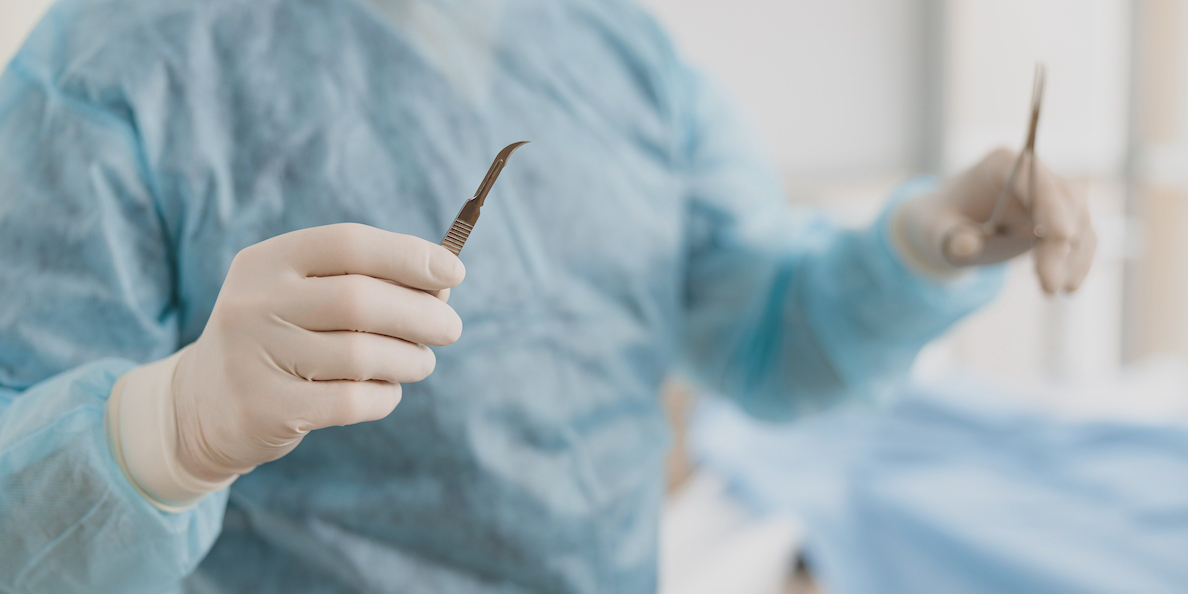
A Surgery Department on a journey for over a decade
FEATURE - This surgery department was among the first areas in this hospital (maybe in the whole of Spain) to adopt Lean Thinking. Here's what their lean journey is focusing on more than 10 years after they started.
Words: Dr Xavier Pérez, Head of Surgery, Consorci Sanitari del Alt- Penedès-Garraf
The Surgery Department that I run was one of the first areas to initiate lean experiments in the Consorci Sanitari. We have been at it for many years, which means that many of our processes – and the way we track them – are now solid and don’t need constant follow-up. We are tracking the same KPIs we have always tracked, but we only highlight their performance when we detect some kind of deviation. In that case, we reactivate them and, if the problem warrants it, we open an A3 to detect the root cause of the problem, identify countermeasures and track the results using our KPIs.
When you have been on a lean journey for as long as we have, one of your challenges is maintaining the focus and the enthusiasm for improvement. Of course, results still are the number-one motivator for our people. If they work hard to improve a process and impact its respective KPIs, but ultimately can’t achieve the desired results, they will lose motivation. Conversely, if they generate improvement and contribute to the elimination of waste, they will feel empowered to carry on. Because we are aware of this, we are trying to be more transparent when it comes to sharing results with the Department: until around six months ago, results were presented to a small committee, whereas now, once a month, we use our weekly surgery planning meeting, in which all managers participate, to provide a summary of how the indicators are going. We weren’t communicating effectively before, and we are hoping to renew engagement with this new approach.
As a department, we have also been relying on the Hoshin methodology. It’s a very simple tool, and it is extremely effective at telling us, visually, where the problems are. It helps us to pick our battles, so to speak: for example, if a bottleneck is caused by an IT problem or a financial one, we know immediately that we are not going to solve it, at least not right away, and that we should find another solution.
Speaking of the battles we are fighting, we are currently focusing on the traceability of the patient from the moment they enter the Surgery Department to the moment they are discharged. This can potentially have a huge impact on avoidable cancellation, which has always been our Achille’s heel, our toughest indicator to improve. We still have a way to go to get where we want to be, but we have begun to work on the productivity of the Surgery area in order to make full use of our capacity. Patients coming in for surgery can come from the ER, from other wards, from their home, and that’s why tracking them can have such a big impact on cancellations. Another countermeasure we have implemented to tackle this problem is dedicating one of our new operating rooms exclusively to urgent procedures, which are currently one of the main causes for cancellations. We will also be measuring the time between a patient being deemed in need of a surgical procedure to the moment they enter the OR, to try and shorten it and, therefore, improve utilization further.
THE AUTHOR
Xavier Pérez is Head of Surgery, Consorci Sanitari del Alt- Penedès-Garraf
Read more
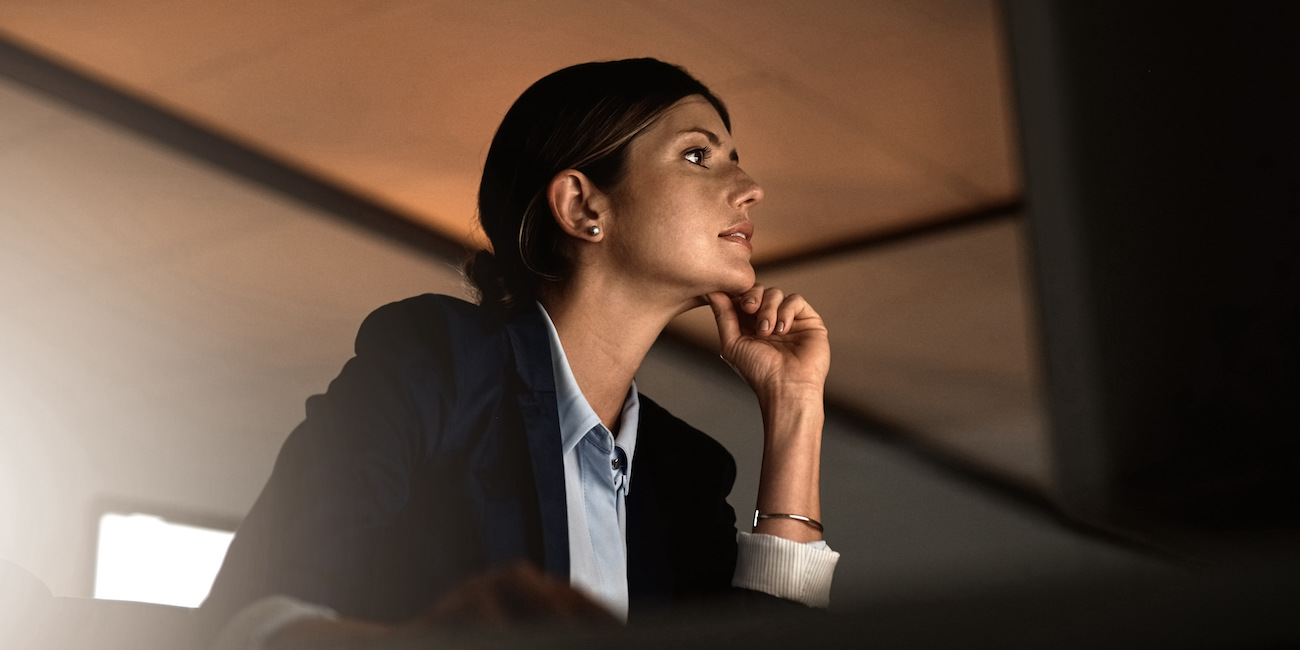
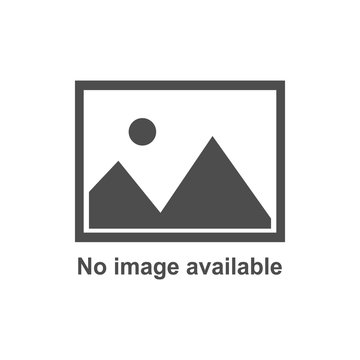
FEATURE - The Basic Thinking dimension of the Lean Transformation Framework is often the most neglected and the least understood. The author tries to shed a light on the subject.
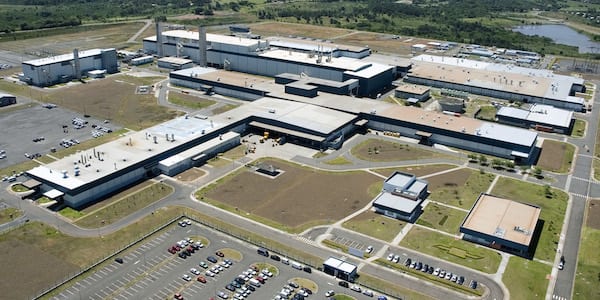
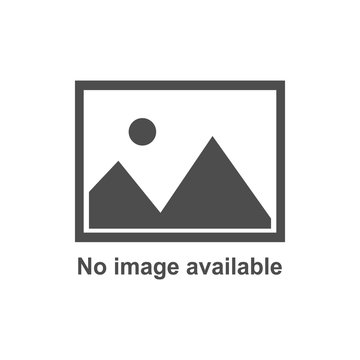
INTERVIEW – We speak with Sérgio Caracciolo of General Motors do Brasil about the carmaker’s approach to lean, its struggles, and its lessons learned.
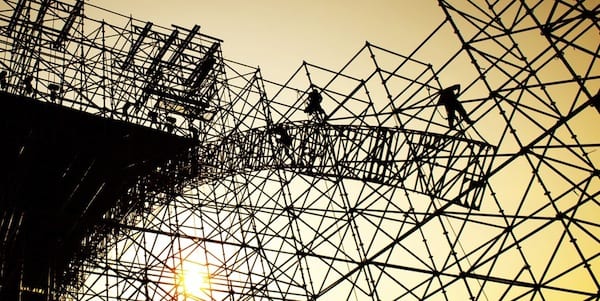
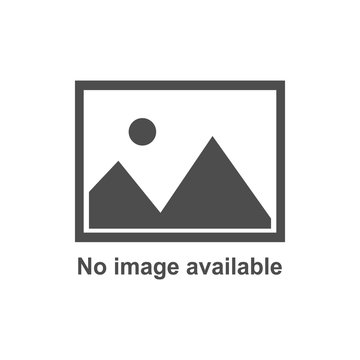
RESEARCH - For most CEOs, working with a sensei is common practice. Yet, many questions remain on this role. This paper aims to bring clarity to the "sensei mystery".
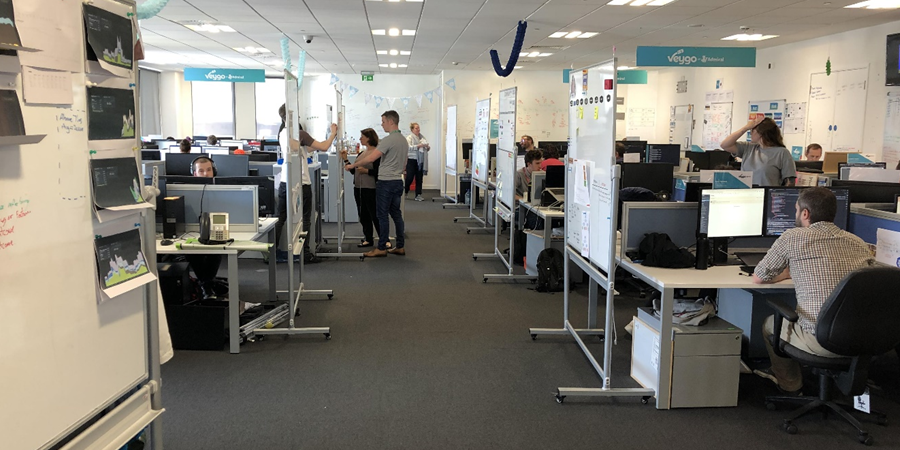
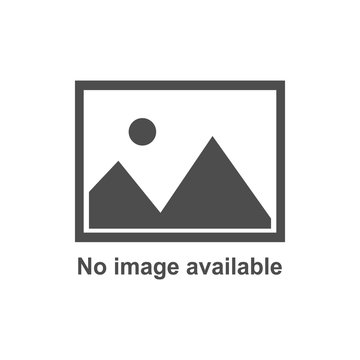
NOTES FROM THE (VIRTUAL) GEMBA – This week, the author chats with an innovative insurance company as it relies on its lean learnings to ensure business continuity and switch to remote working during the Covid-19 crisis.
Read more
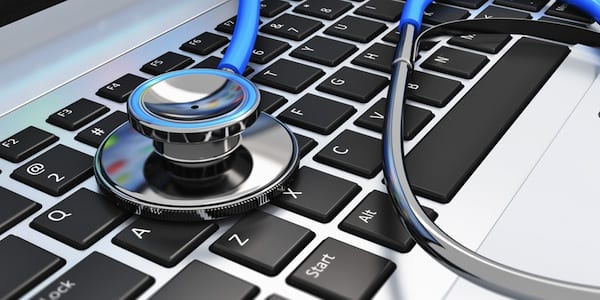
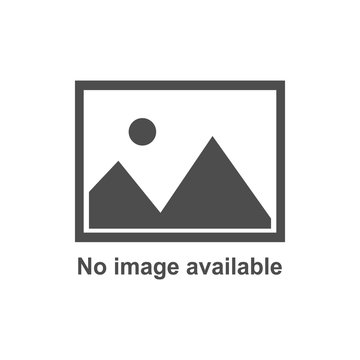
COLUMN - In the third article of our series, the CEO of a healthcare institution in Catalonia, Spain, discusses the implementation of lean as a mindset that has its foundations in continuous improvement.
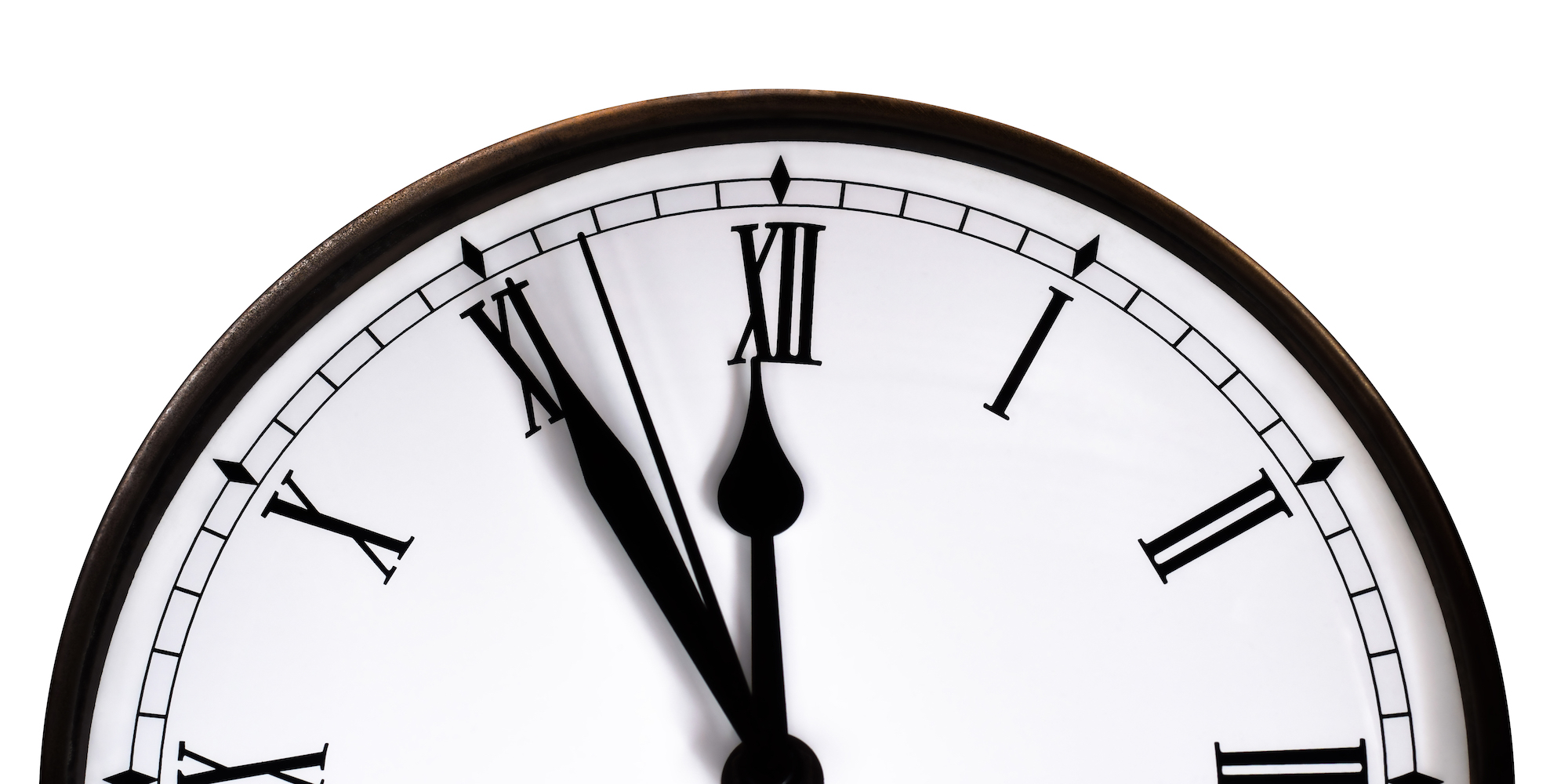
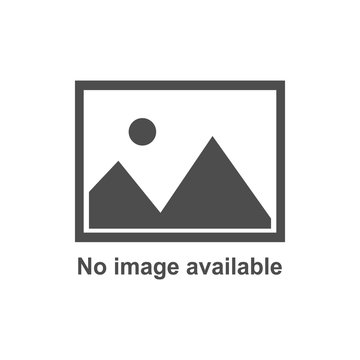
FEATURE – Freeing up beds is an age-old problem for hospitals. The medical area of this Catalan hospital group has found in lean a creative way to solve it.
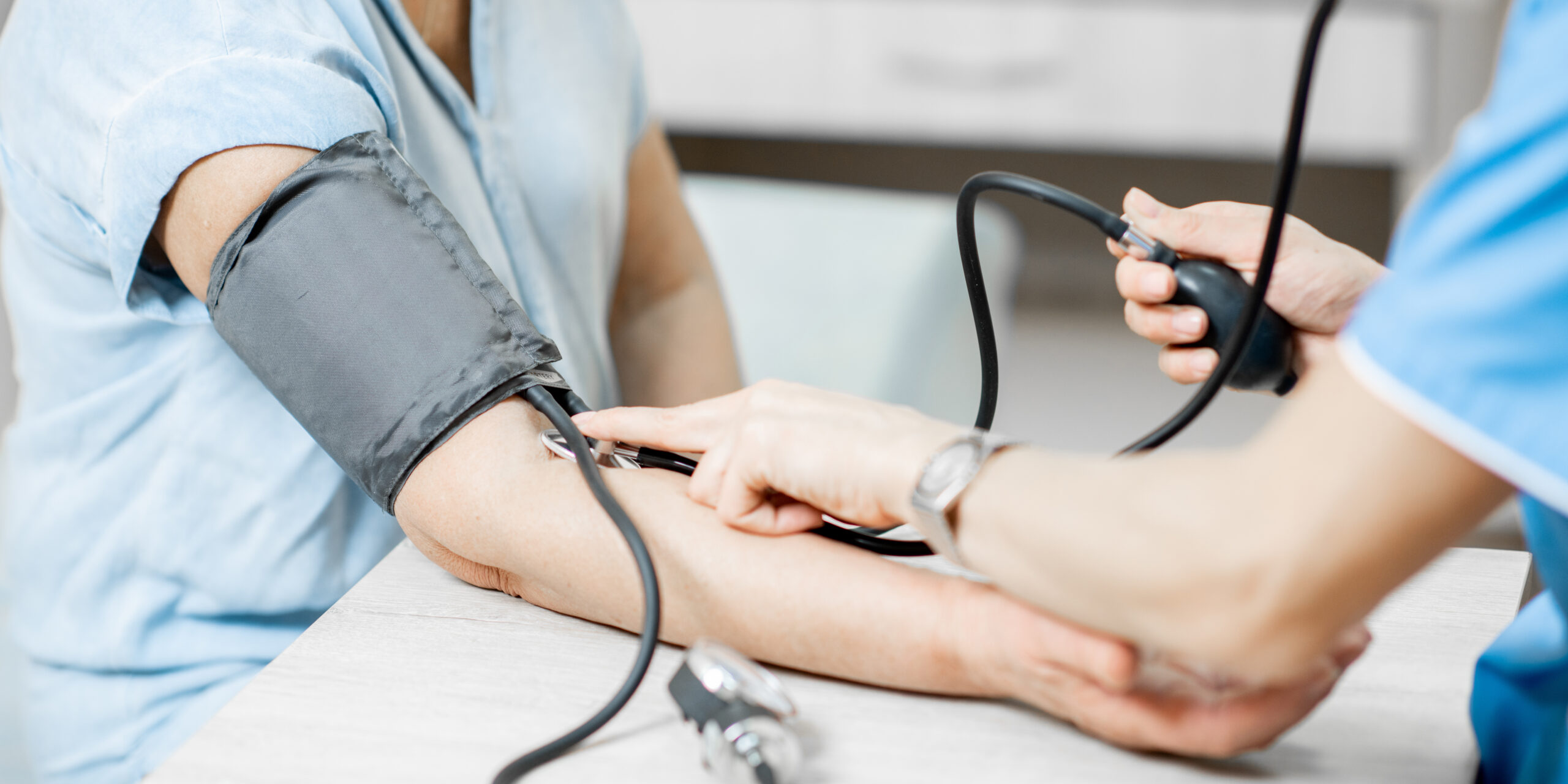
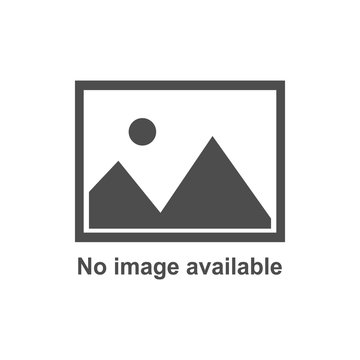
FEATURE – The ER of this Catalan hospital is finding great value in the application of Lean Thinking, which has already led to a dramatic change in its processes and to better care for patients.
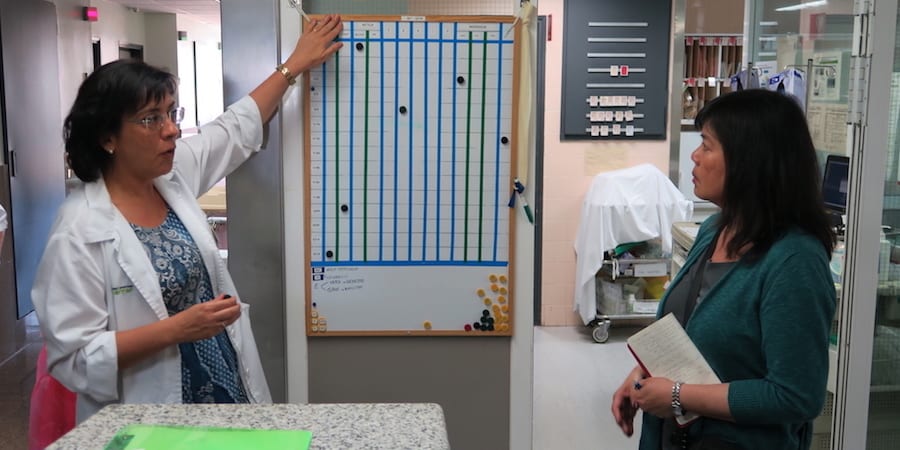
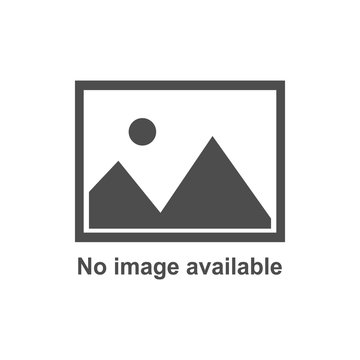
PROFILE – Lean is spreading like wildfire across the Catalonian healthcare sector, following a do-it-yourself model unique to this part of the world. Our editor met one of the practitioners who are making it happen.