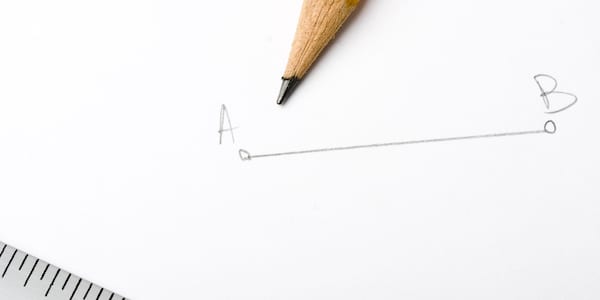
Rely on early adopters to launch your lean implementation
COLUMN - What does it take to start a lean implementation? People often hesitate, blaming lack of preparedness at different management levels. Truth is, all you need is two front line people who are committed.
Words: Cécile Roche, Lean Director, Thales Group
Recently, one of my colleagues went through an experience that, he told me, felt like one of the worst in his professional life: presenting to the big boss - the meaning of lean in engineering.
There was a time at the company when the words “lean” and “engineering” could not be pronounced in the same sentence. For some reason, the boss was completely reluctant when it came to this topic. That is, until a few weeks prior to my colleague’s presentation, when the President announced that lean engineering would be one of the levers for the company’s competitiveness.
The day of the presentation came, for which my colleague had prepared ten slides and put together a list of reference books. A few minutes into his talk, he pronounced the word “kaizen.” Game over. His presentation ended there. “Enough with your japoniaiseries! [The word translates in English as “Japanisms”] I don’t want to hear more,” the boss said.
In lean, we normally say that every problem or mistake is an opportunity to learn. So, what can we learn from this story? That it is pointless to explain to people what we think is important; instead, we should focus on what is important to them. This doesn't mean coming up with something new or, worse, with a lie. It means reframing the issue and looking at it from a different perspective.
People often tell me that they can't start their lean journey because of management: top managers only want to cut costs, middle managers only focus on waste, while front line managers just want to be left alone and for the teams to be able to do their job.
My reflection on this is: no need, no lean. Lean is not a methodology we apply because it is fashionable to do so, or because people say we need to, but an approach for sustainable competitiveness achieved through a deep focus on customer value and people development, and through a systematic drive towards right first time (all of which requires a big change in behaviors).
However, let us suppose that sustainable competitiveness is indeed an issue for your company and that lean is identified as the way forward. Do you wait for the stars and planets to align? Do you wait for top management to be enthusiastic, middle management to be convinced, front line management to be ready to challenge themselves, and teams to be able to experiment? Er… Personally, I have never seen such a favorable situation materialize. Never.
To link back to the question I pose in the title of this article, how many dots do you need to draw a straight line? Many seem to be cautious and wait until several dots are there to guide them. But as we all know, all you need to draw a perfectly straight line is two dots.
If across line management you have two people who are ready to really try for themselves, then I think you can start. Starting means to find a performance that needs improving and to change your point of view on how to approach it. I don’t know how improvement can be achieved specifically, but listening to people and customers, thinking flow and accepting all the problems discovered as opportunities to learn will surely bring dramatic behavioral changes and great progress in performance.
The question is, are you on that line and ready to start by yourself?
THE AUTHOR
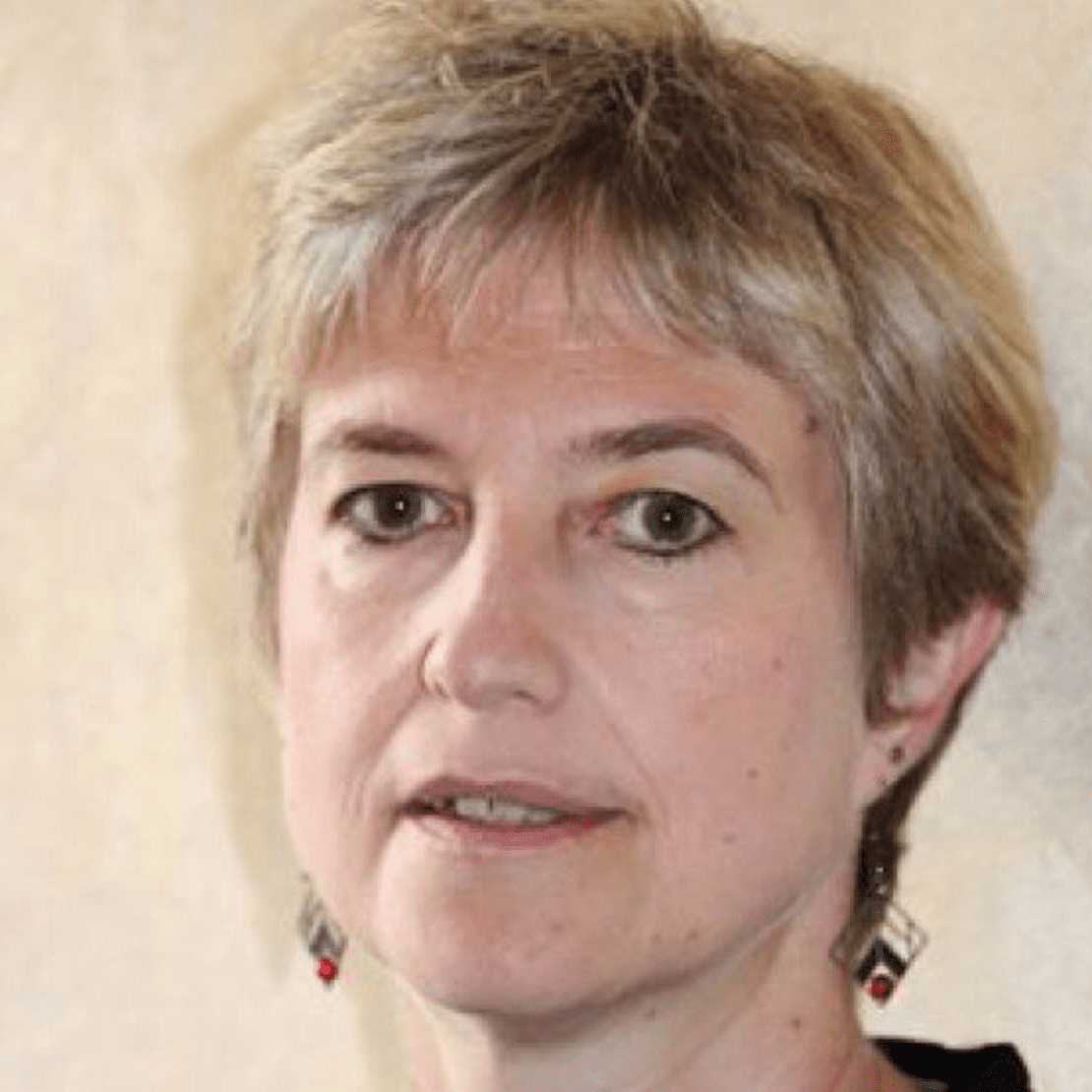
Read more
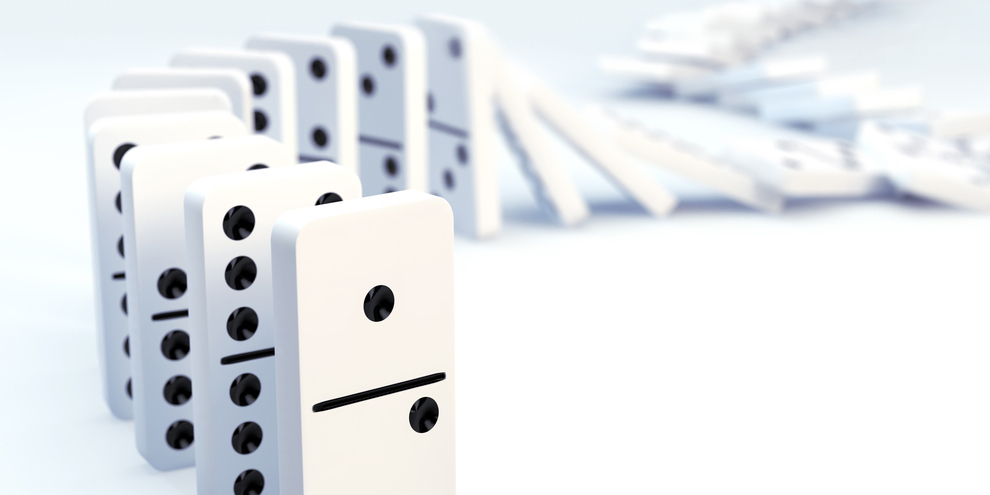
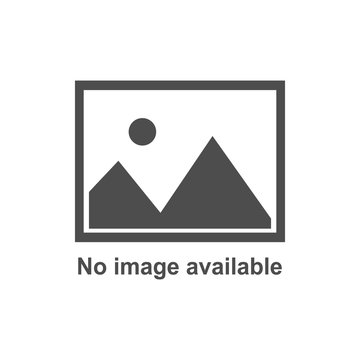
FEATURE – The only way for lean to succeed is to change a leader’s behavior so the rest of the organization will change too and people get the support they need to become problem solvers.
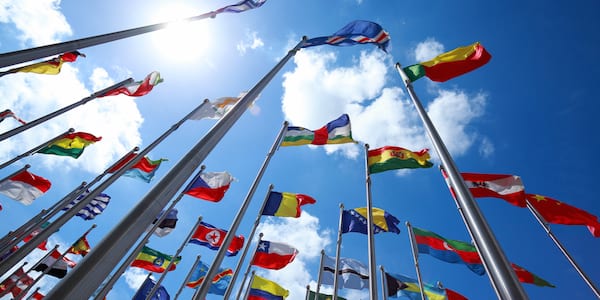
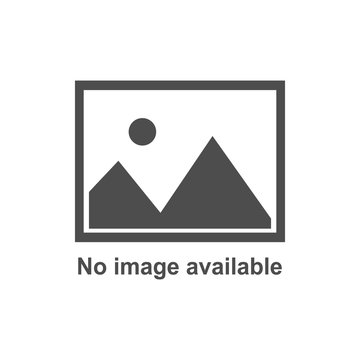
ARTICLE - Are some national cultures better suited to implement lean thinking? This article, based on research on 45 Volvo factories, reflects on the role of local cultures in the rollout of a corporate lean program.
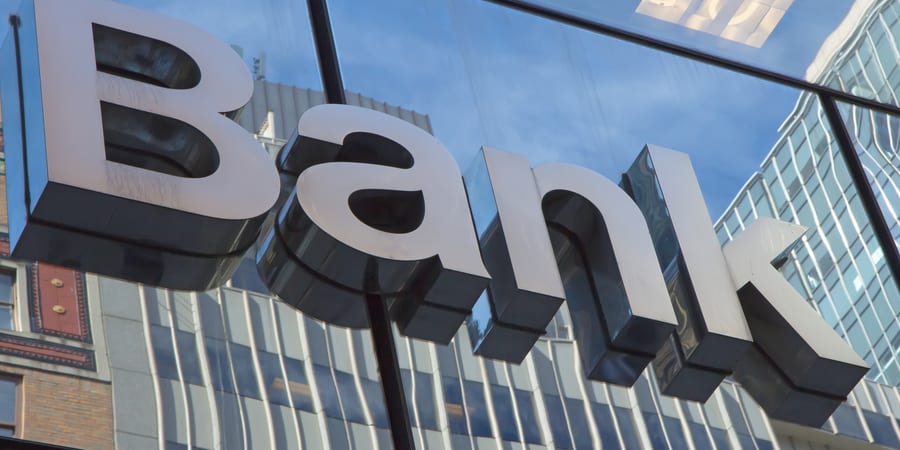
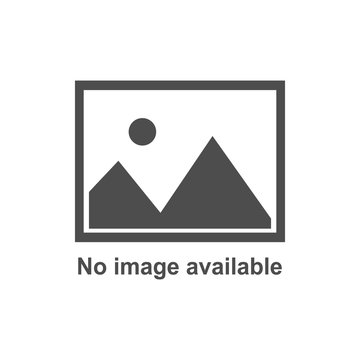
INTERVIEW – Planet Lean interviews Silvia Cespa of Italy’s Banca Nazionale del Lavoro, a bank that boasts one of the most advanced IT departments in Europe. How did it get there? Through a six-year transformation towards lean banking.
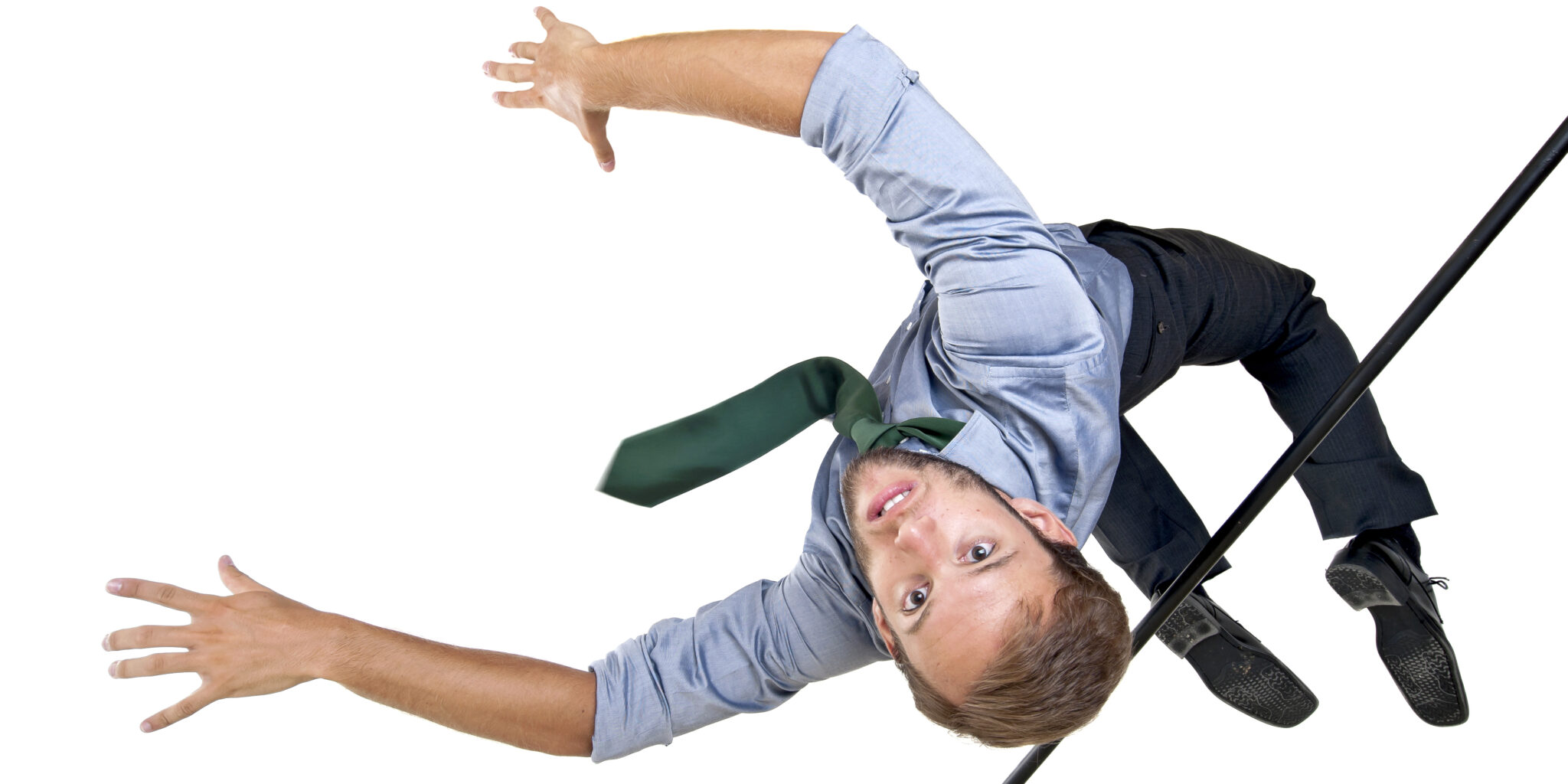
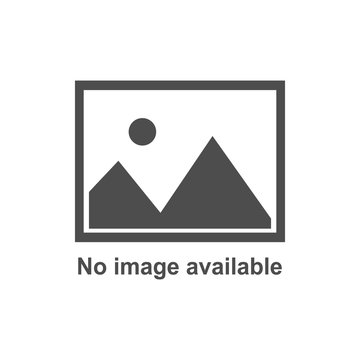
FEATURE – Based on their experience supporting the stellar growth of Aramis Group, the authors discuss the role of leaders in shaping minds and behaviors and constantly challenging themselves to be the best example they can.