermore, these efforts had mainly focused on the manufacturing and engineering space.
The LED Scheme clearly represented a shift in the government’s approach: they now wanted to develop capabilities in SMEs, with a particular focus on the service sector. Naturally, this sounded like a great opportunity for us at the Lean Global Network, to not only impact a whole country, but also to offer SMEs an alternative way of operating. Indeed, our approach to spreading lean thinking and practice has always had the development of capabilities at its heart.
As our search for a local partner continued (we knew from the beginning that the best way forward would be for us to find a local organization that could help us navigate the complexities inherent to starting a new adventure in a new location), the government introduced us to the Singapore Institute of Technology (SIT).
SIT is a newly-established university that strives to teach practical skills (alongside the theory) to train work-ready graduates. Their Learning Enterprise Model, which focuses on training companies to co-create solutions to their day-to-day business challenges, echoes our own approach to spreading lean. Indeed, our mission immediately appeared to be very much in line with SIT’s – not only empowering people to transform their organizations by teaching them practical skills, but also encouraging lean practitioners to come together and share their experiences (for example, through the annual lean summit SIT organizes).
So, around a year ago, the Lean Global Network and the Singapore Institute of Technology started a three-year partnership to develop faculty and support SMEs by developing lean leaders. We shared views, and now we are happy to share a mission with SIT: making a difference for Singapore.
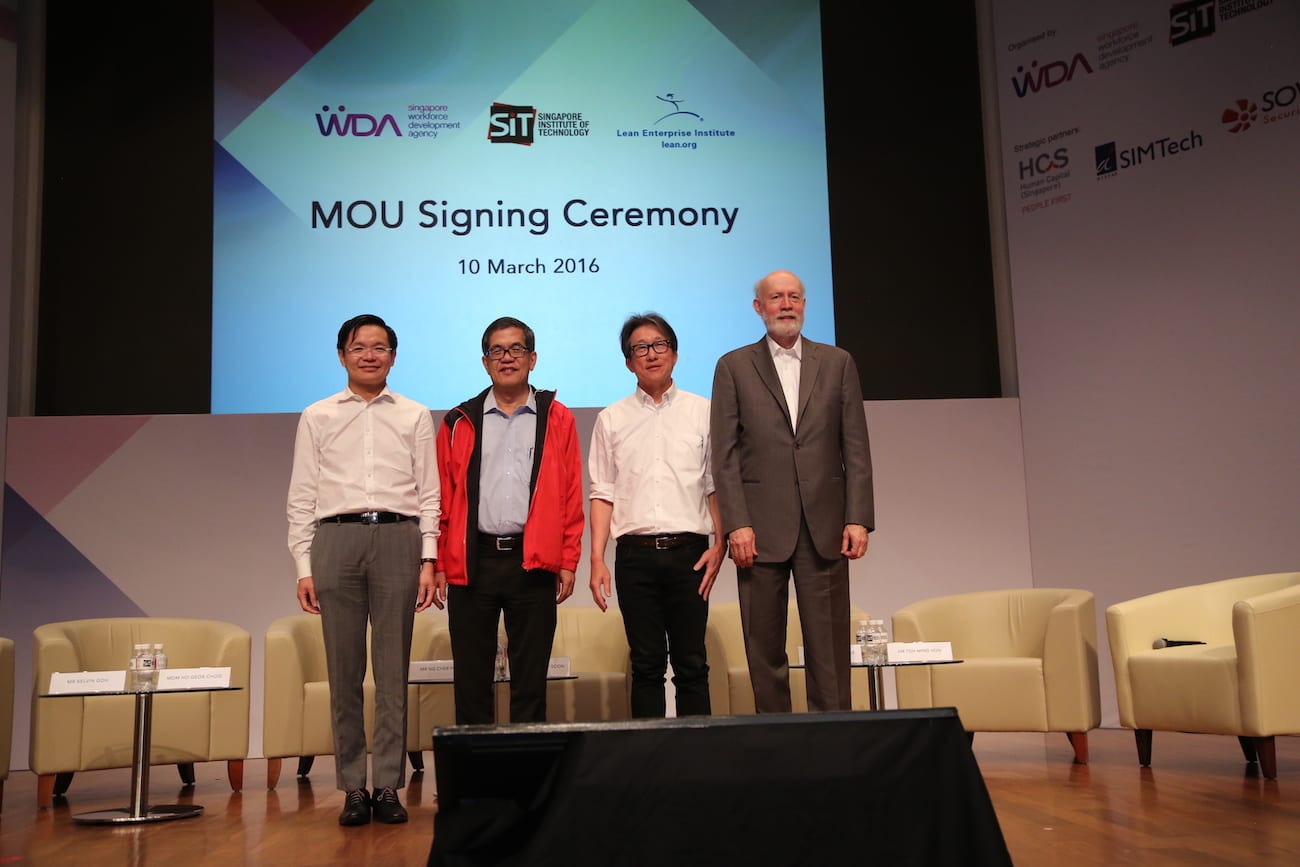
A NEW MODEL FOR ACADEMIA?
The first outcome of this new tripartite relationship – between LGN, SIT and Singaporean companies – was the creation of the Lean Transformation Innovation Center (LTIC). Its purpose is:
- to help the SMEs participating in the program to achieve sustainable business results;
- to develop the capabilities of the employees to enable continuous improvement;
- and to develop the capabilities of SIT faculty to develop Singapore’s future workforce.
The academic world is often criticized for having too strong a focus on theory and for largely neglecting practice. When our experiment with SIT began, it quickly became clear to us that what we had on our hands was a potentially different model for universities to interact with industry and spread knowledge.
Together with SIT, the LGN has put together a lot of activities that can benefit Singapore and its economy, from workshops to summits. We even have plans to create a Learning Lab for school students! The core of our work, however, is the co-development of the Lean Skills Development Program (which is largely based on the LGN’s Lean Practitioner Program).
The five-month program is designed to give participants a theoretical understanding of the lean body of knowledge, followed by practical application of this knowledge at companies to address a real business need. Our objective is to show meaningful improvement in the performance of the companies and develop key people within the businesses so that results can be sustained going forward. In the first year of this partnership, we have worked with a dozen companies in Singapore – including Mount Alvernia Hospital, NTUC adult training center, noodle manufacturer TSK, car workshop Motor Edgevantage, and Polystyrine resin producer TPSC.
But there is more: when we visit a company, faculty members from SIT join us, so that they, too, can learn lean in a hands-on way and then teach it to their students at the university.
But this is not to say that the Lean Global Network isn’t learning as well. The Lean Skills Development Program is delivered by coaches from four of our institutes – the Lean Enterprise Institute in the US, the Lean Enterprise Australia, Lean Management Instituut in the Netherlands, and the Instituto Lean Management in Spain – and this for us is a great learning opportunity.
Sharing our experience as individual institutes and comparing our approaches to co-create something for and with organizations is extremely beneficial. The fact that we can do it with a likeminded partner, with whom we have established a remarkable relationship, makes it all more enjoyable and impactful.
We see SIT as a unique university – one we are proud to join forces with – and encourage academic institutions around the world to learn from their approach to knowledge development and sharing. Injecting on-the-job training and the development of practical skills into curricula would fill a gap currently present in the offering of most universities, while creating better outcomes for students and society.
That’s what we hope to achieve in Singapore. We’ll let you know how our experiment plays out.
A message from John Shook
Chairman of the Lean Global Network
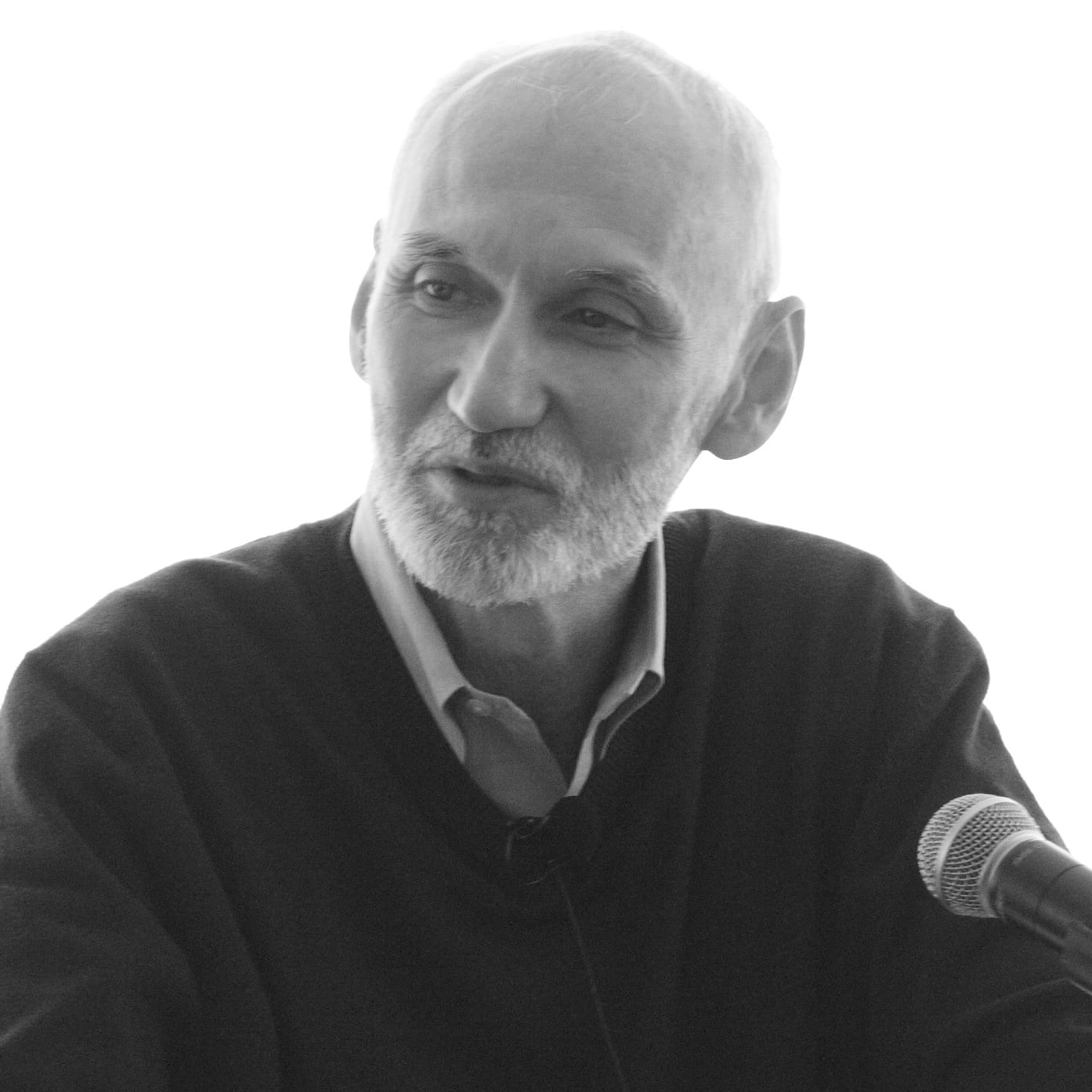
During our series of reconnaissance visits to Singapore to meet potential partners, we were not set on what type of organization we would have liked to work with. We were determined only to find an organization that was willing to try some experiments that could meet both our learning needs and theirs. This could have been a company, a government agency, or it could have been a university. Eventually, it was Singapore Institute of Technology that emerged as not only eager but was also likeminded; there is no doubt that our shared goals and aspirations have made for a “marriage” that, we hope, will have a positive impact on Singaporean companies.
Like everything we do at the LGN, this is very much an experiment – a multi-faceted one at that. It touches on how we, as a network, can support an entire country (and from there influence a region); on how we can help SMEs, which represent the largest share of companies in the world economy; and, perhaps most importantly, on how we can engage with universities in an effective way.
We especially like the fact that SIT, as a university, has a strong focus on developing practical skills. This is completely in line with what we stand for. Our roots rest firmly in traditions that stress the value of experiential learning - learning through doing. As a Lean Community, over time we have learned that the impact of what we do can only be measured by what happens after we are gone – and that sustainability is impossible without developing lean thinking capability in organizations. So, knowing that we can’t fully support lean transformations from a distance and that our time with the companies participating in the program is limited, we made an effort right at the outset to structure the training program to ensure as much sustainability as possible. And this means simultaneously developing lean skills in companies and in the university.
I think that’s the most important part of our experiment with SIT: partnering with an academic institution to provide companies with hands-on lean knowledge and skills they can carry with them into the future.
THE AUTHORS
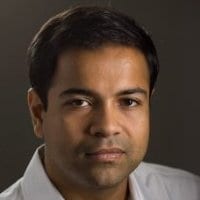
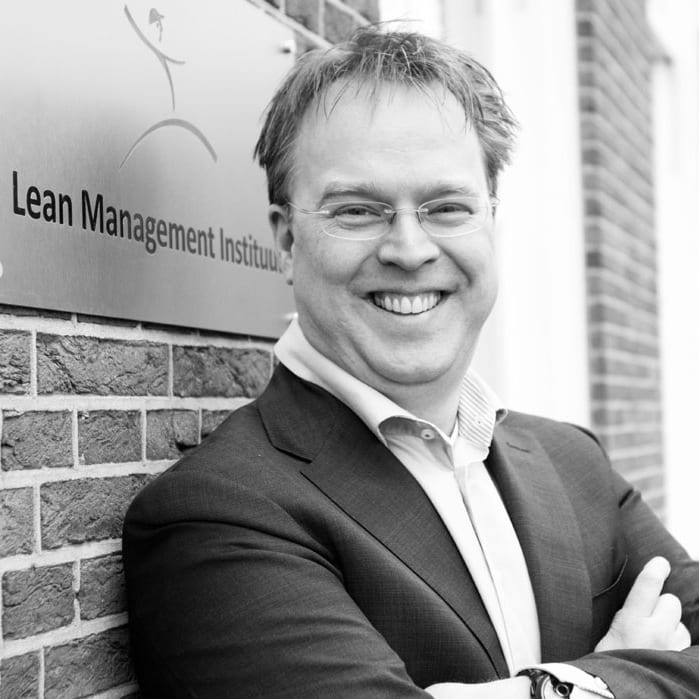
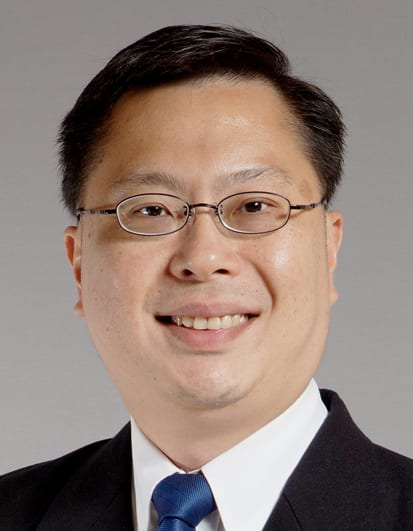
Read more
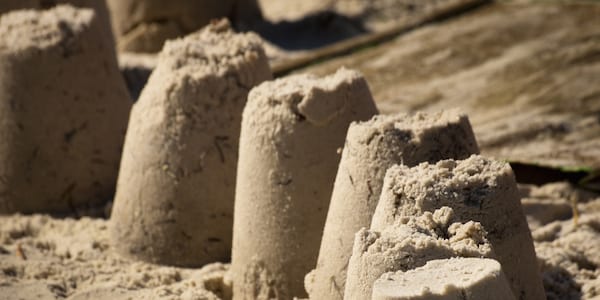
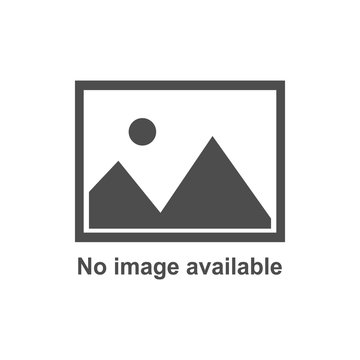
FEATURE – In a transformation, should we spread responsibilities across the business or go for a centralized Lean Office? For their second piece, our Polish colleagues look at what they have learned on the field.
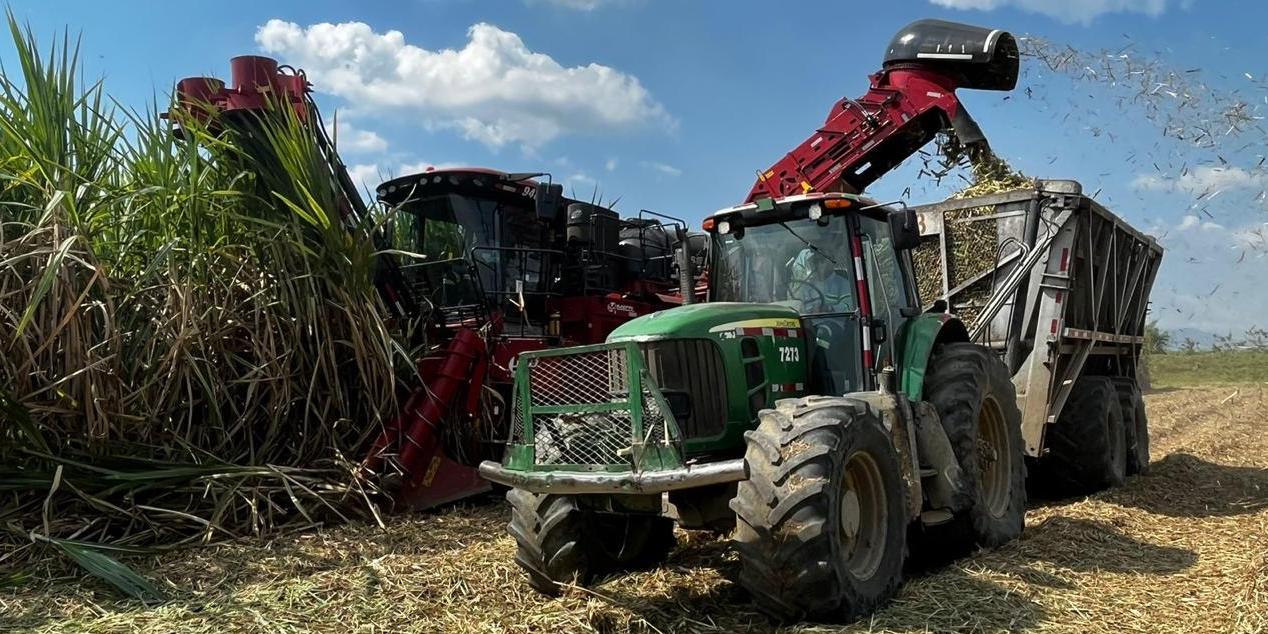
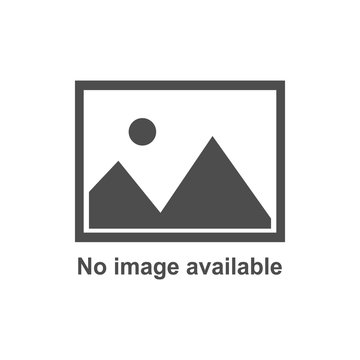
CASE STUDY – Manuelita Sugar Mill in Colombia adopted Daily Management to bolster leadership effectiveness and operational outcomes, addressing siloed thinking and communication challenges.
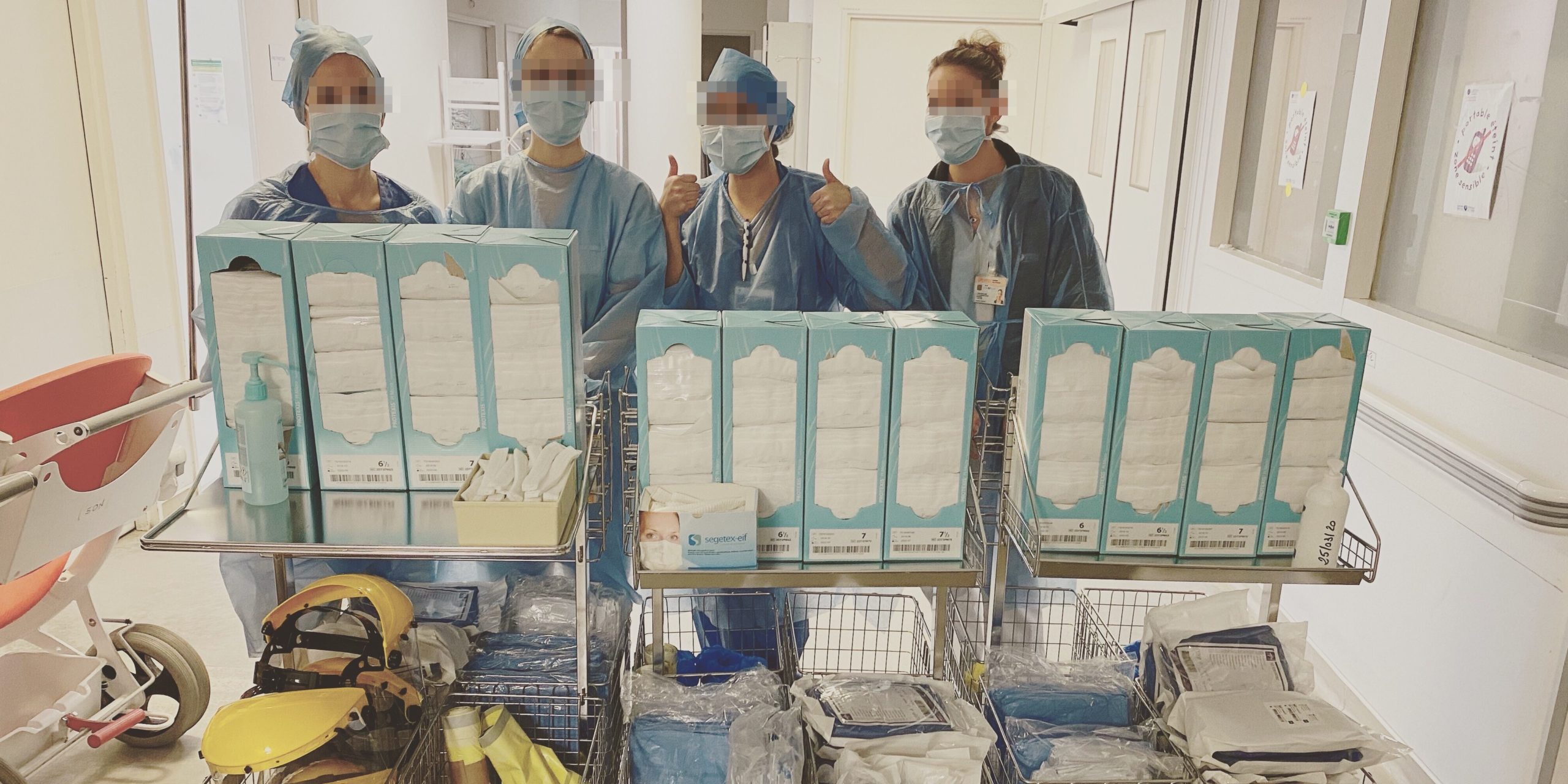
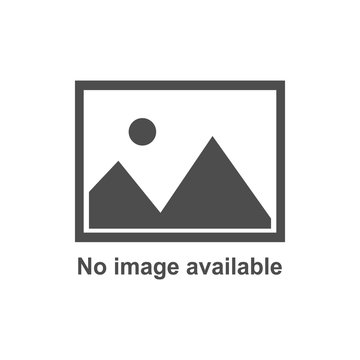
NOTES FROM THE (VIRTUAL) GEMBA – This small manufacturer is relying on Lean Thinking to keep the business running during the Covid-19 crisis, overcome the disruption in its supply chain, and even innovate.
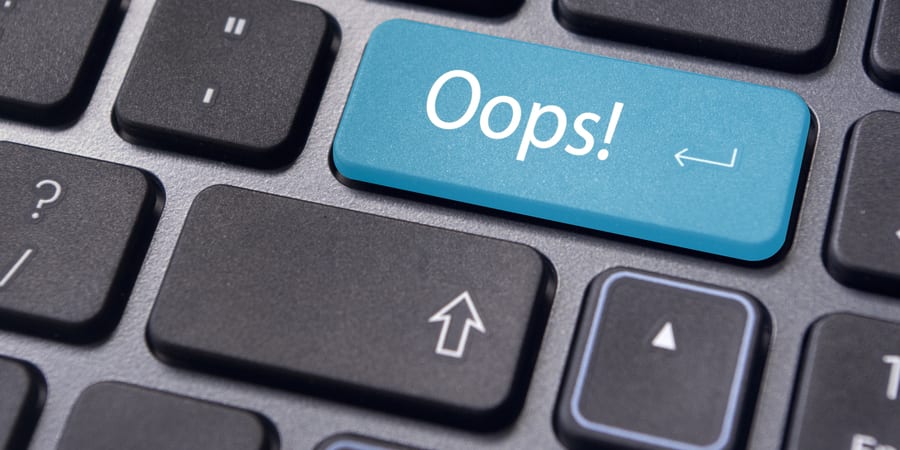
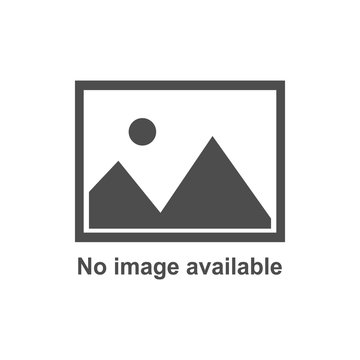
FEATURE - Traditionally seen as the mother of all evil, the IT department in our organizations has a long way to go before it fulfils its potential and becomes an actual facilitator in the delivery of excellent products and services. In the past few years, IT leaders have realized that lean management can help them to transform the function.