
The criteria to decide on a pull system
FEATURE – Before you decide which method to use to establish pull, you must consider a number of factors. Here’s the things you should be paying attention to.
Words: Christoph Roser
In my previous post, I offered an overview of the different types of pull system available to lean organizations. A natural next step would be to select one and get started. However, there are a few criteria to take into consideration before you can select the flavor of your pull system. Let’s see them.
MAKE-TO-STOCK VERSUS MAKE-TO-ORDER

The most important element to consider is whether your product is make/ship-to-stock or make-to-order. Is the item produced, transported, or purchased before the customer order comes in or only after it does? High-volume-low-mix and low-volume-high-mix is a similar concept. The key question is the same: do you aim to always have a product in inventory (make-to-stock) or do you only produce when an order comes in and have the customer wait (make-to-order).
Make-to-stock and make-to-order have very different goals. Make-to-stock aims to always have parts available, while requiring as little inventory as possible. You typically produce large quantities of identical products (high-volume-low-mix). In this scenario, a customer order implies the delivery of an item in stock, which is immediately replenished by another, identical item. Items are produced in advance, which means the customer (ideally) doesn’t have to wait.
With make-to-order, production only begins after a customer order. You usually have a backlog of open orders waiting to enter the pull system, which can also be sequenced according to priority. In make-to-order set-ups, completed parts are usually delivered right after production and you have little or no finished-goods inventory. Hence, with make-to-order, the goal is to minimize the time between receiving the order and delivering the product, while keeping the system utilization reasonably high. You typically produce many different products in small quantities or even completely unique items (low-volume-high-mix). Only after a customer order does production start. The customer always has to wait for delivery after making an order.
One important effect of this is the level of detail you need for controlling your pull system: for make-to-order production, you only need a generic inventory limit across all parts within your pull loop (they all contribute to the same inventory limit). For make-to-stock production, however, you have to set a limit separately for every single part type in your pull loop.

It is also possible to combine make-to-order and make-to-stock in the same system. In this case, you need a pull system capable of handling both situations. This mix of make-to-order and make-to-stock is usually a combination of two different pull systems, often kanban and CONWIP.
PRODUCTION/DEVELOPMENT VERSUS PURCHASING
A second important distinction is related to the capacity limits of your system. Are you producing/developing or are you purchasing items from an external supplier? Can you get all the items you want at once (purchasing) or do you have to make one at a time (development or production)? Do you have to worry about the production sequence of your items or is it okay to just get them all at once?
Production systems usually produce one item after another. The sequence of your orders is therefore relevant. Your production system has a limited capacity, which could be measured in parts per day. If you want to produce too much at the same time, your production system gets clogged up – some products may be completed early, others may take longer.
However, if you order different goods from different suppliers, you need not think about the sequence of your order. You don’t think if you should order parts A from supplier X first and then parts B from supplier Y. You just order them all at the same time. Even if you order multiple parts from the same supplier, you rarely worry about the sequence of the order. Instead, you let the supplier figure it out.
FLOW SHOP VERSUS JOB SHOP

Another, less important factor – relevant only to production but not to purchasing – is if you have a job shop or a flow shop (the latter being much easier to handle). If you can turn your system into a flow shop, it will almost always be beneficial because you will only need to control the first process while the others will be usually controlled automatically through a FIFO (First-In-First-Out).
If, however, you have a job shop, you need to manage not only what to produce with your system but also every process in the job shop. POLCA specializes in job shops, but requires more effort because job shops in general require more effort. For mixed systems that have some elements of a flow shop and some elements of a job shop, you may choose which concept fits your system better. Have you arranged your processes in a sequence that fits most products? Then it is probably closer to a flow shop. Were you unable to find a sequence since so many different products have different sequences? Then it is probably closer to a job shop.
HIGH DEMAND VERSUS LOW DEMAND
A smaller factor, which only matters in make-to-stock or ship-to-stock environments, is the demand of a particular item. Do you sell large quantities or only a few items? Judging if an item is high demand or low demand is relative to your system and may vary greatly from product type to product type. In particular, it may influence kanban systems to decide what variation of kanban you should use.
SMALL AND CHEAP VERSUS EXPENSIVE OR LARGE
A final consideration for make-to-stock systems is the cost and effort of having the item in inventory. Most times, this is largely based on the value and size of the item. If the item is expensive, you probably don’t want to tie up too much capital in excess inventory. If the item is large, you probably don’t want to use up too much storage space. In both cases you may invest additional effort to reduce the quantity and hence reduce the tied-up capital or required storage space. For example, if you make cars, you don’t want to put too many expensive and bulky engine drive trains on stock.
If the items are neither large nor expensive, you probably don’t worry too much about your inventory so long as you have enough. In this case, having a bit more material than needed is usually nothing to worry about. Here, you may choose a method that might not have the smallest possible inventory limit but makes for an easier-to-manager pull system.
In my next article, I will use this information to provide more guidance on what pull system to use and when. Until then, stay tuned, and go out and organize your industry.
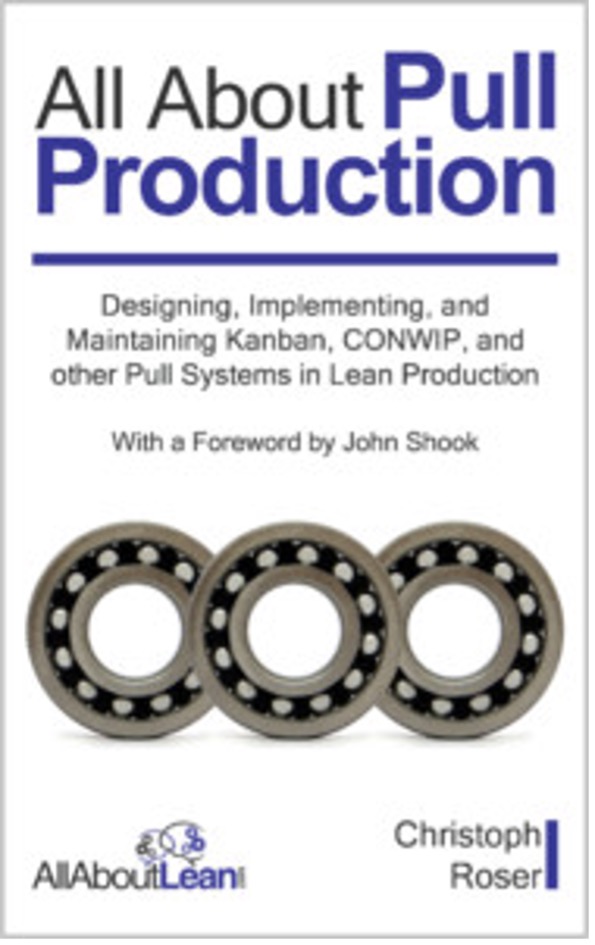
This article, originally published on All About Lean, is loosely based on Christoph’s new book All About Pull Production: Designing, Implementing, and Maintaining Kanban, CONWIP, and other Pull Systems in Lean Production, a practical guide for anyone looking to implement pull systems.
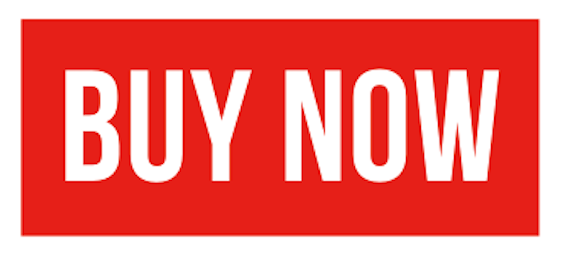
THE AUTHOR
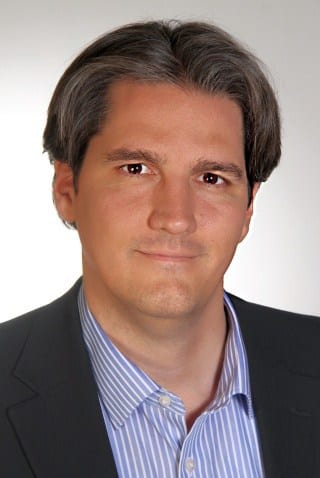
Christoph Roser is Professor of Production Management at the Karlsruhe University of Applied Sciences. He writes based on decades of experience in implementing, researching, and teaching lean manufacturing, including five years working at and researching for Toyota in Japan.
Read more

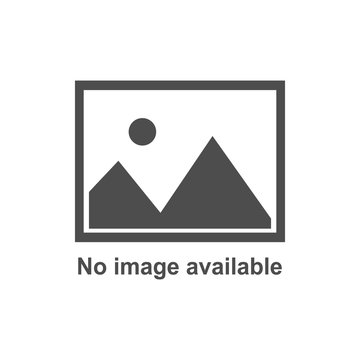
FEATURE – A Dutch transmission system operator is using Lean Planning – built around the Last Planner System – to better manage its complex infrastructure projects.

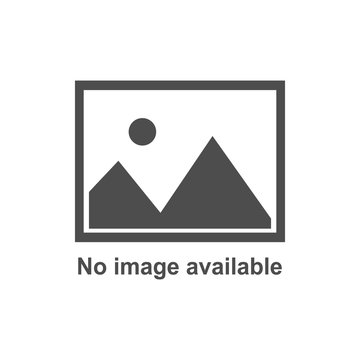
FEATURE – What started as the idea of two friends to meet up and discuss their lean journeys turned into a regular get-together of lean practitioners in the Cape Town area. Another example of the importance of sharing.

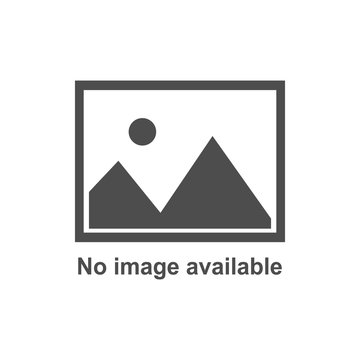
WOMACK’S YOKOTEN – The author discusses the benefits that the many family businesses making up our economies can harness from embracing lean management.
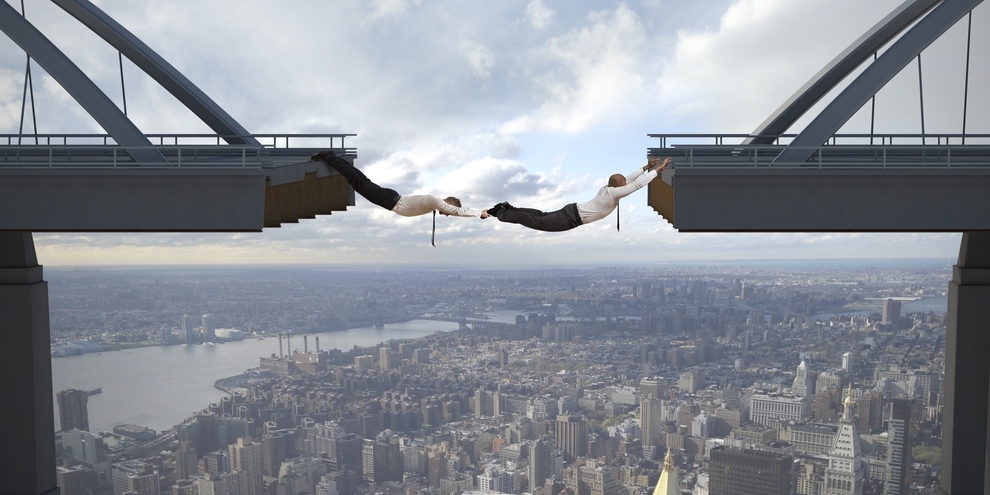
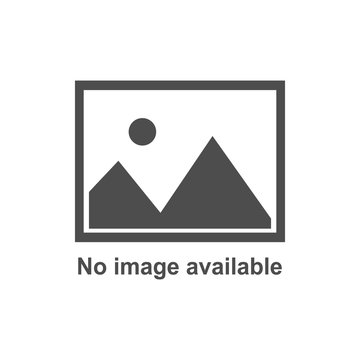
FEATURE – What is the role of middle managers in a transformation and how can we ensure they can fulfil that role – instead of being blamed for the failure of the initiative and even excluded from it?