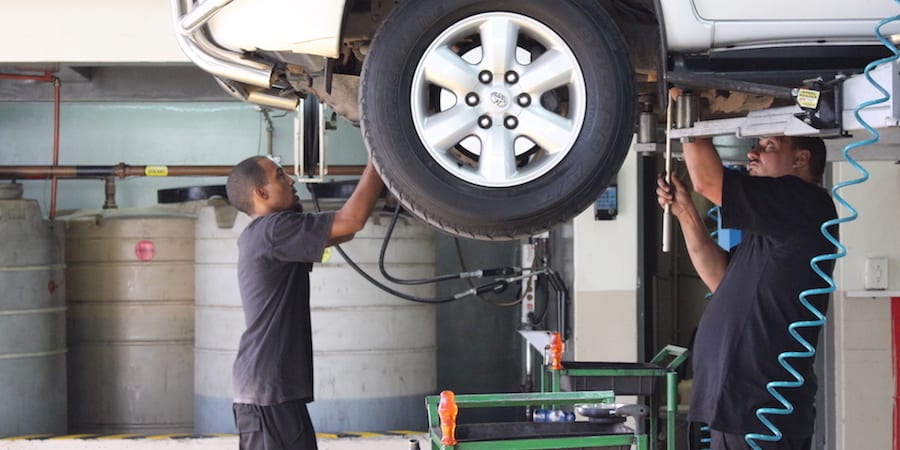
The people-led lean turnaround of a chain of car dealerships
DOCUMENTARY – In PL’s first ever documentary, we share the story of a chain of car dealerships in Africa. Watch and learn how people development and lean leadership made for one of the best turnarounds you’ll ever encounter.
Words and footage: Roberto Priolo, Editor, Planet Lean
Last May, I travelled to South Africa and Botswana to visit the Halfway Group, a chain of car dealerships that is achieving an extremely successful lean transformation.
At Halfway, lean thinking has been applied to processes of all kinds, but the two most important applications of its principles and techniques are certainly in Sales and in Aftersales (repairing and servicing vehicles).
The results achieved by the organization in both areas are unbelievable. After the introduction of lean, car sales at Halfway Ottery in Cape Town, for example, grew 400% in six years, while the number of cars being serviced in a day more than doubled (thanks to a very innovative system to service cars, based on one-piece flow). The results at Halfway Ngami (in Botswana) have been just as impressive, with the work of one the workshop’s bays seeing a 280% increase in efficiency with the introduction of the lean system. Overall, the Botswana dealership has seen a 111% increase in average monthly profit between 2013 and 2015. I was also extremely impressed by the Production Center in Johannesburg (where new and used vehicles are prepared for sale and delivery to customers), which has completely transformed itself in just over a year after the culture and management attitudes shifted towards lean. Such results and figures should be enough to convince every other dealer in the world (or maybe every company in general) to give lean a try.
But what made lean so successful here? Across Halfway, PDCA, problem solving and kaizen are built into the mindset of the business, with people coming up with ideas for improvements and managers encouraging them to take more and more initiative. Like any successful cultural shift, the Halfway transformation was possible thanks to forward-looking and humble lean leadership – with effective coaching and sound strategic guidance provided by Terry O’Donoghue (a former VP with Toyota South Africa) and Dave Brunt (the CEO of the Lean Enterprise Academy).
During my trip to Africa, I have met many of the people who are making this transformation happen, and I have been very touched by their stories. What struck me – and you will learn this today – is that the reality in which they work (where poverty, deprivation and crime are often rampant) ultimately represents the fuel of this turnaround. Struggle is at the heart of the lean journey of Halfway: nowhere more than here have I seen so many people succeed against all odds.
I left Africa humbled and inspired, and decided to share with you all the faces, voices and stories of the wonderful people I have met. That’s why we created the documentary you can see here. I know that this product – a first for Planet Lean – is going to challenge the low attention span of the online audience, but I am hoping you will still take the time to watch this documentary… perhaps on a weekend (between episodes of Game of Thrones maybe), or during your morning train ride to work. I promise you this is a story that will not leave you indifferent.
This documentary is meant to be an introduction to the Halfway story, and a way for you to get to know the people who are bringing change to the organization. You are going to read a lot about them over the next few months: starting in October, Planet Lean will publish a monthly article on Halfway. So, if you enjoy the documentary, make sure you come back the first week of each month to learn more about this extraordinary lean transformation.
Happy watching!
THE AUTHOR
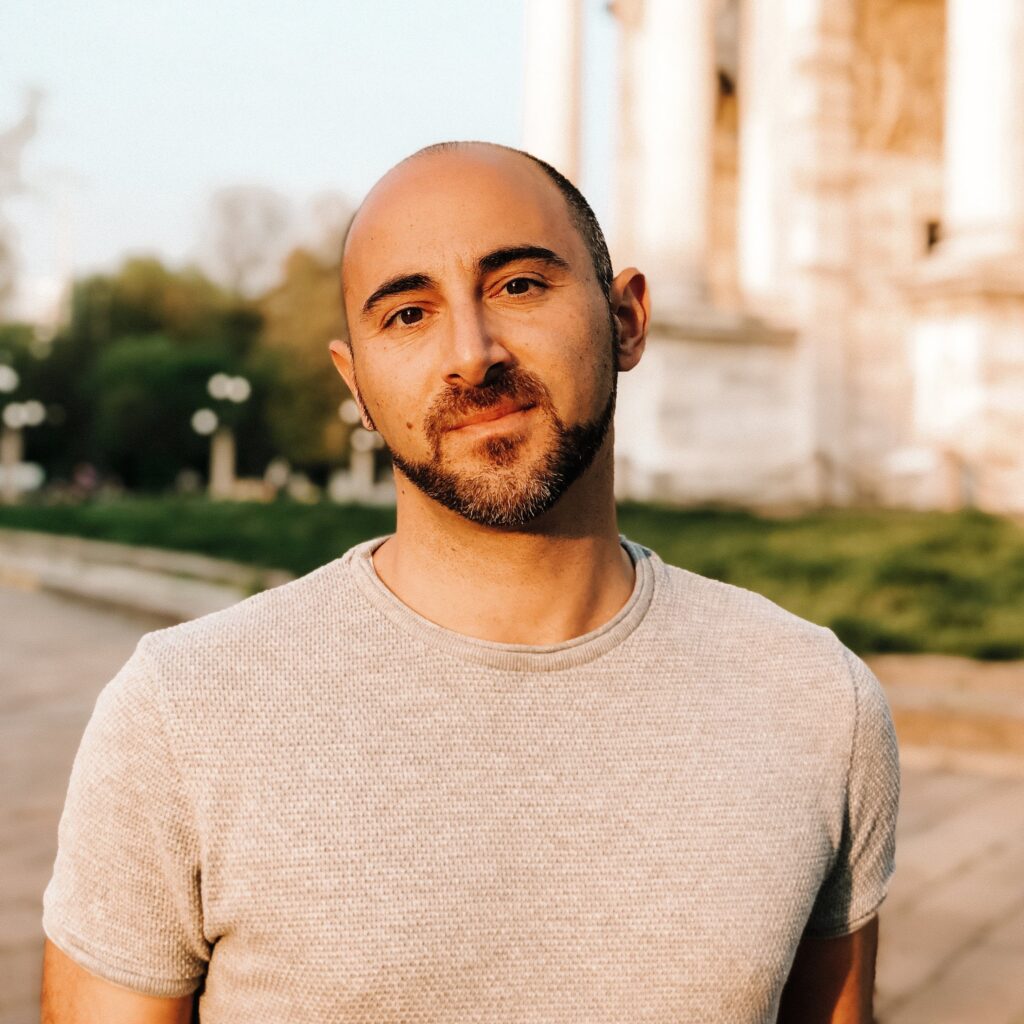
Read more
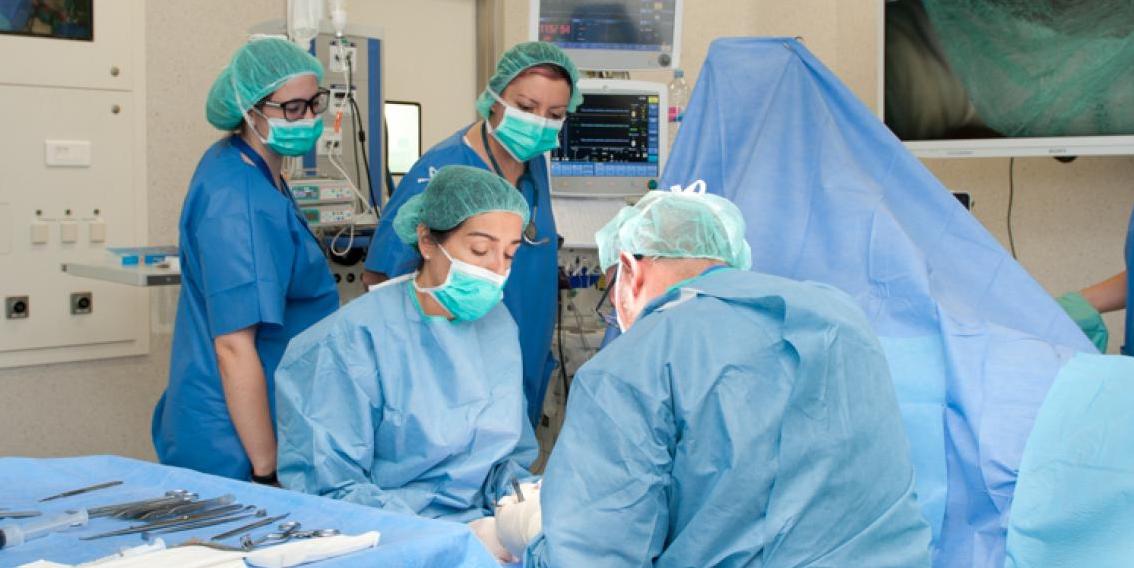
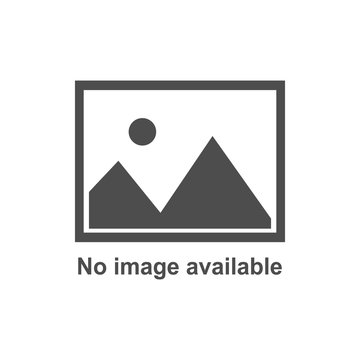
CASE STUDY – The Hospital de Bellvitge in Barcelona is relying heavily on hoshin and Kata to create a working environment based on collaboration and joint problem solving.
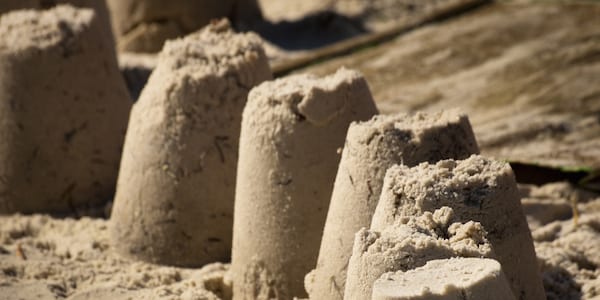
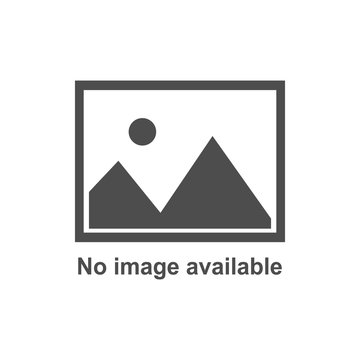
FEATURE – In a transformation, should we spread responsibilities across the business or go for a centralized Lean Office? For their second piece, our Polish colleagues look at what they have learned on the field.
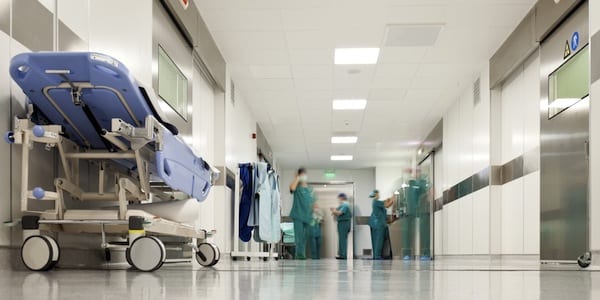
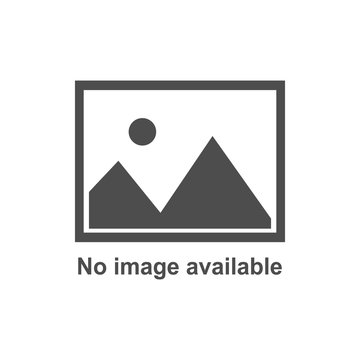
CASE STUDY - What does having a new “true north” mean? Following the merger with a large group, cancer center IOV is looking to seamlessly spread its lean management system to new operations and facilities.
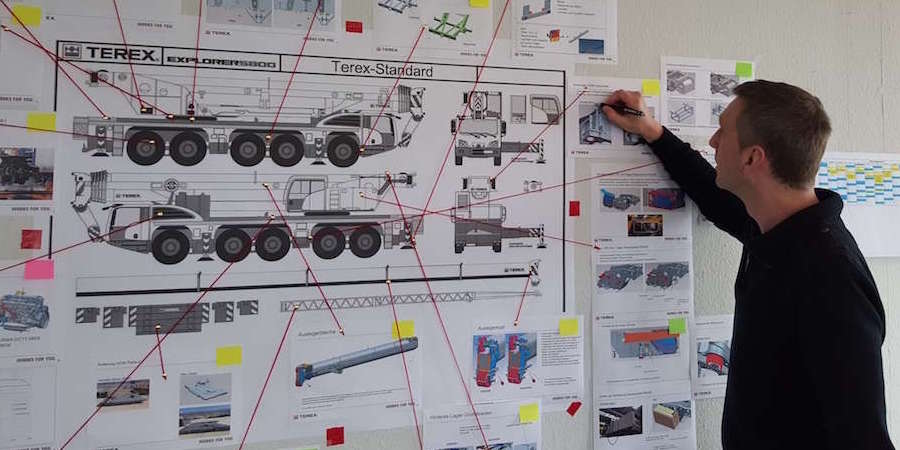
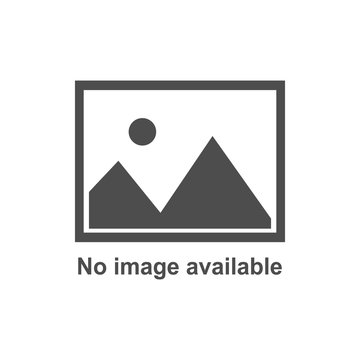
NOTES FROM THE GEMBA – In the past 15 months Terex Cranes has successfully initiated a lean transformation. Follow Catherine Chabiron on her gemba walk to see what this large company is doing to put learning at the heart of its activities.