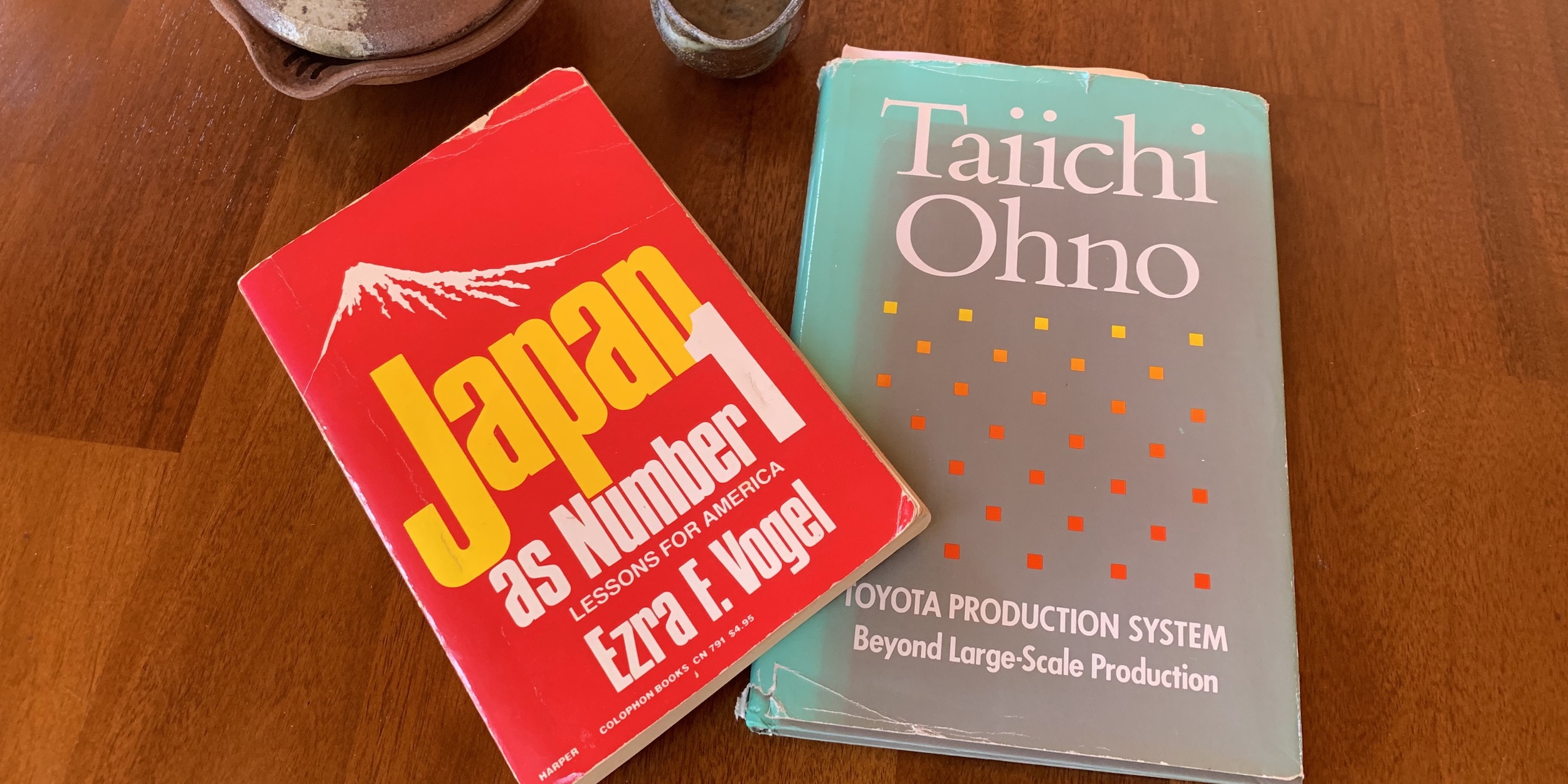
Two giants, two communities, one lasting thing
FEATURE – John Shook remembers the work of Ezra Vogel and Norman Bodek and discusses how, in their own way, each of their contributions help us to understand the Toyota Production System.
Words: John Shook, Chairman, Lean Global Network
Two extraordinarily influential individuals from two distinct but strangely adjacent communities died recently. Ezra Vogel was among the most prominent of an influential generation of scholars of post-WWII Japan. Norman Bodek was instrumental in bringing a specific tranche of profound knowledge from Japan to the English-speaking world. They died within ten days of each other, Norm on December 10 at age 88 and Ezra on December 20 at age 90.
I can’t claim to have known either man so well personally, though I met and interacted with them both. To my knowledge, they never met. They couldn’t have been more different as individuals. Vogel was a distinguished Harvard professor, at home in academia and diplomatic circles; Bodek was a gregarious recovered accountant who paved his own unique way forward, twisting, turning and pivoting by his street smarts. More importantly, along with countless others, I was deeply influenced by the work of each.
LEARNING FROM JAPAN
From meeting Professor Vogel in the 1970s to touring companies throughout Japan in 1977 to living in Japan and working for Toyota, I have spent my adult life trying to unpack the Japanese economic miracle and understand what actually happened in post-WWII Japan and why.
Vogel’s most famous book, Japan as Number 1: Lessons for America, has occupied a special place on my bookshelf since it was published in 1979. Professor Vogel honored us with a visit when my fascination with Japan was germinating as a student at the University of Tennessee. A visit from a prominent Harvard professor was a big deal to us; I soaked up everything he had to say. It wasn’t his visit alone that sent me packing to Japan, but hearing that the country was Numero Uno added just enough fuel to my fire to go see for myself.
Japan as Number 1 wasn’t his most important scholarly work, but it is a book that beautifully captured a zeitgeist of the moment. Japan was kicking our (American) butts in every field imaginable. Everyone was searching for the secret to it all. Theories upon theories were concocted and proffered. Number 1 was the perfect title and the book received massive attention while generating its fair share of controversy. Japan as Number 1 contributed mightily to the Japanese management boom – the management fad of the ‘70s and ‘80s. I personally was firmly swept up in it. By the time Japan’s economic bubble famously burst in the very early 1990s, I was fully embroiled in learning about the single most important contribution that emerged from the fad: Toyota’s production and management system.
Enter Norman and other early explorers, including Robert "Doc" Hall and Freddy Ballé among others, who recognized that the real gem amidst the Japanese management rough was indeed the Toyota Production System, AKA the Toyota Way. Norm founded Productivity Press and eventually published more than a hundred books on what came to be called “lean production”. Working inside Toyota in Japan, I never heard of any of the books – even Ohno’s books – until we started TSSC and began working with companies to learn TPS in the early 1990s. Only over time did I learn the role that books played in disseminating knowledge of TPS. While I would say that it’s a mixed record – simply because learning TPS is ultimately a learn-through-doing process – it is undeniable that books are important and the books Norman published in those decades were incalculably influential.
LEARNING FROM TOYOTA
From landing in Toyota City, the site of the birthplace of TPS, to teaching at the University of Michigan to leading LEI and LGN, I have spent the rest of my adult life unpacking what actually happened at Toyota and how others can benefit from learning from it.
Japan’s post-WWII miracle has been explained in many ways. From brilliant industrial policies to favorable social and cultural conditions to unfair trade practices to taking advantage of postwar American kindness to – and here is the one that remains intriguing – unique management practices.
Did the USA create favorable circumstances and provide substantial resources that enabled Japan to rebuild its economy? Absolutely. Did Japanese government and industry cooperate in ways that nurtured winners for decades following the war? For sure. Did monetary policy facilitate industrial and consumer behaviors that contributed to prosperity and growth? Hard to argue otherwise. Are there underlying cultural factors that enable corporations and industries to work in alignment and partnership for the betterment of all? Yes, I’d say so.
But, as dramatically as the world turned to fads of “Japanese management” in a desperate rush to copy the country’s success, the bubble burst. Suddenly and quite literally. Now, rather than “how can we emulate Japan’s success?” books are written about how to avoid the mistakes the country has made that have led supposedly to decades of stagnation.
I won’t try to offer my own explanation of the miracle and subsequent bubble burst here (though, briefly, I will state my view that the dismissive assessment of economists and other observers of the “lost decades” of stagnation says more about the dominant economic models of “success” – which is that growth is the only meaningful indicator – than they say about what has actually been happening on the ground in Japan; Japan’s population was sixth highest in the world when I first visited and is now eleventh and soon to be twelfth; its economy was the world’s second highest and is still the third highest); rather, I posit that the most impactful contribution to global business is TPS, or Toyota’s overall way of doing business.
In the time I have followed the company, it has suffered just one unprofitable reporting period (Tesla is now praised by finally showing its first profitable year), has consistently maintained market capitalization equivalent to its top five competitors combined (recently surpassed by Tesla; time will tell if that holds), and has usually dominated quality surveys and maintains easily the best residual values across a wide range of vehicle categories. As of this writing, it is the highest-selling automaker in the world (if you care about this as an indicator of performance).
Most importantly, that remarkable performance can be explained. Toyota has performed so well because of the way it works. Excellent Japanese companies have come and gone. Some perform well from time to time, year to year, then go on the skids for a while. Many have gone out of business. Direct cause and effect: Toyota performs so well because of its operations and management practices. Call it the Toyota Production System, the Toyota Way; call it lean thinking and practice – it is Toyota’s collection of thinking, doing, learning, improving, adapting that is the differentiator. And the good news is that other companies can learn from it. They can’t be Toyota (though many try to blindly copy pieces), but they can learn from it.
EZRA IN 2021
Here in 2021, we know what happened after Prof Vogel published his famous book. Regardless of the causes one may assign to Japan’s poor economic performance over the past three (3!) decades, we now know that the feared steady march of Japanese companies taking over industry after industry simply did not occur. Company names that instilled fear in American boardrooms 30 years ago became also-rans at best. Sony, having fallen from consensus at the most innovative large corporation in the world, to staid supplier to its one-time Korean rivals, is showing signs of leadership life again, but its future remains to be seen.
One Japanese multinational has consistently led its industry: Toyota.
In Japan, Toyota and its success have always been viewed as something of an inconvenient truth. Few Japanese would see the company as innovative or particularly attractive. Curiously, most don’t even see the company as one to emulate. Toyota is seen in Japan as a company that has merely done a good job of tapping into native Japanese characteristics such as diligence, loyalty, industriousness, frugality, and reliability. Any company could tap that well if they tried, or so many believe.
Companies considered worthy of emulation, on the other hand, are those that evolve beyond those old-fashioned character traits that may have worked well in the past but are surely inadequate to meet the dynamic needs of modernity. A brand image survey that Toyota conducted in the late 1980s revealed that Japanese and non-Japanese alike viewed the company as traditional, conservative, efficient, aggressive – nothing there to emulate other than its cash flow and balance sheet. This failure on the part of Japan to recognize the transformative power of Toyota’s way of working remains a tragic loss for the nation and its economy.
Prof Vogel himself never dove deeply enough into the machinations of business to single out Toyota for its special contributions. From his earliest studies of Japanese society to equally profound surveys of Chinese culture, my take on Prof Vogel’s efforts is that he believed deeply in the simple merit of mutual understanding, and that promoting respect across the vast cultural and mindset divides of “east and west” would benefit all. Actually, his work that most influenced me was Japan’s New Middle Class, a mind-blowing exploration at the time of the rise of the “salaryman” as a kind of modern-day samurai who fought bravely to bring the country into the new global economic wars of the 20thcentury; little did I know when I studied the book that just a few years later I would be living precisely the life that his ethnographic research described so well. Despite considerable evidence to the contrary, I still share his conviction in the power of mutual understanding. As he wrote in Japan as Number 1,
“On the American side, our confidence in the superiority of Western civilization and our desire to see ourselves as number one make it difficult to acknowledge that we have practical things to learn…I am convinced that it is a matter of urgent national interest for Americans to confront Japanese successes more directly and consider the issues they raise.”
The Japanese, for their part, so loved reading Vogel’s assessment of their position as “number 1” that the book remains to this day the all-time best-seller of a translated non-fiction work in Japan. Incredible. (Remarkably, Vogel’s book Deng Xiaoping and the Transformation of China occupies a similar place among translated works in China.)
NORM IN 2021
Here in 2021, we also know what happened after Norm Bodek began publishing his string of translated works about the Toyota Production System: years of enthusiasm, emulation, disappointment, delusion, hope, dedication, and, yes, some execution and learning along with a degree of undying passion. Books begat books.
From the earliest translated works – Ohno’s Toyota Production System, Shigeo Shingo’s A Study of the Toyota Production System from an Industrial Engineering Viewpoint Fukuda’s Managerial Engineering (less famous than the other two but no less profound in its content and far more accessible) – to the MIT work of Dr. Womack and others that culminated in The Machine that Changed the World and the avalanche of attention that followed, (I made an attempt at putting much of that into context in a previous post), to Toyota’s own evolution (including some improvement, some probable corruption and certainly much change) of its most ingenious invention and consequential contribution to business and society, the jury is still out on what humankind will make of it all.
ALL OF US IN 2021
As understood by enterprises and individuals who have undertaken the considerable effort to understand and to acquire the profound knowledge of learning through doing, the power of Toyota’s contribution is palpable, the potential great – the one thing of lasting value from the Japanese management craze. And the impact of that craze should not be underestimated. It spawned the quality movement, the excellence movement, and countless re-engineered and even reverse-engineered management theories. The need has been felt as long as we’ve had industrial organizations, and the need felt more so than now, as we enter this year ahead of us that is so ripe for the promise of intentional transition.
The “contribution”, to be clear, isn’t a matter of viewing Toyota the company as some sort of perfect platonic ideal for economic entities. Toyota as a company is riddled with countless “imperfections” and its future is highly uncertain. As is yours. But, the company’s way of working – including its management system that nurtures humans to work effectively in the service of common endeavor – and its system of frugal, non-wasteful use of all resources tap into the need we all feel for harmonic balance between the techno-mechanical and social needs of humans living and working under modern socio-economic conditions. For all of us, Toyota included, lean management is an aspiration (seemingly impossible to attain perhaps) to strive for with known means of navigating our ways forward.
Ezra and Norm belonged to adjacent communities – one studied Japan, the other promoted enterprise improvement. Ezra and the many proponents of the Japanese management boom set the table; Norm and his peers opened doors to achieving practical betterment. Together, we benefit from the legacy of one thing, at least, of lasting value – lean or Toyota’s way of working. Rest in peace, Ezra and Norm, and thank you for your efforts.
This article is being published simultaneously on our sister publication The Lean Post.
THE AUTHOR
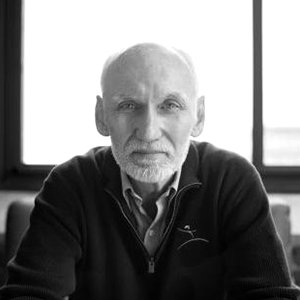
Read more
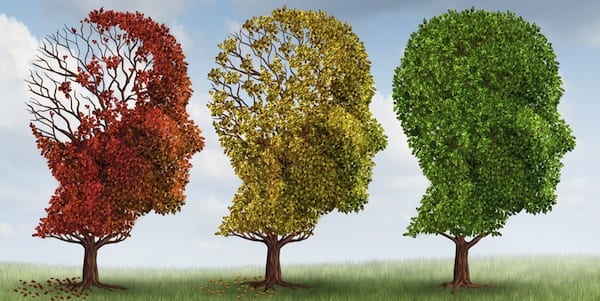
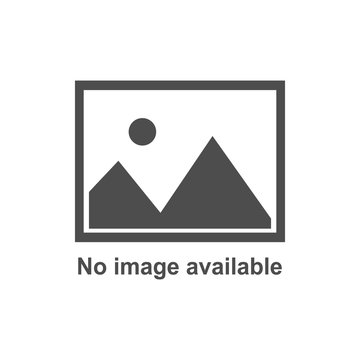
OPINION – How many times, in the early stages of kaizen events, have you thought about giving up? Hang in there. As frustrating as they can be, they will also teach you a lot, says our Danish colleague.
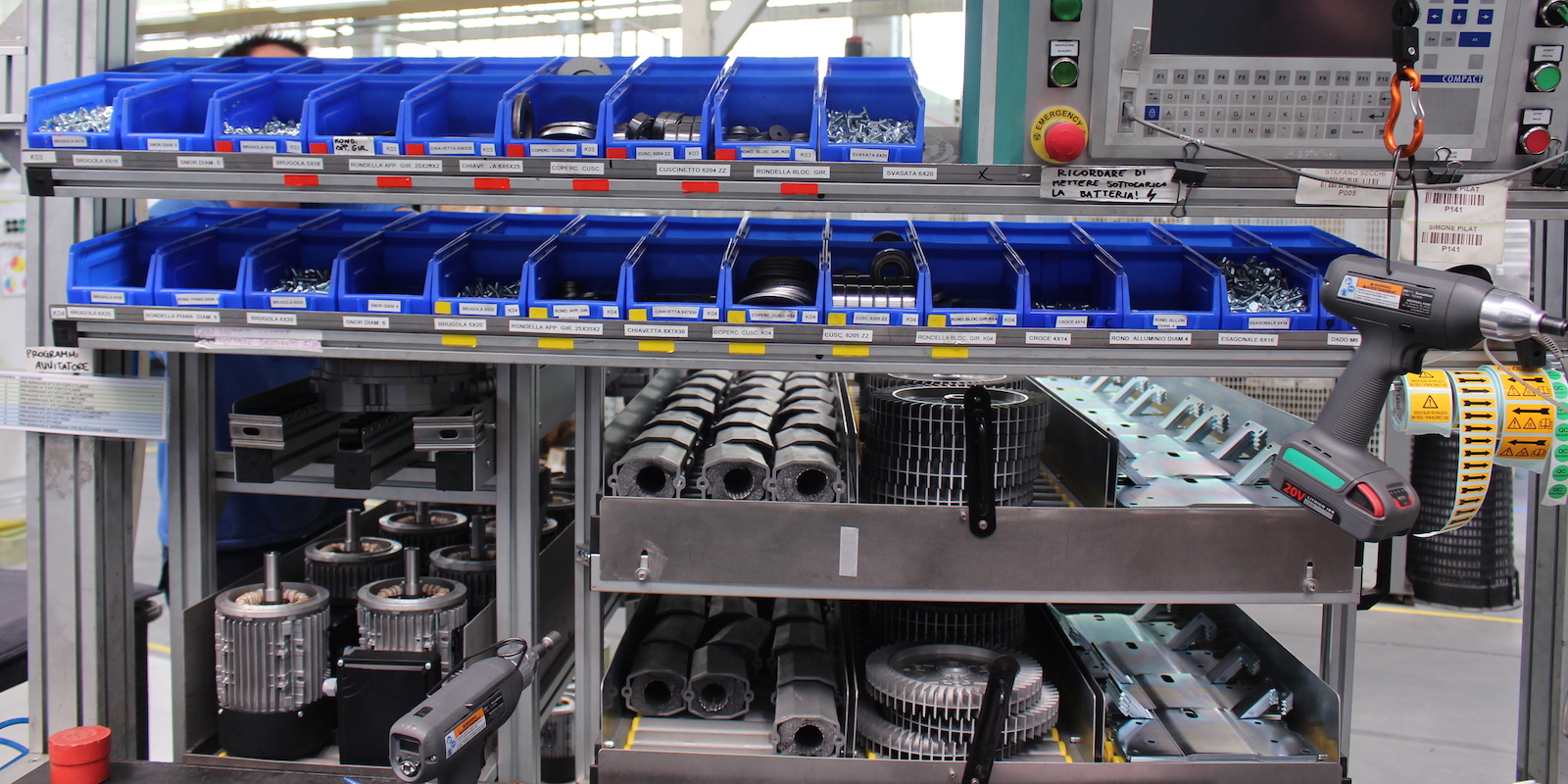
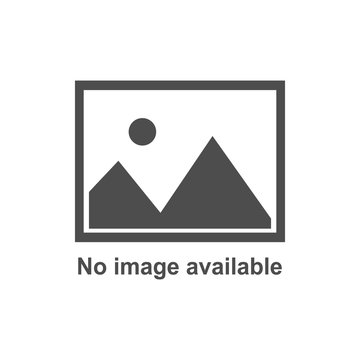
FEATURE – Two coaches from Italian company FPZ reflect on their role helping lean thinking spread across the company and its newly-acquired businesses.
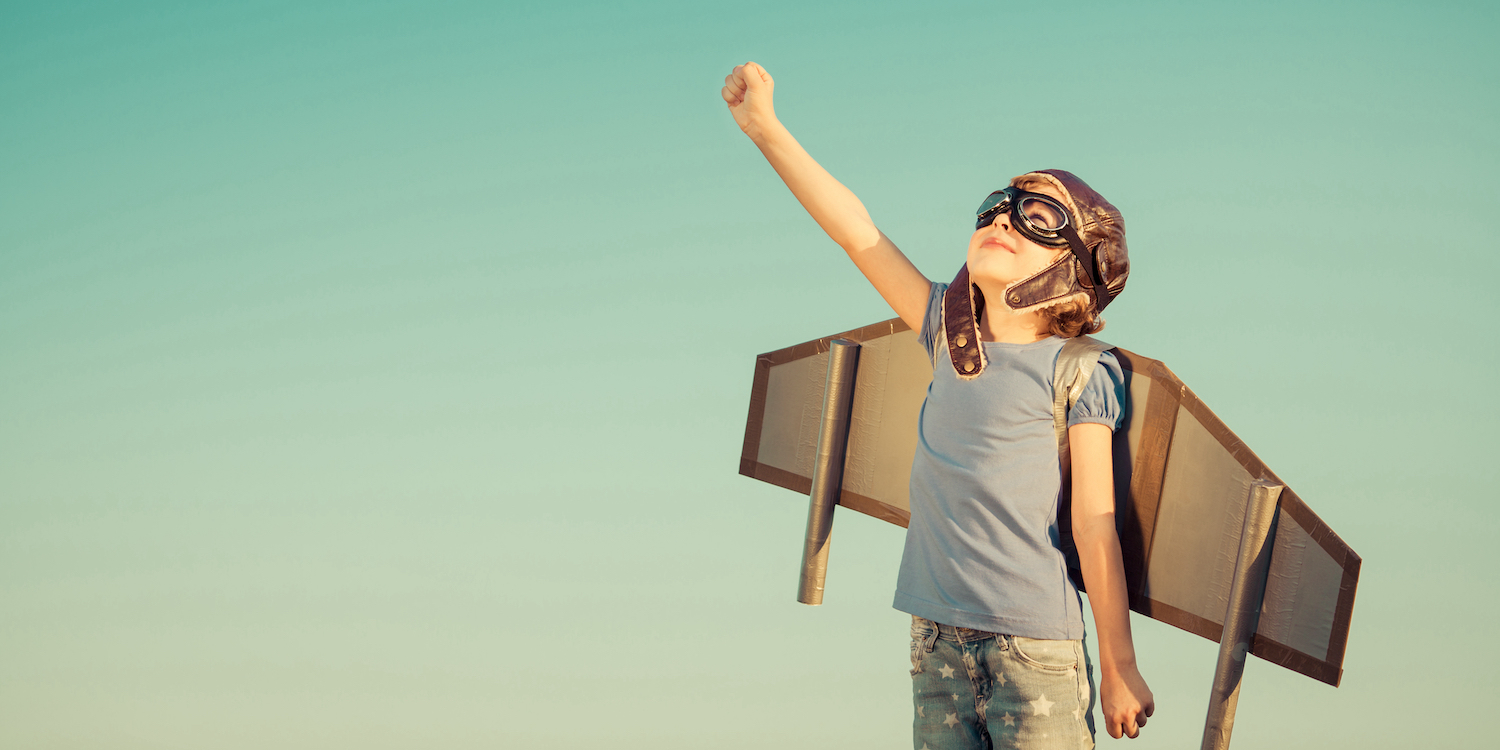
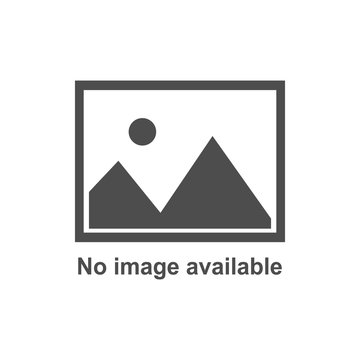
FEATURE – In this new series, the author will walk us through some uncommon ways to apply lean – with a particular focus on establishing productive and enjoyable relationships. In the first instalment, he introduces the concept of lean parenting.
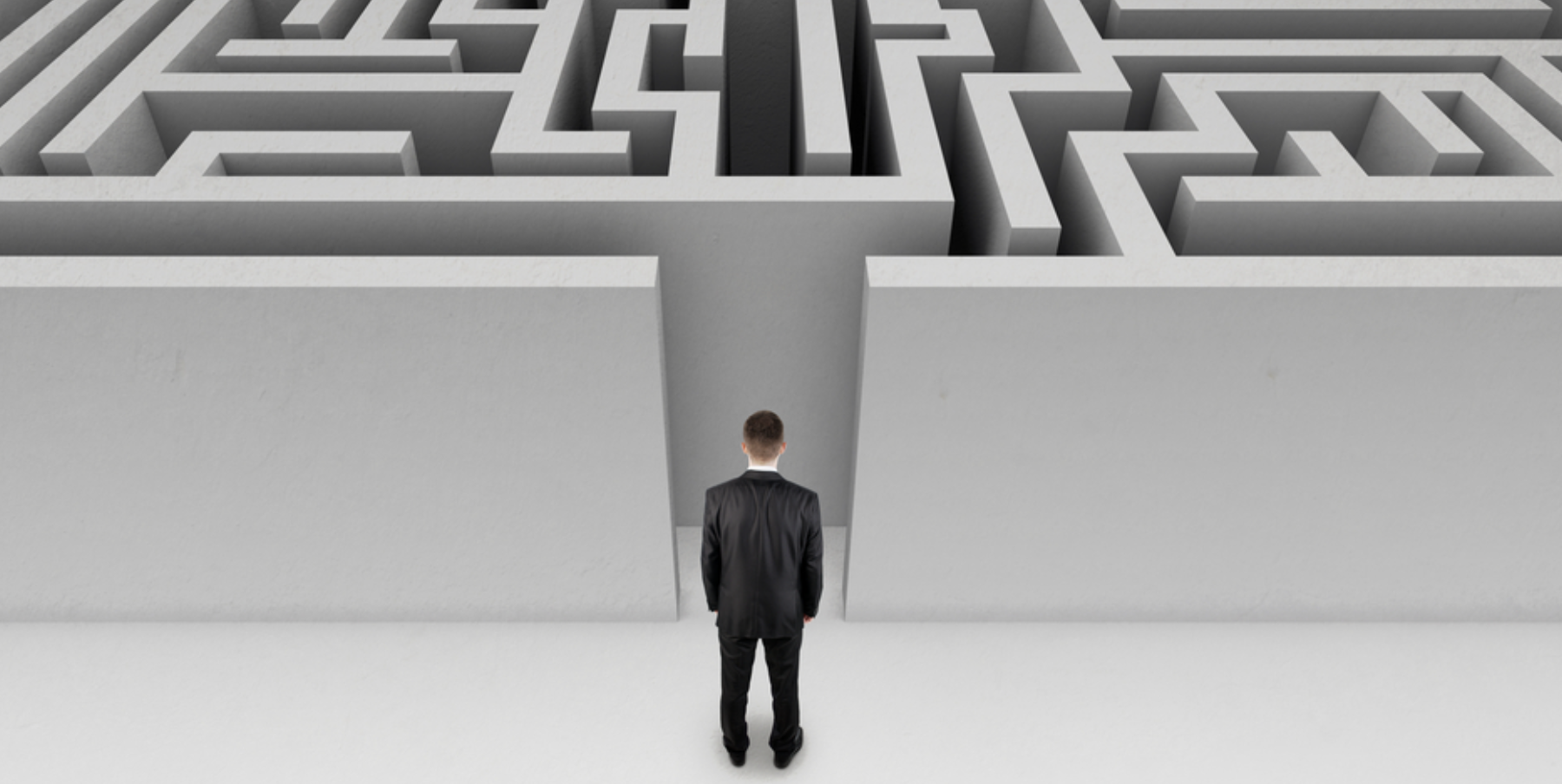
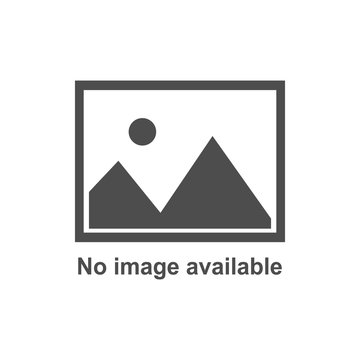
FEATURE – Using data from a recent piece of research on logistics, the author discusses how Lean Thinking contributes to a more efficient and effective way of dealing with problems.